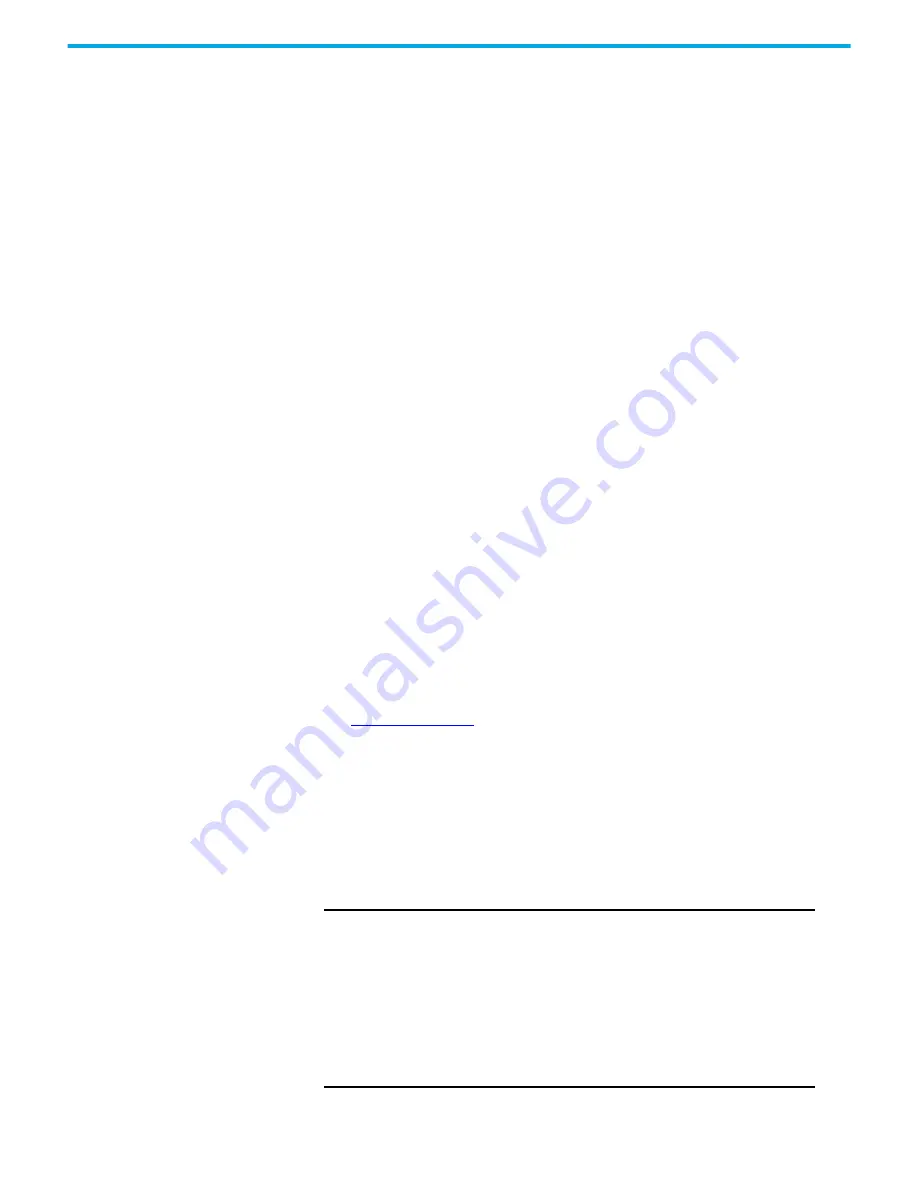
Rockwell Automation Publication 35-UM001A-EN-P - May 2022
41
Chapter 2 Install the Armor PowerFlex Drive
Wiring and Workmanship
Guidelines
In addition to conduit and seal-tite raceway, it is acceptable to use cable that is
rated Tray Cable Exposed Runs (TC-ER), for power and control wiring on
Armor PowerFlex installations. The National Electrical Code (NEC) and
NFPA 79 outline the following guidance for installations in the USA and
Canada.
In industrial establishments where the conditions of maintenance and
supervision verify that only qualified persons service the installation, and
where the exposed cable is continuously supported and protected against
physical damage, by using mechanical protection, such as struts, angles, or
channels, Type TC tray cable that complies with the crush and impact
requirements of Type MC (Metal Clad) cable and is identified for such use with
the marking Type TC-ER (Exposed Run) shall be permitted between a cable
tray and the utilization equipment or device as open wiring. The cable shall be
secured at intervals not exceeding 1.8 m (6 ft) and installed in a good
workmanlike manner. Equipment grounding for the utilization equipment
shall be provided by an equipment grounding conductor within the cable.
While the Armor PowerFlex drive is intended for installation in factory floor
environments of industrial establishments, the following must be considered
when locating the Armor PowerFlex drive in the application:
•
Cables that include control voltage cables, for example, 24V DC and
communications, are not to be exposed to operator or building traffic on
a continuous basis.
•
Location of the Armor PowerFlex drive to minimize exposure to
continual traffic is recommended. If location to minimize traffic flow is
unavoidable, other barriers to minimize inadvertent exposure to the
cabling must be considered.
•
Cables must be routed to minimize inadvertent exposure and/or
damage.
•
If conduit or other raceways are not used, we recommend that strain
relief fittings be used when installing the cables for the control and
power wiring through the conduit openings.
•
Power cabling, such as three-phase, source brake, and dynamic brake,
must be kept at least 150 mm (6 in.) away from the EtherNet/IP network
and I/O cables to avoid noise issues.
See
for additional cable location requirements.
The Armor PowerFlex drive is meant to be disconnected and replaced after
proper lockout/tagout procedures have been employed.
Electromagnetic
Compatibility (EMC)
The following guidelines are provided for EMC installation compliance.
Cabling and Grounding
IMPORTANT
For EMC compatibility, the motor cable connector that is selected
must provide good 360° contact and low transfer impedance
from the shield or armor of the cable to the conduit entry plate at
both the motor and the Armor PowerFlex drive, for electrical
bonding.
The motor cable must be kept as short as possible to avoid
electromagnetic emissions and capacitive currents. CE
conformity of Armor PowerFlex drive with EMC Directive does not
confirm that the entire machine installation complies with CE
EMC requirements.