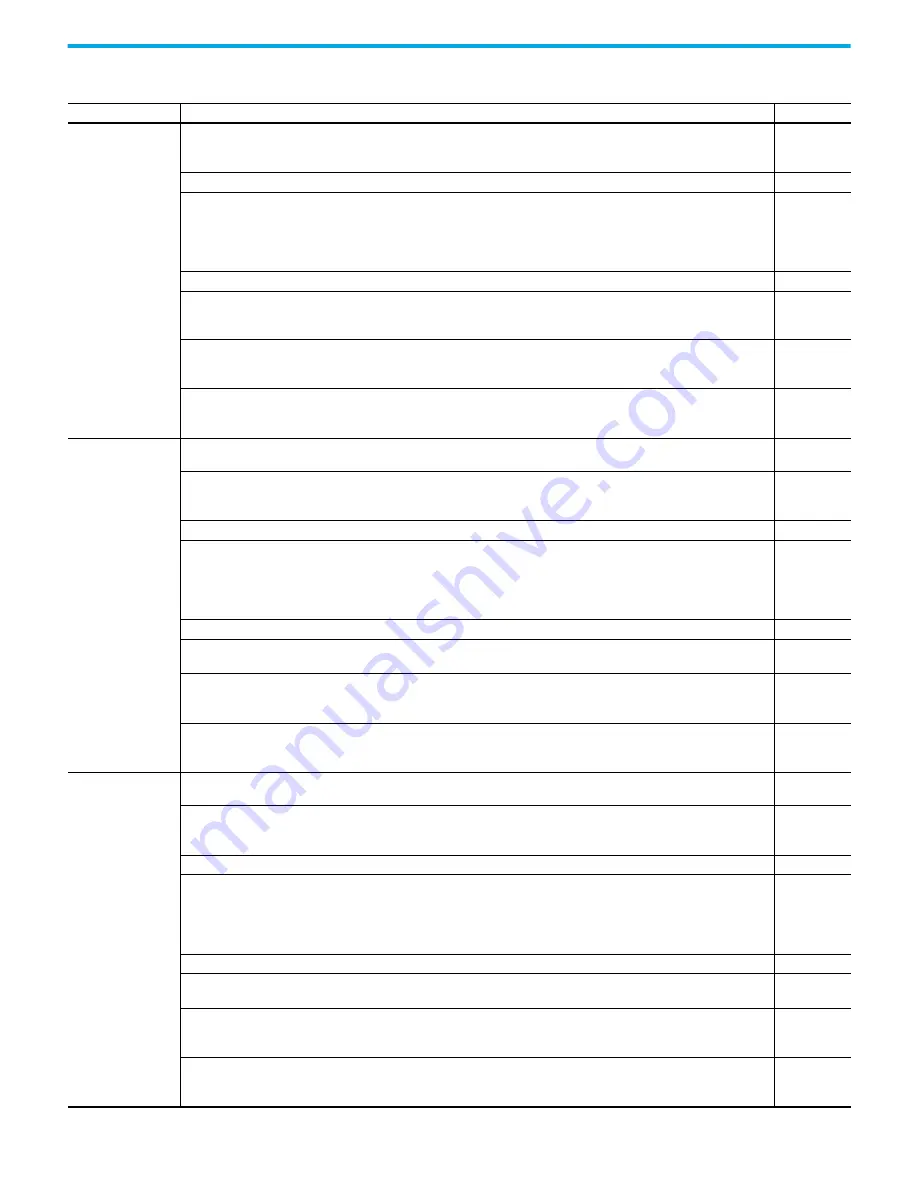
212
Rockwell Automation Publication 35-UM001A-EN-P - May 2022
Appendix A Integrated Safety Instruction Validation Checklist
Table 98 - SS1 Instruction Checklist
Test Type
Test Description
Test Status
Normal Operation
Initiate a Start command.
• Verify that the machine is in a normal machine run condition
• Verify proper machine status and safety application program status
Operate the machine at the desired operating system speed.
Set up a trend with expected time scale and the following tags to graphically capture this information:
•
SFX_Name
.ActualSpeed
•
SS1_Name
.SpeedLimit
•
SS1_Name
.DecelerationRamp
•
SS1_Name
.O1
Initiate SS1 demand.
Make sure that the instruction output
SS1_Name
.01 turns off without generating a fault and that the drive initiates an STO
instruction.
• Verify that the STO instruction de-energizes the motor for a normal safe condition.
While the system is stopped with the sensor subsystems in a safe state, initiate a Start command.
• Verify that the STO instruction remains de-energized for a normal safe condition
• Verify proper machine status and safety application program status
While the system is stopped with the SS1 demand removed, initiate a Reset command of the STO and SS1 instructions.
• Verify that the STO instruction remains de-energized
• Verify proper machine status and safety application program status
Abnormal Operation 1
Change the actual motion deceleration rate within the motion task that is associated with this SS1 function so that it is slower
than the calculated speed limit used by the SS1 instruction.
Initiate a Start command.
• Verify that the machine is in a normal machine run condition
• Verify proper machine status and safety application program status
Operate the machine at the desired operating system speed.
Set up a trend with expected time scale and the following tags to graphically capture this information:
•
SFX_Name
.ActualSpeed
•
SS1_Name
.SpeedLimit
•
SS1_Name
.DecelerationRamp
•
SS1_Name
.O1
Initiate SS1 demand.
Make sure that the instruction generates a deceleration fault and that the drive initiates an STO instruction.
• Verify that the STO instruction de-energizes the motor for a normal safe condition
While the system is stopped with the sensor subsystems in a safe state, initiate a Start command.
• Verify that the STO instruction remains de-energized for a normal safe condition
• Verify proper machine status and safety application program status
While the system is stopped with the SS1 demand removed, initiate a Reset command of the STO and SS1 instructions.
• Verify that the STO instruction remains de-energized
• Verify proper machine status and safety application program status
Abnormal Operation 2
Change the motion deceleration rate within the motion task that is associated with this SS1 function so that the stop delay time
is exceeded without triggering a deceleration fault.
Initiate a Start command.
• Verify that the machine is in a normal machine run condition
• Verify proper machine status and safety application program status
Operate machine at desired operating system speed.
Set up a trend with expected time scale and the following tags to graphically capture this information:
•
SFX_Name
.ActualSpeed
•
SS1_Name
.SpeedLimit
•
SS1_Name
.DecelerationRamp
•
SS1_Name
.O1
Initiate SS1 demand.
Make sure that the instruction generates a maximum time fault and that the drive initiates an STO instruction.
• Verify that the STO instruction de-energizes the motor for a normal safe condition
While the system is stopped with the sensor subsystems in a safe state, initiate a Start command.
• Verify that the STO instruction remains de-energized for a normal safe condition
• Verify proper machine status and safety application program status
While the system is stopped with the SS1 demand removed, initiate a Reset command of the STO and SS1 instructions.
• Verify that the STO instruction remains de-energized
• Verify proper machine status and safety application program status