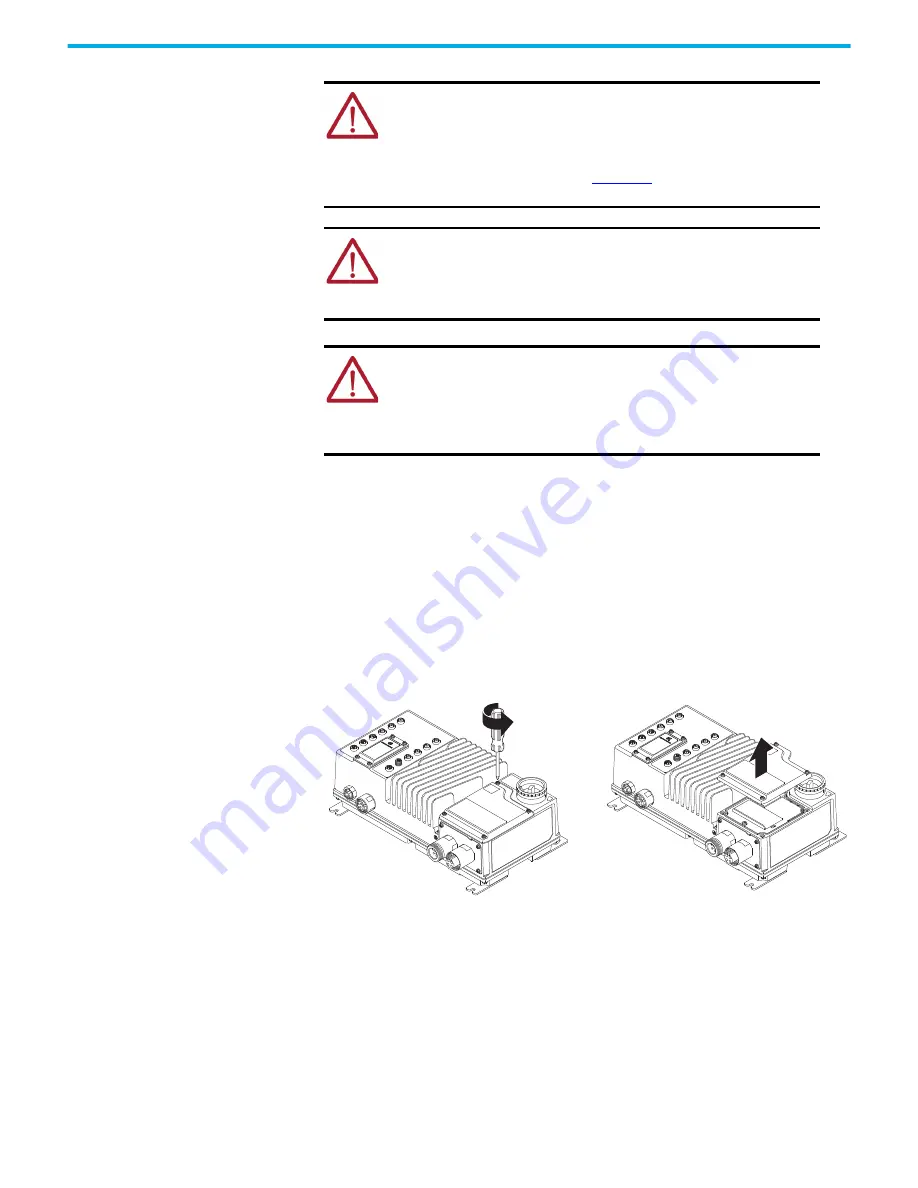
206
Rockwell Automation Publication 35-UM001A-EN-P - May 2022
Chapter 10 Maintenance and Repair
Test for Hazardous Voltage
Before servicing the Armor PowerFlex drive or any device in the motor side
(motor, motor cables, motor brake, and so on), follow these steps to remove
power from the Armor PowerFlex and test for hazardous voltage:
1. Remove power from the drive by setting the local disconnect to the Off
position or by removing the three-phase power using the isolating device
upstream (system circuit breaker, for example).
2. After power has been removed from the drive, wait three minutes so the
DC bus capacitors can discharge.
3. After 30 seconds, loosen the screws to remove the power section door.
ATTENTION:
This drive contains electrostatic discharge (ESD) –
sensitive parts and assemblies. Static control precautions are required
during installation, test, service, or repair of this assembly. Component
damage can result if ESD control procedures are not followed. If you are
not familiar with static control procedures, see Guarding against
Electrostatic Damage, publication
, or any other applicable
ESD protection handbook.
ATTENTION:
An incorrectly applied or installed drive can result in
component damage or a reduction in product life. Wiring or application
errors, such as undersized motor, incorrect or inadequate AC supply, or
excessive ambient temperatures can result in malfunction of the
system.
ATTENTION:
Five test points on Armor PowerFlex allow you to confirm
that the products downstream from the drive have been successfully
isolated from hazardous voltage and that hazardous stored energy in
the DC bus has been discharged.
This will allow safer servicing for the electromechanical brake fuses, the
motor output cable, and the motor.