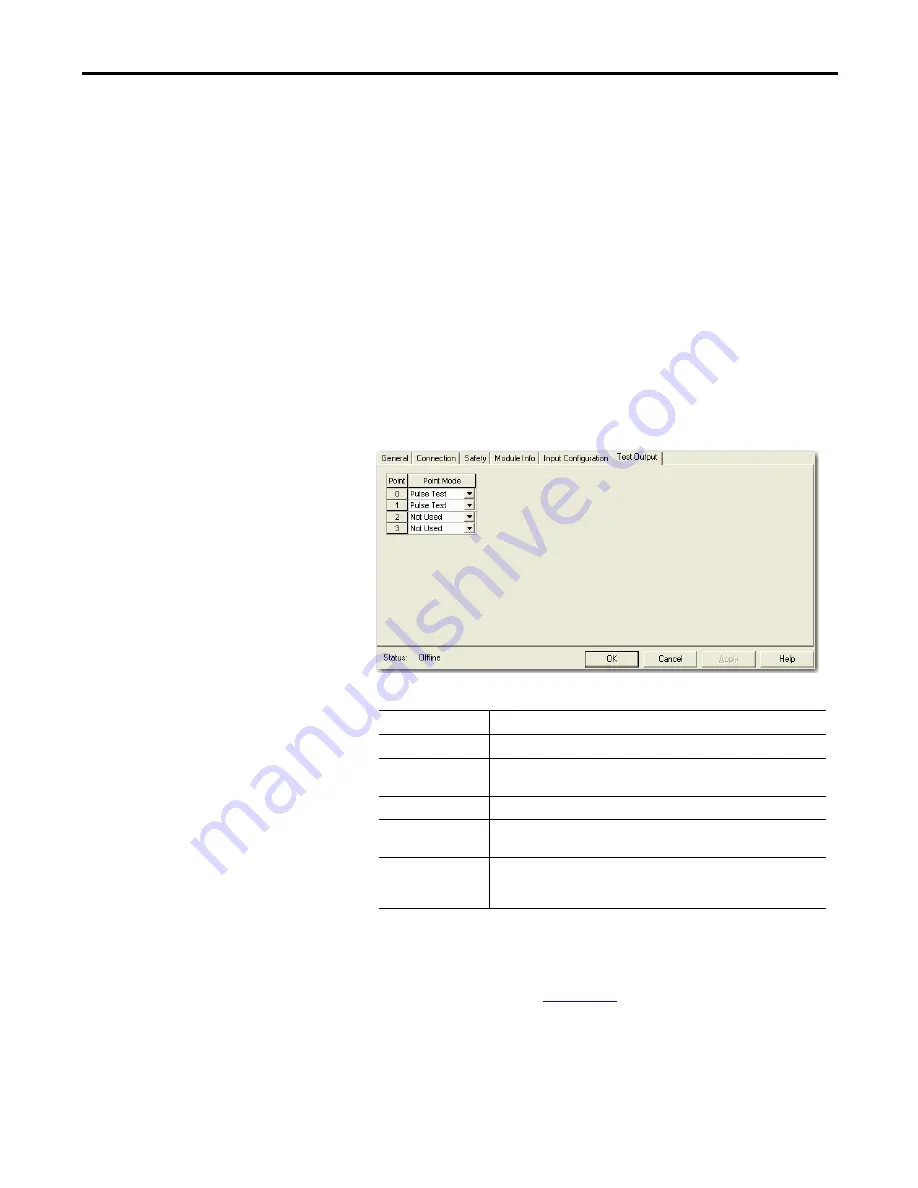
Rockwell Automation Publication 1734-UM013J-EN-P - July 2014
85
Configure the Module in a GuardLogix Controller System
Chapter 5
7.
From the Input Error Latch Time field, enter the time the module holds an
error to make sure the controller can detect it (0…65,530 ms, in increments
of 10 ms - default 1000 ms).
This setting provides more reliable diagnostics. The purpose for latching
input errors is to make sure that intermittent faults that may exist only for a
few milliseconds are latched long enough to be read by the controller. The
amount of time to latch the errors should be based on the RPI, the safety
task watchdog, and other application-specific variables.
8.
Click Apply.
Configure the Test Outputs
Follow this procedure to complete the test output configuration.
1.
From the Module Properties dialog box, click the Test Output tab.
2.
Assign the Point Mode.
There is also a Test Output Fault Action parameter that can only be read or
written to via explicit messaging. If communication to the module times
out, you can set the test outputs to Clear OFF (default) or Hold Last State.
For more information, see
.
3.
Click Apply.
Choose
Description
Not Used
The test output is disabled (default for T2 and T3).
Standard
The test output point can be controlled programmatically by the GuardLogix
controller.
Pulse Test
The test output is being used as a pulse test source (default for T0 and T1).
Power Supply
A constant 24V is placed on the output terminal. It can be used to provide
power to a field device.
Muting Lamp Output
(terminals T1 and T3
only)
An indicator lamp is connected to the output. When this lamp is energized, a
burned-out bulb, broken wire, or short to GND error condition can be detected.
Typically, the lamp is an indicator used in light curtain applications.
Summary of Contents for Allen-Bradley 1734-IB8S
Page 1: ...POINT Guard I O Safety Modules Catalog Numbers 1734 IB8S 1734 OB8S 1734 IE4S User Manual ...
Page 4: ...4 Rockwell Automation Publication 1734 UM013J EN P July 2014 Summary of Changes Notes ...
Page 10: ...10 Rockwell Automation Publication 1734 UM013J EN P July 2014 Table of Contents ...
Page 14: ...14 Rockwell Automation Publication 1734 UM013J EN P July 2014 Preface Notes ...
Page 186: ...186 Rockwell Automation Publication 1734 UM013J EN P July 2014 Appendix D Safety Data Notes ...
Page 211: ......