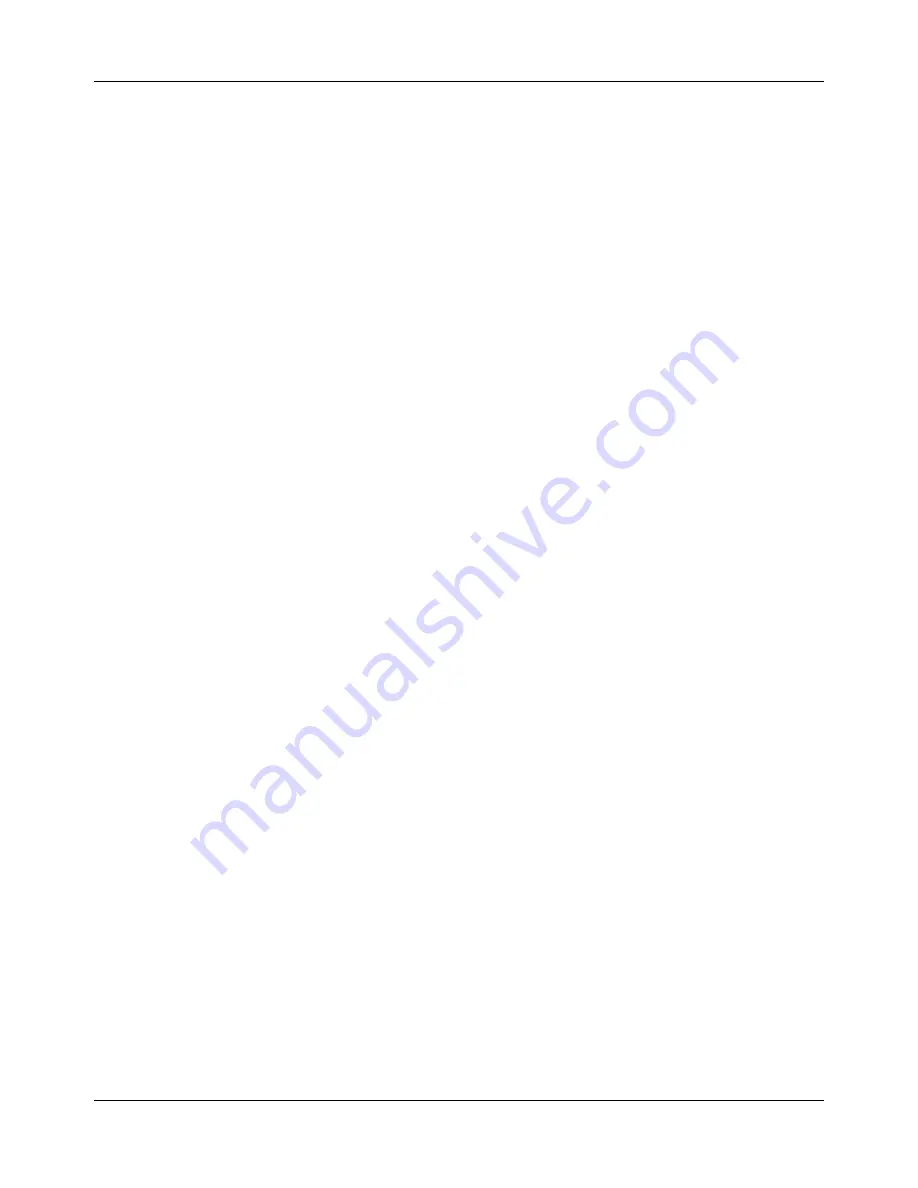
Design Guidelines
Transport System Design
QuickStick HT User Manual
75
Rockwell Automation Publication MMI-UM007F-EN-P - September 2020
The current to each motor in a system at a given time depends on system behavior and vehicle
size. When determining the size of cable, the worst case power draw, current, and vehicle
motion must always be used. When using QSMC controllers, design the electrical system to
keep voltage drops below 5% of the nominal voltage (+300–400V DC). When using QSHT
5700 inverters, design the electrical system to keep voltage drops below 5% of the nominal
voltage (+458–747V DC) is recommended.
Vehicle motion consumes power when the vehicle accelerates, and regenerates power when it
decelerates. While the vehicle is accelerating, the motor is drawing power from the motor
power supply system, including any excess power being generated from regeneration in other
motors connected to the same power supply system. In the worst case, a motor can draw up to
the value for peak power per vehicle while the vehicle is finishing its acceleration. Along with
providing the power used to accelerate a vehicle, the wiring must also be designed to manage
regenerated power as a vehicle slows and stops. In general, if a system is designed to support
supplying full power during acceleration, it also supports the excess power that regeneration
creates during deceleration.
Methods to Reduce Voltage Drop
There are two methods that can be used to reduce the drop of voltage in the system during
acceleration. The first method is to decrease the cable resistance between the power supply
and the motor drives by either shortening the length of the cables or by increasing the conduc-
tor gauge of the cables. This method reduces the voltage difference between the power supply
and the motor drive. The second method is to limit the number of motors and drives that are
connected to one power supply.
Methods to Reduce Voltage Increase
There are two methods that can be used to reduce the voltage increase in the system during
deceleration. The first method is to decrease the cable resistance between motor drives by
either shortening the length of the cables or increasing the conductor gauge of the cables. This
method reduces the voltage difference between the motor that is regenerating power and the
motors that are consuming or dissipating the power and allows the voltage at the regenerating
motor to be lower. The second method is to install a voltage clamp in the power supply circuit
to dissipate power if the voltage on the bus goes above a certain level.
Signal Wiring
Logic power of +24V DC is provided separately. Logic power is a constant 15 W of power per
motor drive (see
). Separate logic and pro-
pulsion power buses allows propulsion power to be removed (for example, during an EMO
event) without loss of motor logic functions (configuration data, vehicle data, fault informa-
tion). Separate power buses also allow the motors to be programmed and configured without
enabling the propulsion power.