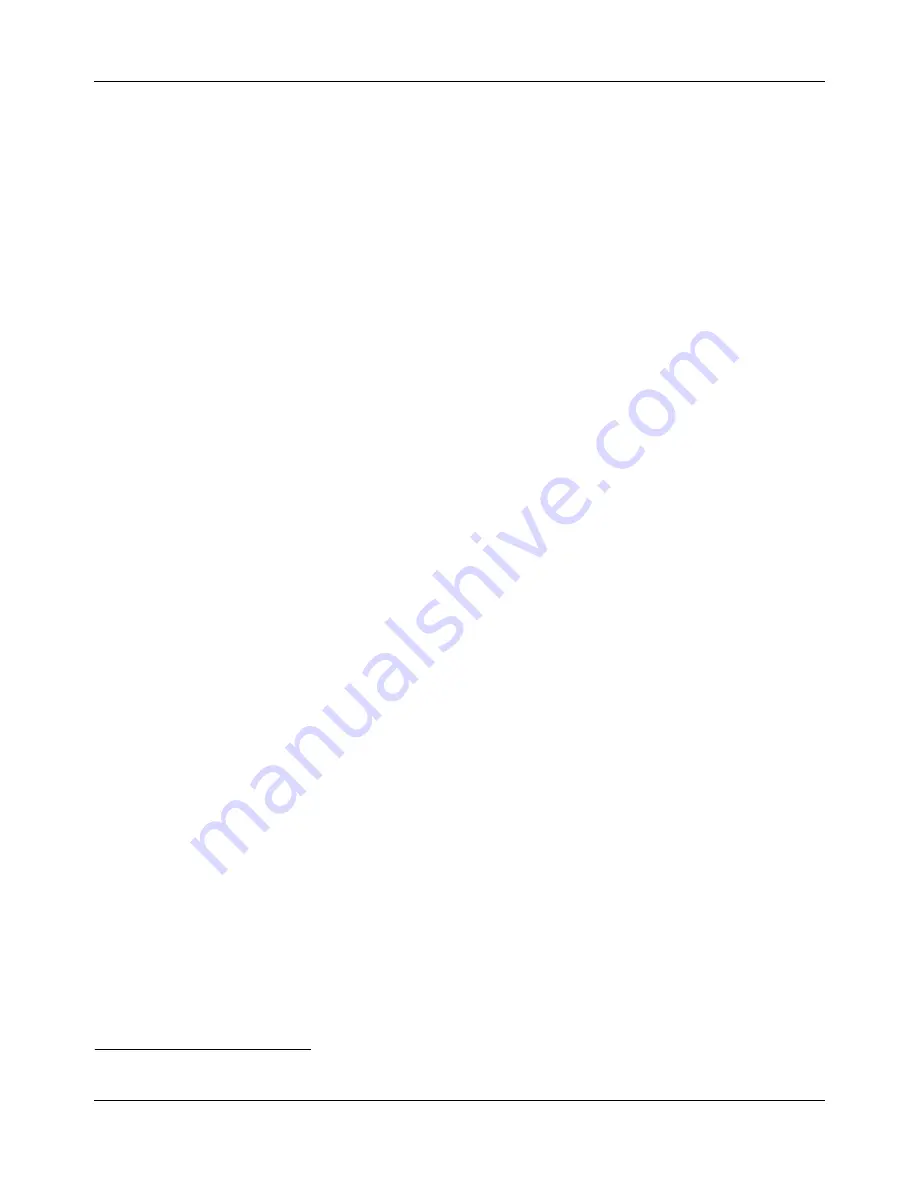
Introduction
QuickStick HT Transport System Overview
30
MagneMotion
Rockwell Automation Publication MMI-UM007F-EN-P - September 2020
QuickStick HT Transport System Overview
The QuickStick High Thrust (QSHT) is an intelligent transport system that provides fast, pre-
cise motion, and positioning and tracking of large loads being transported in a transport sys-
tem. The QSHT transport system is a configuration of linear synchronous motors and related
control electronics that move independently commanded material carriers (vehicles) in a con-
trolled manner at various acceleration/deceleration and velocity profiles while carrying a wide
range of payloads with high precision. The QSHT transport system consists of the following
components:
•
QuickStick High Thrust motors and motor drives.
•
User-designed and supplied vehicles with QSHT magnet arrays.
•
Node controllers.
•
Power supplies.
•
Paths and nodes.
•
User-supplied host controller.
•
User-designed and supplied guideway and track system.
Using proven linear synchronous motor (LSM) and control technology from MagneMotion,
QuickStick HT transport systems offer an excellent alternative to conventional belt and chain
conveyors for OEM/in-machine applications and for demanding product conveyance require-
ments.
•
QuickStick HT motors provide repeatable positioning with no hard stops required,
bidirectional travel, smooth motion, and continuous vehicle tracking and reporting.
•
Vehicle positioning and guidance are built into the motor with external drive
electronics.
•
Servo repeatability at any position: ± 1.0 mm [0.04 in] (dependent on the size
of the gap between the motor and the vehicle-mounted magnet array). Repeat-
ability can vary based on the PID settings that are used and track and vehicle
design/structure, repeatability is not applicable over the gaps between motors.
•
Vehicles are controlled individually allowing the host controller to prioritize
the routing of individual vehicles over different paths.
•
Motion is provided by user-designed vehicles with magnet arrays that are attached to
the surface closest to the motor.
•
Up to two vehicles in queue or in motion per meter
*
(238 mm [9.4 in] vehicle
length).
•
Speeds up to 3.5 m/s [7.8 mph] and acceleration up to 60 m/s
2
[6.1
g
].
*
Maximum number of vehicles per meter is determined using the shortest magnet array that is allowed on a straight
guideway. Using a longer magnet array or a curved guideway decreases the number of vehicles that fit per meter.