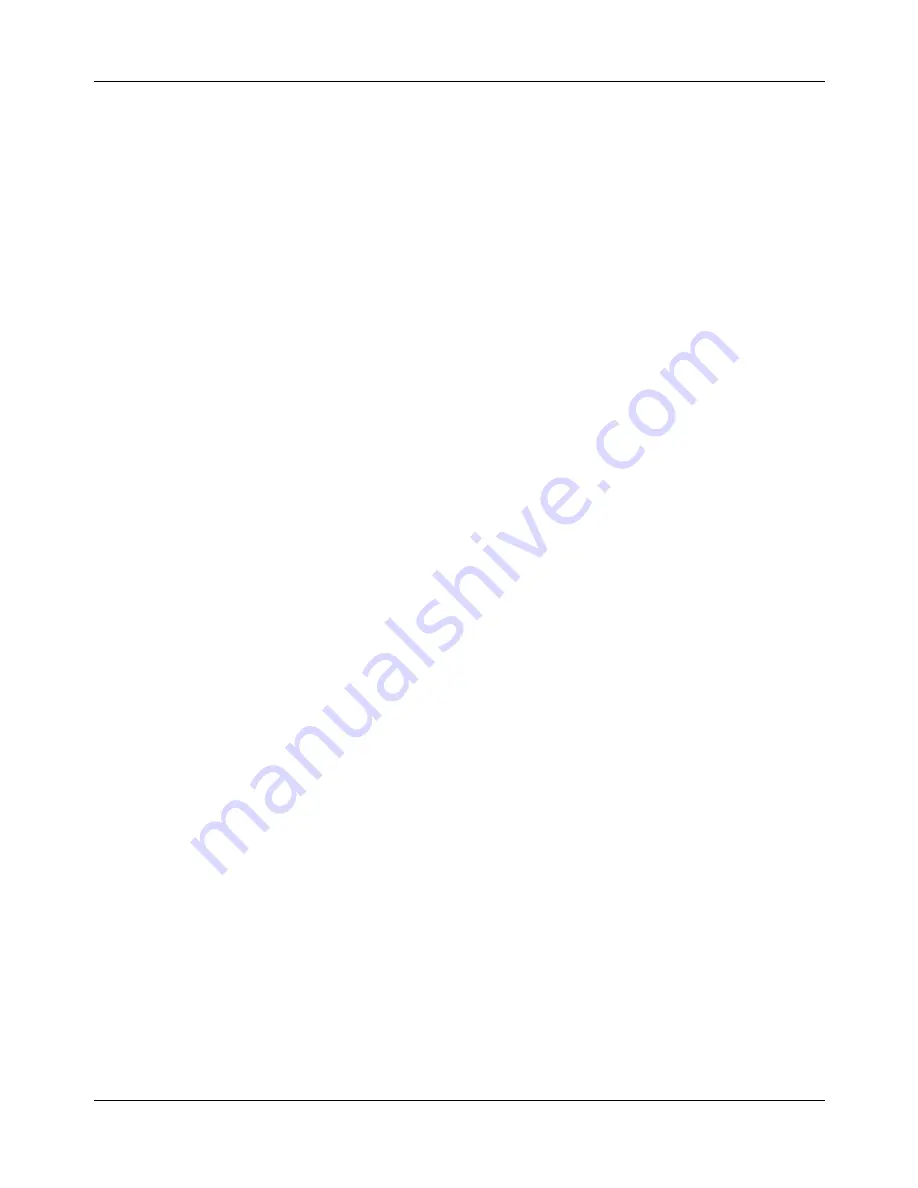
Design Guidelines
Transport System Design
110
MagneMotion
Rockwell Automation Publication MMI-UM007F-EN-P - September 2020
Vehicle Design
When designing vehicles for use with the QuickStick HT motors, the following vehicle design
guidelines and considerations must be accounted for:
•
Make the vehicles longer than the magnet array to help protect the array from impacts.
A minimum of 5 mm extra length at the front and back of the vehicle is recommended.
•
The vehicle design and the magnet array size determine the quantity and locations of
suspension and guidance wheels or other suspension and guidance features.
•
The use of a low friction barrier, such as UHMW material, is recommended to help
prevent damage to either the magnet array or the motor if there is contact between the
magnet array and the motor.
•
Up to two vehicles per meter (238 mm [9.4 in] minimum length) in motion or in
queue.
•
The payload, vehicle mass, and required acceleration must be within the limits of the
magnet array.
•
Vehicles that carry payloads sensitive to magnetic fields must provide shielding or
separate the payload from the magnet array by 50–100 mm.
•
When using curved guideways, make sure that the vehicle design is able to negotiate
the curves.
Vehicle Materials
Some examples of commonly used vehicle materials and considerations:
Steel:
•
Good strength properties.
•
High density yields heavier vehicles.
•
Caution is required when using carbon steel (a ferromagnetic material).
•
300 series stainless steel is suitable.
Aluminum:
•
Good combination of comparatively high strength and low mass.
•
Less caution is required because of no magnetic attractive force.
•
The area under the vehicle magnet array must be clear of aluminum as the aluminum
can create eddy currents, which create a breaking force.