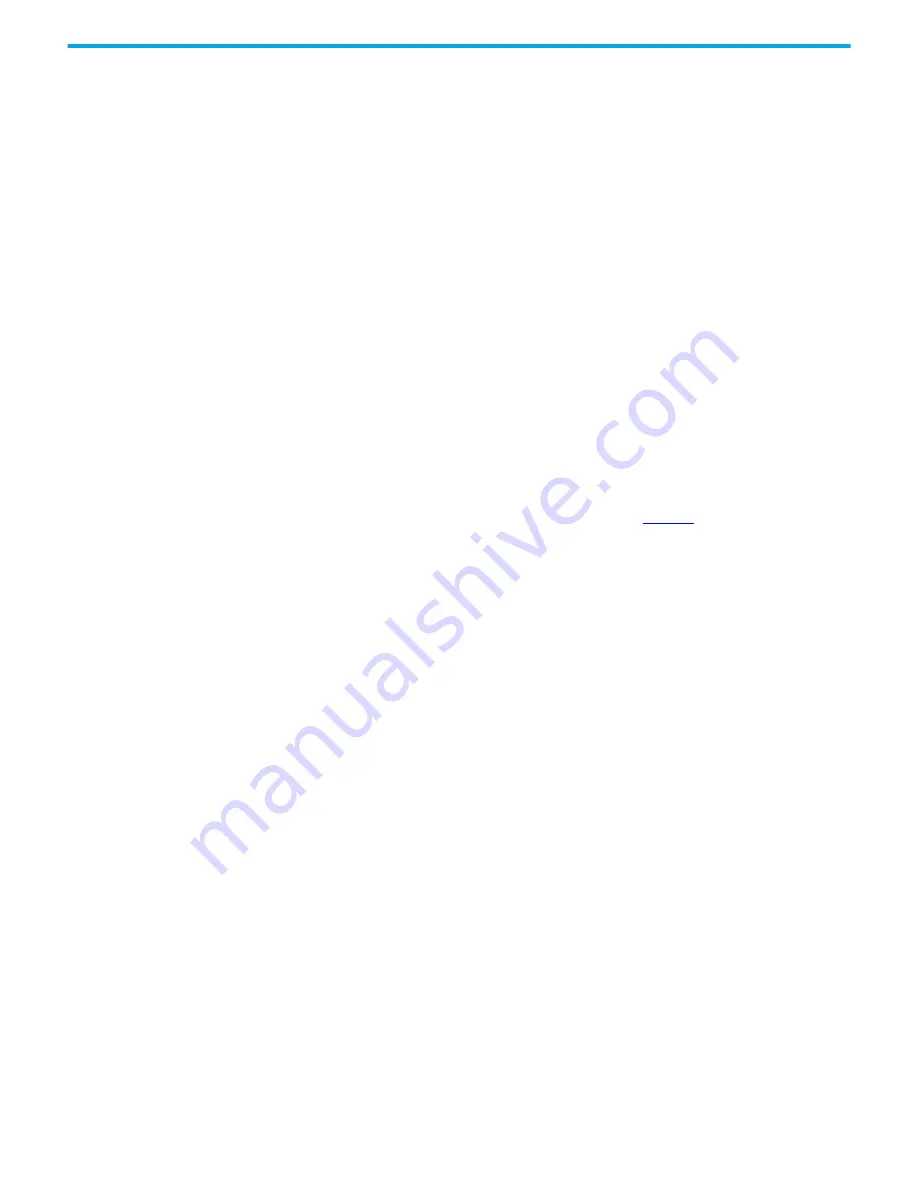
Rockwell Automation Publication 1766-UM001O-EN-P - September 2021
181
Appendix E Connect to Networks via RS-232/RS-485 Interface
power lines of less than 20 A, 0.30 m (1 ft.) from lines greater than 20 A,
but only up to 100K VA, and 0.60 m (2 ft.) from lines of 100 K VA or more.
•
If you run the cable through a contiguous metallic wireway or conduit,
keep the communication cable at least 0.08 m (3 in.) from AC power lines
of less than 20 A, 0.15 m (6 in.) from lines greater than 20 A, but only up to
100 K VA, and 0.30 m (1 ft.) from lines of 100 K VA or more.
Running the communication cable through conduit provides extra
protection from physical damage and electrical interference. If you route
the cable through conduit, follow these additional recommendations:
•
Use ferromagnetic conduit near critical sources of electrical interference.
You can use aluminum conduit in non-critical areas.
•
Use plastic connectors to couple between aluminum and ferromagnetic
conduit. Make an electrical connection around the plastic connector (use
pipe clamps and the heavy gauge wire or wire braid) to hold both sections
at the same potential.
•
Ground the entire length of conduit by attaching it to the building earth
ground.
•
Do not let the conduit touch the plug on the cable.
•
Arrange the cables loosely within the conduit. The conduit should
contain only serial communication cables.
•
Install the conduit so that it meets all applicable codes and
environmental specifications.
For more information on planning cable routes, see
Industrial Automation
Wiring and Grounding Guidelines, publication
.
Software Considerations
Software considerations include the configuration of the network and the
parameters that can be set to the specific requirements of the network. The
following are major configuration factors that have a significant effect on
network performance:
•
number of nodes on the network
•
addresses of those nodes
•
baud rate
The following sections explain network considerations and describe ways to
select parameters for optimum network performance (speed). See your
programming software’s user manual for more information.
Number of Nodes
The number of nodes on the network directly affects the data transfer time
between nodes. Unnecessary nodes (such as a second programming terminal
that is not being used) slow the data transfer rate. The maximum number of
nodes on the network is 32.
Setting Node Addresses
The best network performance occurs when node addresses are assigned in
sequential order. Initiators, such as personal computers, should be assigned
the lowest numbered addresses to minimize the time required to initialize the
network. The valid range for the MicroLogix controllers is 1...31 (controllers
cannot be node 0). The default setting is 1. The node address is stored in the
controller Communications Status file (CS0:5/0…CS0:5/7).
Summary of Contents for 1766-L32AWA
Page 10: ...10 Rockwell Automation Publication 1766 UM001O EN P September 2021 Table of Contents Notes ...
Page 302: ...302 Rockwell Automation Publication 1766 UM001O EN P September 2021 Glossary Notes ...
Page 308: ...308 Rockwell Automation Publication 1766 UM001O EN P September 2021 Index Notes ...