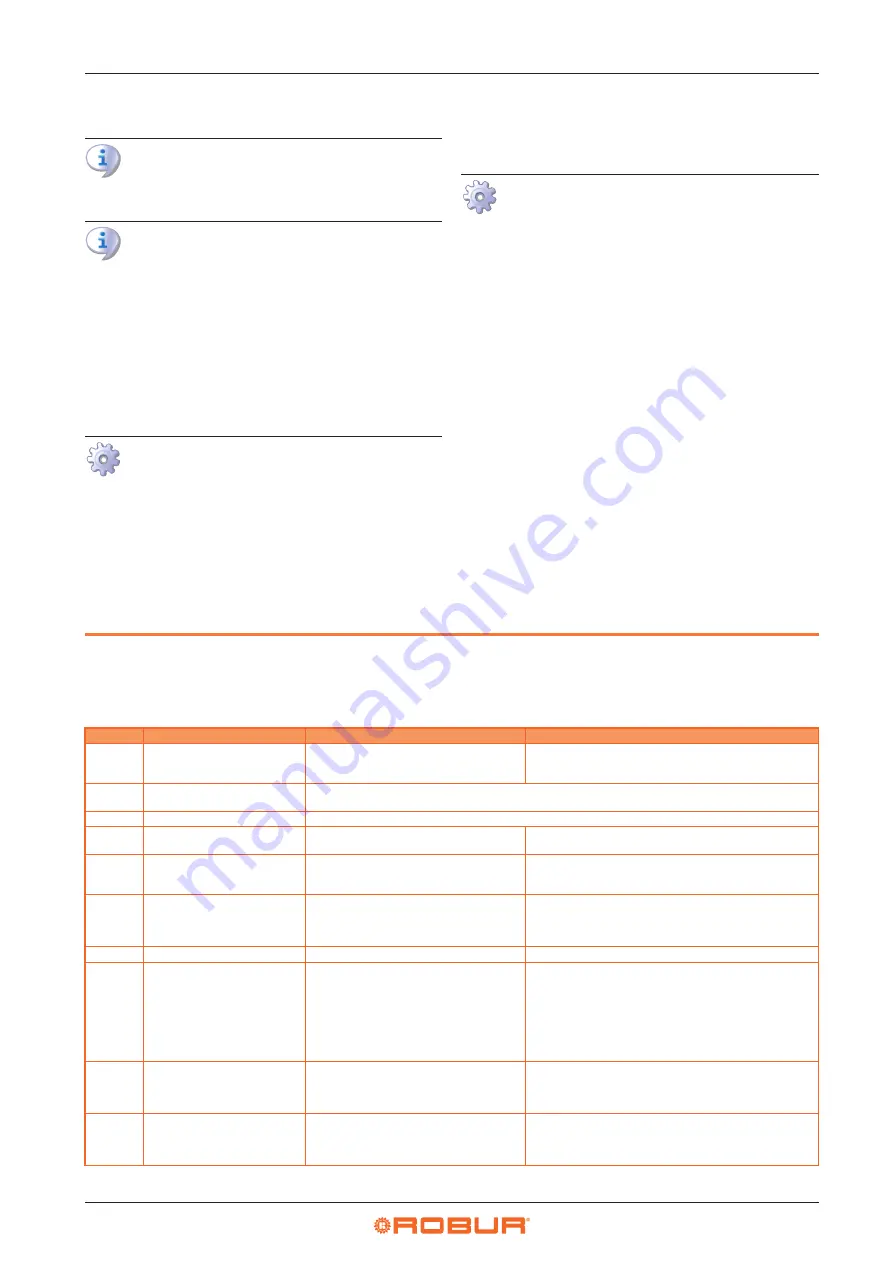
Diagnostics
34
8
7.4
PERIODS OF INACTIVITY
Avoid emptying the installation
Emptying the system may cause damage due to corro-
sion of the water pipes.
Deactivate the system in winter
Should you intend to stop the appliance in the winter
season, ensure at least one of the following conditions:
1� anti-icing function active (Paragraph 3.5 p. 21);
2� sufficient anti-icing glycol (Paragraph 3.6 p. 21).
Prolonged periods of inactivity
▶
Should you foresee to leave the appliance inactive for a long
period of time, disconnect it from the electrical and gas
mains. These operations must be performed by Qualified
Personnel.
How to deactivate the appliance for long periods of
time
1� Switch the appliance off (Paragraph 6.2 p. 30).
2� Only when the appliance is completely off, power it
off with the main switch/disconnector switch (De-
tail GS in Figure 4.2
3� Close the gas valve
4� If necessary, add water with glycol (if the appliance
is disconnected from the power and gas mains, the
active anti-icing protection is missing, Paragraph
3.5
How to reactivate the appliance after long periods of
inactivity
Before reactivating the appliance, the operator/mainte-
nance technician of the system must first of all:
Check whether any maintenance operations are re-
quired (contact the TAC; see Paragraphs 7.2
and 7.3
Check content and quality of the water in the system,
and if necessary top it up (Paragraphs 3.8
Ensure the flue gas exhaust duct is not obstructed,
and that the condensate drain is clean.
After completing the above checks:
1� Open the gas cock and ensure there are no leaks;
should gas smell be noticed, close the gas cock
again, do not switch any electrical devices on and
request intervention by Skilled Personnel.
2� Power on with the main power supply switch (GS,
Figure 4.2
3� Switch on the appliance by means of the provided
control device (DDC, CCP/CCI or external request,
Paragraph 4.4
p. 26).
8
DIAGNOSTICS
8.1
OPERATIVE CODES
Table 8�1
Operative Codes GAHP A
CODES
DESCRIPTION
Warning (u)
Error (E)
400
FAULT ON RESET CIRCUIT OF
FLAME CONTROL UNIT
NA
Power cycle the appliance.
If the code persists, shows up again or in case of doubt, contact
the TAC.
401
GENERATOR LIMIT THERMOSTAT
TRIP
Contact authorised Technical Assistance
402
FLUE GAS THERMOSTAT TRIP
Contact authorised Technical Assistance
405
AMBIENT TEMPERATURE EXCEED-
ING OPERATIVE LIMITS
NA
Reset is automatic when the triggering condition ceases.
406
AMBIENT TEMPERATURE LOWER
THAN OPERATIVE LIMITS
Non-blocking Warning (informative code).
The code is reset automatically when the
triggering condition ceases.
NA
407
GENERATOR TEMPERATURE HIGH
Reset is automatic when the triggering condi-
tion ceases.
Reset may be performed from the DDC/CCI or from the S61
board (menu 2, parameter 21).
If the code persists, shows up again or in case of doubt, contact
the TAC.
408
FLAME CONTROL UNIT ERROR
NA
Contact authorised Technical Assistance
410
INSUFFICIENT WATER FLOW
Reset is automatic when the triggering condi-
tion ceases.
Check and clean water filters on the system.
Check for air in the system.
Check water flow pump.
Power cycle the appliance.
Reset may be performed from the DDC/CCI or from the S61
board (menu 2, parameter 21).
If the code persists, shows up again or in case of doubt, contact
the TAC.
411
INSUFFICIENT ROTATION OF OIL
PUMP
Reset occurs automatically 20 minutes after the
code is generated.
Reset may be performed from the DDC/CCI or from the S61
board (menu 2, parameter 21).
If the code persists, shows up again or in case of doubt, contact
the TAC.
412
FLAME CONTROLLER UNIT ARREST Reset is automatic up to 4 attempts (in about 5
minutes).
Gas supply check.
Reset may be performed from the DDC/CCI or from the S61
board (menu 2, parameter 20).
If the code persists or in case of doubt, contact the TAC.