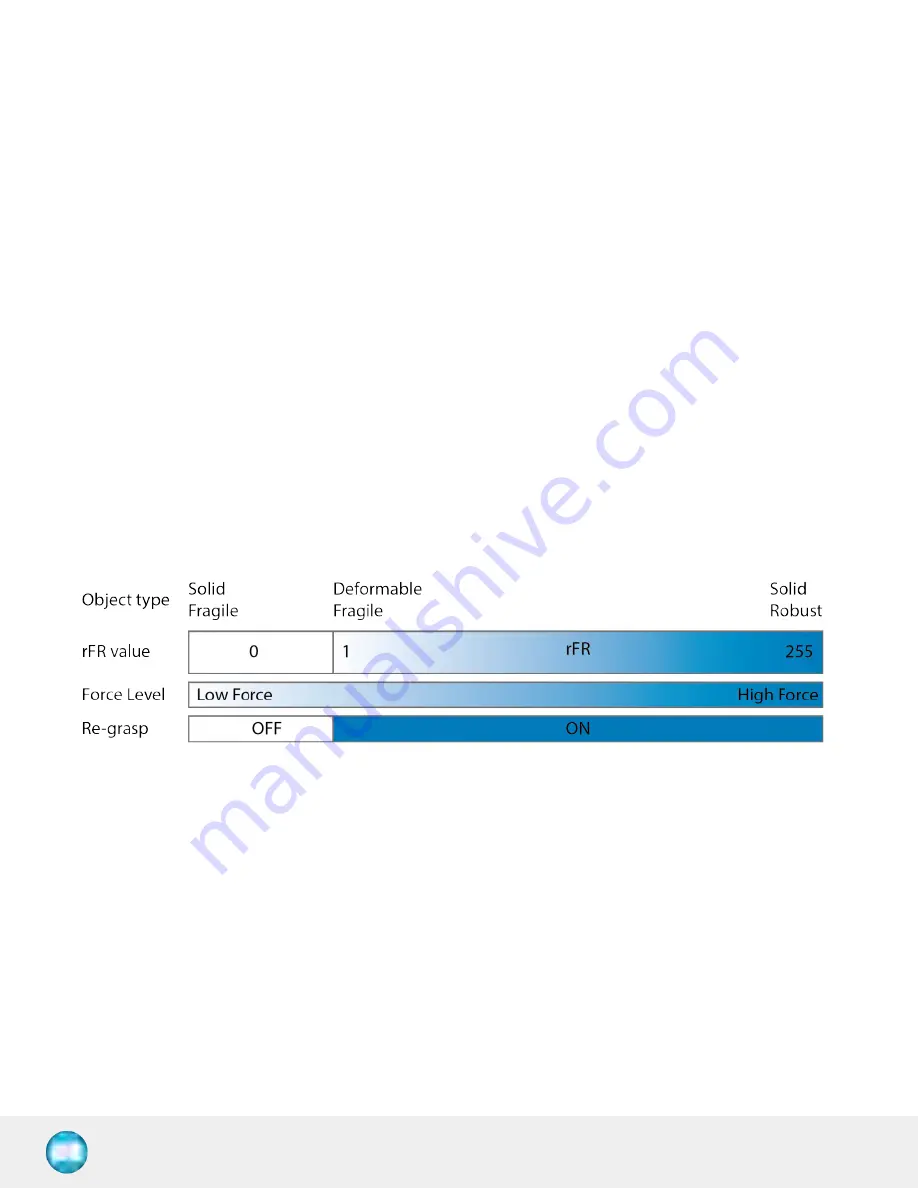
2F-85 & 2F-140 - Instruction Manual
4.5. Picking Features
As stated in previous sections, object picking is done via a simple "Go To" command, rGTO bit calls for movement, while rPR byte
is the aimed position, rSP and rFR will be the desired speed and force settings respectively. This section describes key features in
object picking applications:
l
Force control
l
Re-grasp
l
Object detection
l
Object contact loss
4.5.1. Force Control
The gripping force is controlled via the rFR byte (refer to the Robot Output Registers & Functionalities section).The gripper
behavior will change according to the rFR force requested.
l
rFR = 0 : Very fragile objects
l
Lowest force
l
Re-grasp feature is off
l
1 rFR 255 : Fragile to robust object
l
Re-grasp feature is on
The table below shows the expected applied force according to the payload material hardness, speed setting rSP and force
setting rFR. All tests were done with the 2-Finger Gripper with firmware GC3-1.3.9. Data was obtained with a Load Cell from
Phidget
,
S Type
,
model 3138
.
40