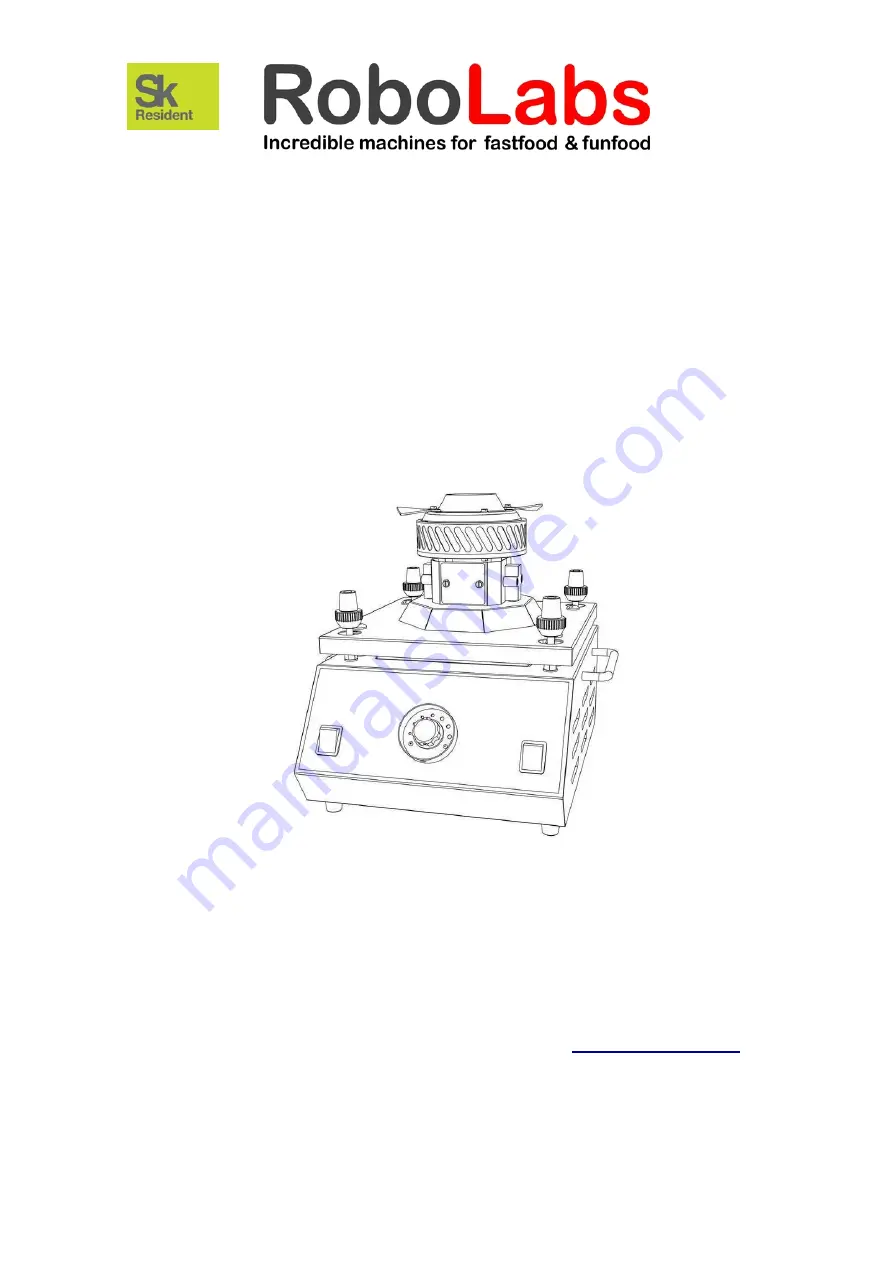
OPERATING MANUAL
COTTON CANDY MACHINES
TWISTER-M2 (ACB-02E) 230 V
TWISTER-M2 (ACB-02U) 120 V
MONSTER (ACB-07) 230 V
CAUTION: READ THE INSTRUCTIONS
BEFORE USING THE MACHINE!
PDF version of this manual is available on
OPERATING MANUAL
COTTON CANDY MACHINES
TWISTER-M2 (ACB-02E) 230 V
TWISTER-M2 (ACB-02U) 120 V
MONSTER (ACB-07) 230 V
CAUTION: READ THE INSTRUCTIONS
BEFORE USING THE MACHINE!
PDF version of this manual is available on