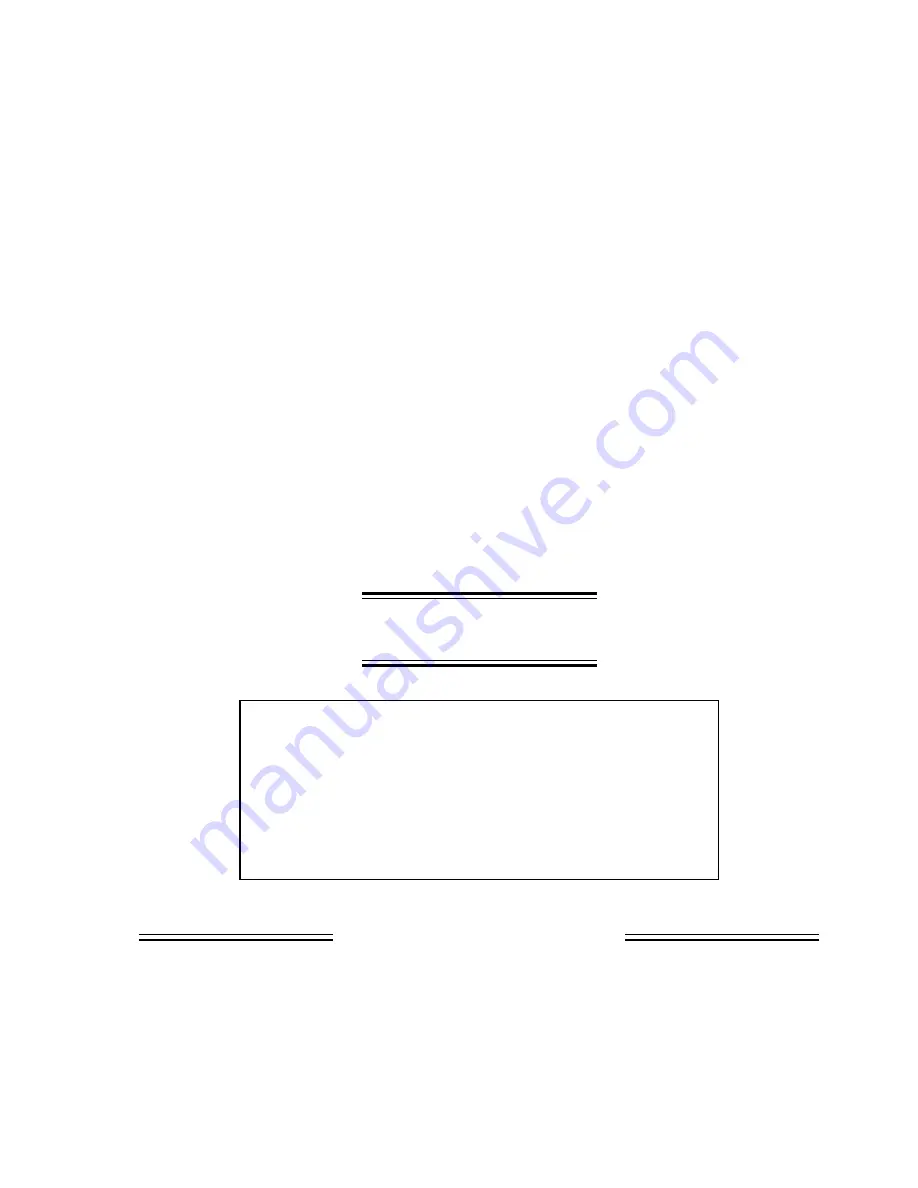
RISO INTERNATIONAL GROUP
RISO KAGAKU CORPORATION (JAPAN)
RISO DEUTSCHLAND GMBH (GERMANY)
RISO, INC. (U.S.A.)
RISO FRANCE (FRANCE)
RISO EUROPE LIMITED (U.K.)
RISO IBERICA (SPAIN)
RISO HONG KONG (HONG KONG)
RISO CANADA (CANADA)
RISO UK (U.K.)
RISO ZHUHAI (HONG KONG)
RISO THAILAND LIMITED (THAILAND)
RISO AFRICA (SOUTH AFRICA)
Copyright : 2000 Riso Kagaku Corporation
All Rights Reserved. This Technical Manual was prepared
and written for the exclusive use of RISO International Group
Certified Dealers. Reproduction and/or transmittal of this
material in any form or by any means, including photocopying
or recording of the information is strictly prohibited without the
consent of a member of RISO International Group.
VERSION 1.0
JULY, 2000
RN
SERIES
TECHNICAL MANUAL
Summary of Contents for RN SERIES
Page 18: ...1 16 RN Version 1 0 CHAPTER 1 MAINTENANCE Memo...
Page 21: ...2 3 RN Version 1 0 CHAPTER 2 MACHINE SUMMARY SPECIFICATIONS METRIC MODEL Reference only...
Page 22: ...2 4 RN Version 1 0 CHAPTER 2 MACHINE SUMMARY SPECIFICATIONS METRIC MODEL Reference only...
Page 23: ...2 5 RN Version 1 0 CHAPTER 2 MACHINE SUMMARY SPECIFICATIONS METRIC MODEL Reference only...
Page 25: ...2 7 RN Version 1 0 CHAPTER 2 MACHINE SUMMARY SPECIFICATIONS INCH MODEL Reference only...
Page 30: ...3 5 RN Version 1 0 CHAPTER 3 MAIN DRIVE SECTION Memo...
Page 43: ...4 8 RN Version 1 0 CHAPTER 4 FIRST PAPER FEED SECTION Memo...
Page 82: ...6 9 RN Version 1 0 CHAPTER 6 PRESS SECTION Memo...
Page 85: ...6 12 RN Version 1 0 CHAPTER 6 PRESS SECTION Memo...
Page 131: ...8 30 RN Version 1 0 CHAPTER 8 PRINT DRUM SECTION Memo...
Page 156: ...11 3 RN Version 1 0 CHAPTER 11 FB ORIGINAL SCANNING SCTION SCANNER TABLE SETTING SYSTEM Memo...
Page 182: ...12 5 RN Version 1 0 CHAPTER 12 ADF SCANNING SECTION ADF ORIGINAL SET MECHANISM Memo...
Page 286: ...17 1 RN Version 1 0 CHAPTER 17 USERS MODE Contents 1 Customizing the Initial Setting 1 2...
Page 288: ...17 3 RN Version 1 0 CHAPTER 17 USERS MODE CUSTOMIZING THE INITIAL SETTINGS...
Page 289: ...17 4 RN Version 1 0 CHAPTER 17 USERS MODE CUSTOMIZING THE INITIAL SETTINGS...
Page 290: ...17 5 RN Version 1 0 CHAPTER 17 USERS MODE CUSTOMIZING THE INITIAL SETTINGS...
Page 294: ...18 4 RN Version 1 0 CHAPTER 18 MISCELLANEOUS PRECAUTIONS Memo...