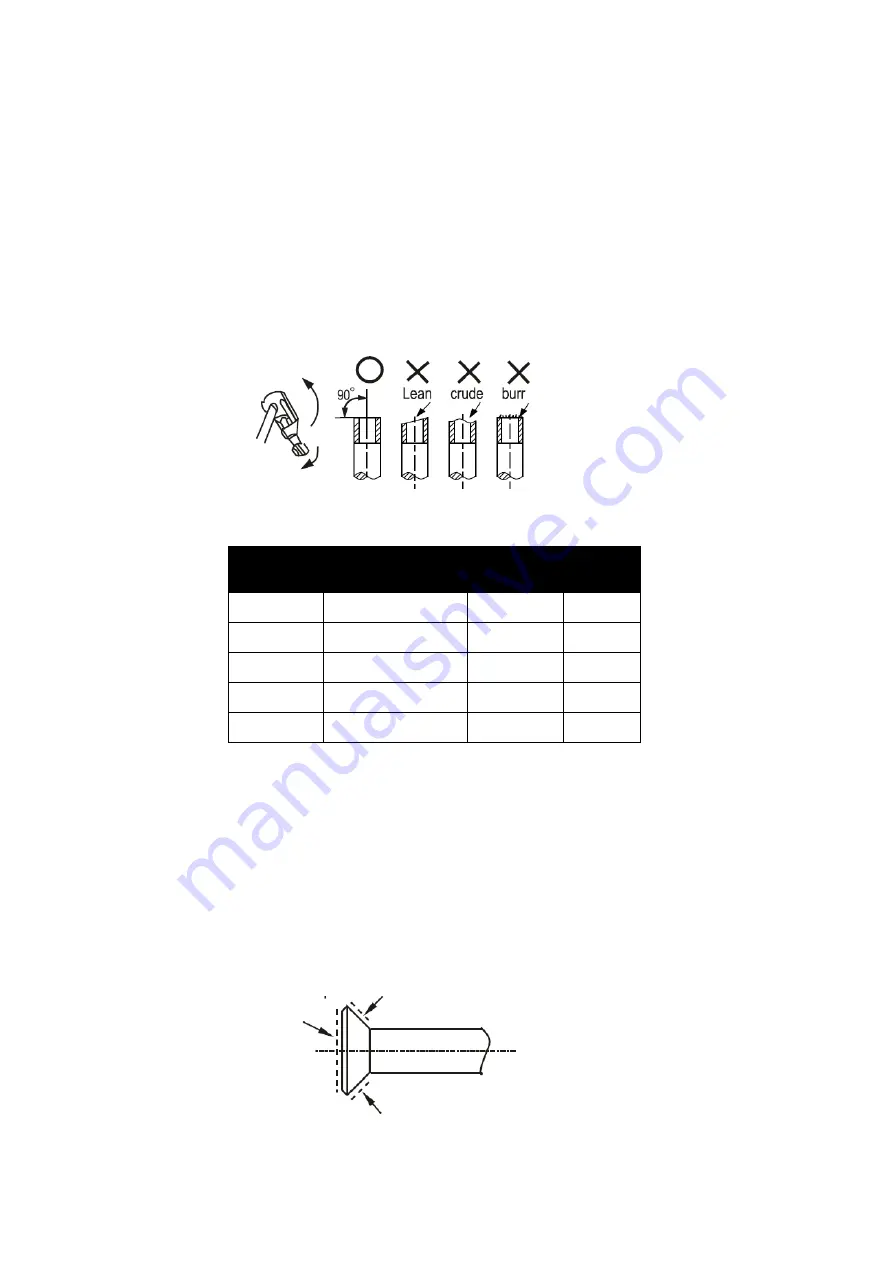
20
6.2 Pipe-work connection
Sweat connection:
•
Locate the suction & liquid pipe service valves in the compressor compartment by removing the service access
panel
•
Check that the service valves are tightly closed (Service Ball valves have been provided for suction and liquid
lines)
•
Wrap each valve in turn with a wet cloth prior to sweating off its associated blanking plate (Flare nut connection is
fitted on some of the indoor units to avoid brazing)
•
Braze the interconnecting liquid and suction pipes from the indoor unit
•
Pressurise the indoor unit & pipe-work again with dry nitrogen and check for any brazed joint leaks. Repair as
necessary but ensure the system is not under pressure prior to brazing
•
With the indoor unit pressure again released, evacuate to a vacuum pressure of 100 microns minimum
•
Disconnect the vacuum pump whilst retaining the system vacuum
•
Open the liquid line valve fully first, and then the suction line valve
Flare connection:
•
Cut the pipe with pipe cutter
•
Insert the flare nut into the pipe and flare the end
•
Refer to the following table for the dimension of flare nut spaces:
Pipe Gauge
Tightening Torque
Flare Dimensions ‘A’
Minimum
(mm)
Maximum
(mm)
Ø 6.4
14.2 ~ 17.2 N.m
(144 ~ 176 kgf.cm)
8.3
8.7
Ø 9.5
32.7 ~ 39.9 N.cm
(333 ~ 407 kgf.cm)
12.0
12.4
Ø 12.7
49.5 ~ 60.3 N.m
(504 ~ 616 kgf.cm)
15.4
15.8
Ø 15.9
61.8 ~ 75.4 N.m
(630 ~ 770 kgf.cm)
18.6
19.0
Ø 19.0
97.2 ~ 118.6 N.m
(990 ~ 1210 kgf.cm)
22.9
23.3
Table 3 – Flare Dimensions and Flare Tightening Torque
•
Connect the indoor unit first and then the outdoor unit.
•
Bend the refrigerant pipe in the correct way to prevent damage.
•
The bending angle should not exceed 90°.
•
The preference is to place any bends in the middle of the pipe. The larger the bending radius the
better, as it reduces internal pressure drop.
•
Do not bend pipe more than is necessary.
•
When connecting the flare nut, coat the flare both inside and outside with approved oil and
initially tighten by hand 3 or 4 turns before tightening firmly
.