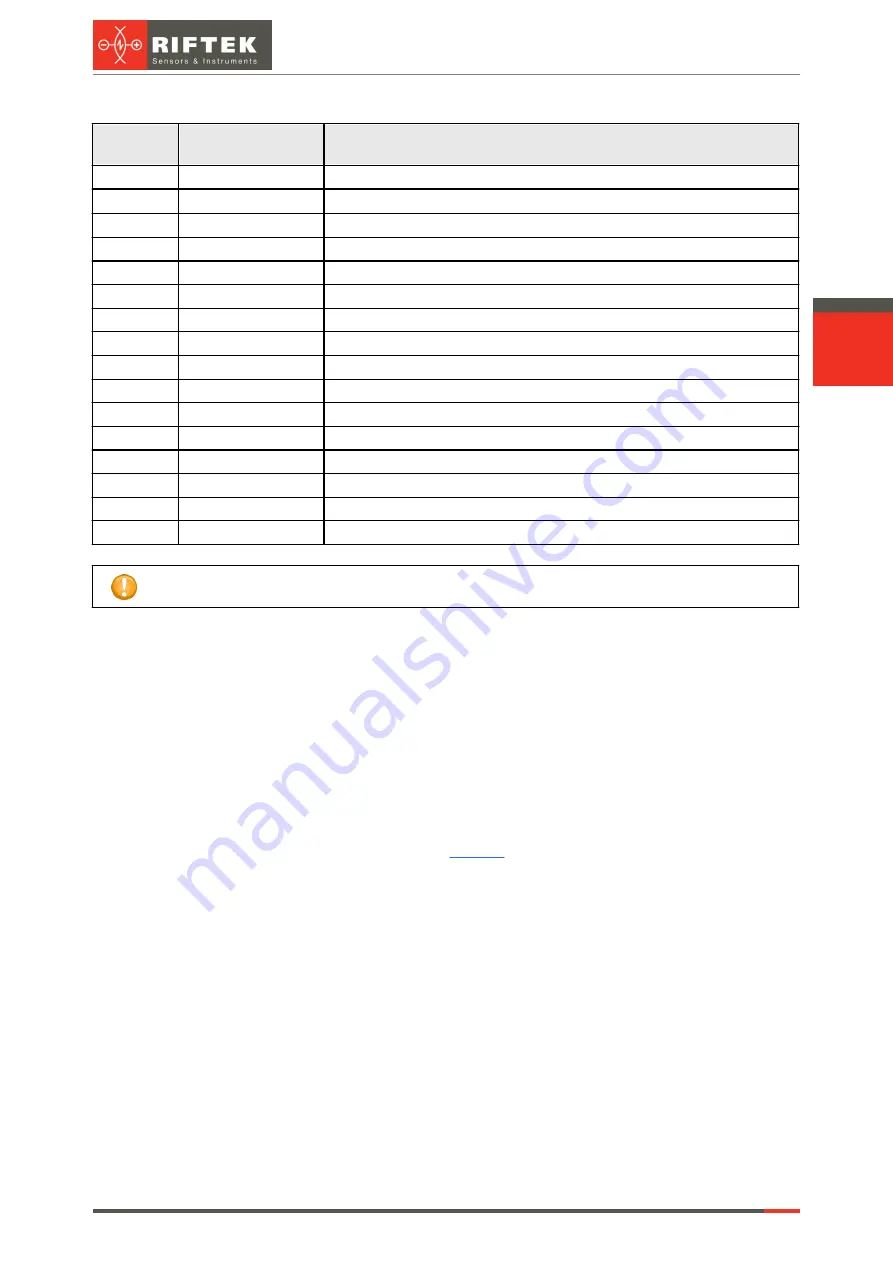
8
Laser Seam Tracking System for Welding Automation. RF627Weld Series
RF627Weld [Revision 1.1.1] 03.08.2020
Assignment of cable wires is given in the table below:
Pin
number
Wire color
Assignment
K
Pink
MX4-
L
Gray
MX4+
M
Red
Power 9...36V
N
Blue
0V GND
A
Black
MX3-
B
Violet
MX3+
C
Brown / Yellow
IN1-
D
White / Yellow
IN1+
E
Red / Blue
IN3+
F
White
MX2-
O
Brown
MX2+
G
Gray / Pink
IN3-
P
Yellow
MX1-
H
White / Green
IN2+
I
Brown / Green
IN2-
R
Green
MX1+
If the order does not include a controller, the UNITRONIC® LiYCY (TP) cable will be compressed
to RJ-45 Ethernet and two power wires (red and brown).
5.4.2. RJ-45 Ethernet cable
The RJ-45 Ethernet cable is used to connect the scanner controller to the robot
controller.
5.4.3. Power cable
The power cable is used to connect the scanner controller to 220V AC.
5.5. Calibration plate
The calibration plate is used to calibrate the scanner relative to the welding robot.
The calibration procedure is described in par.
6. Operating principle
The laser scanner is mounted on the flange of the robot next to the welding torch.
The scanning area is located directly in front of the welding electrode at a distance of
several centimeters. The scanner controller processes the information received from the
scanner in accordance with the selected mathematical algorithm that determines the exact
coordinates of the welding joint. In real time, the scanner controller transmits the coordinates
to the robot controller, and the robot controller corrects the position of the welding torch
during the welding process.