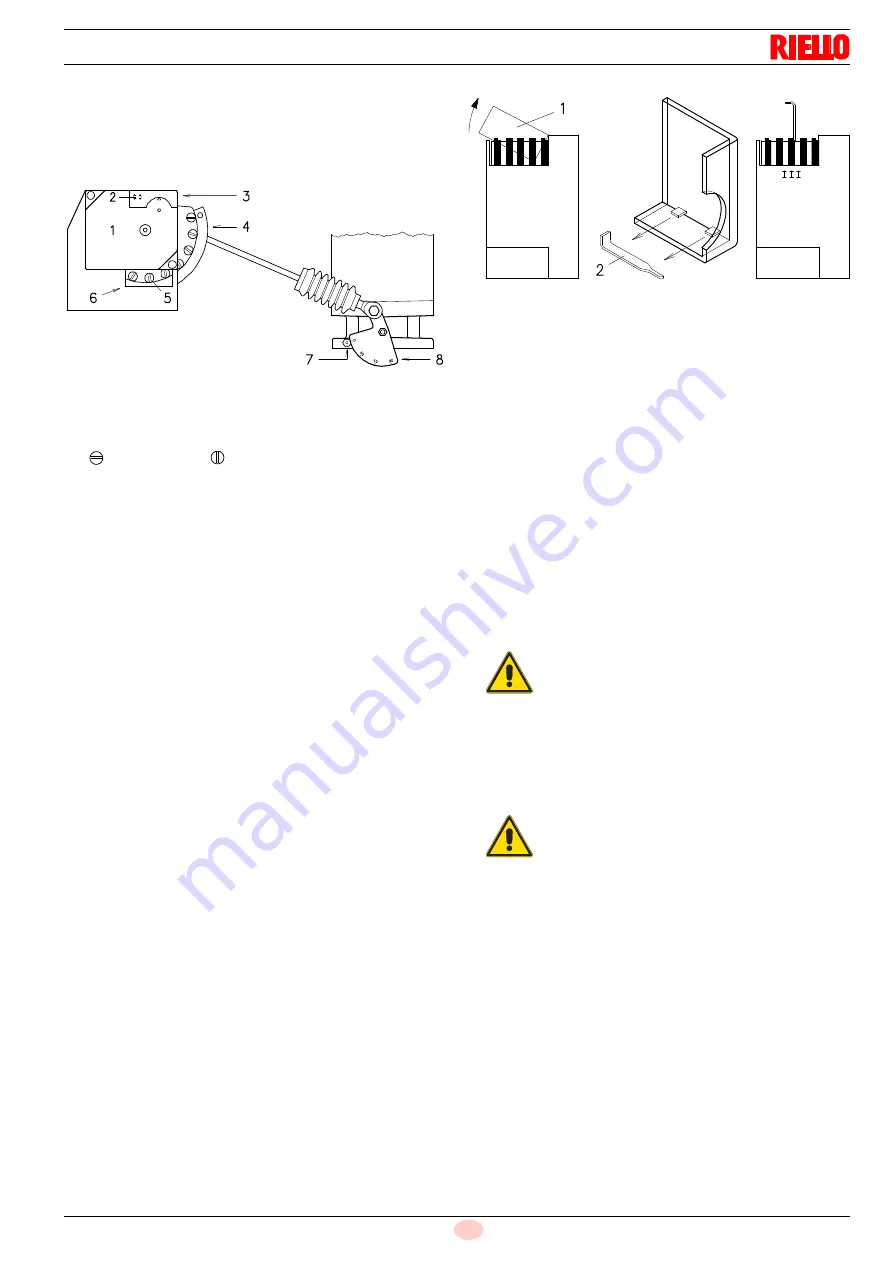
23
20159575
GB
Start-up, calibration and operation of the burner
Air adjustment
Progressively adjust the end profile of cam 4)(Fig. 28) by turning
the screws of the cam that appear inside the opening 6)(Fig. 28).
–
Turn the screws clockwise to increase air delivery
–
Turn the screws anticlockwise to reduce air delivery
Servomotor
2
Cam 4 engaged/
disengaged
3
Cam cover
4
Variable profile cam
5
Screws for adjusting the adjustable profile
6
Opening for access to screws 5
7
Index for graduated sector 8
8
Graduated sector for gas butterfly valve
6.6.3
Minimum output
The MIN output must be set within the firing rate (Fig. 2 on
page 9).
Press the “reduce output” button 2)(Fig. 27 on page 22) and keep
it pressed until the servomotor has closed the air damper and the
gas butterfly valve is at 20° (adjustment made in the factory).
Adjustment of gas delivery
Measure the gas delivery on the gas meter.
–
If it is necessary to reduce it, slightly decrease the angle of
cam III (Fig. 29) with small, regular movements, i.e. bring it
from an angle of 20° to 18° - 16°....
–
If you need to increase it, lightly press the “increase output”
button 2)(Fig. 27 on page 22) (open the gas butterfly valve by
10-15°), and increase angle of cam III (Fig. 29) with a series
of small movements, i.e. move from angle 20° to 22° - 24°....
–
Now press the “power reduction” button until the servomotor
returns to the minimum opening position, and measure the
gas delivery.
NOTE:
The servomotor follows the adjustment of cam III only when the
angle of the cam is reduced.
If it is necessary to increase the angle of the cam, you must first
increase the angle of the servomotor by means of the “output in-
crease” key, then increase the angle of cam III, and finally bring
the servomotor to the position of MIN output, with the “output re-
duction” key.
To adjust cam III, remove the snap action cover 1)(Fig. 29), re-
move the relative key 2) from inside and insert it into the notch of
cam III.
Air adjustment
Progressively adjust the beginning profile of cam 4)(Fig. 28) by
turning the screws of the cam that appear inside the opening
6)(Fig. 28).
It is preferable not to turn the first screw since this is used to set
the air damper to its fully closed position.
6.6.4
Intermediate outputs
Adjustment of gas delivery
No adjustment of gas delivery is required.
Air adjustment
Lightly press the “increase output” button 2)(Fig. 27 on page 22)
so that a new screw 5)(Fig. 28) appears inside the opening
6)(Fig. 28), adjust it until optimal combustion is obtained.
Proceed in the same way with the other screws.
Switch off the burner using the switch 1)(Fig. 27 on page 22), po-
sition OFF, release the variable profile cam from the servomotor
putting the notch 2)(Fig. 28) in the vertical position.
Check that the movement is fluid and free of jamming by turning
the cam backwards and forwards by hand a few times.
NOTE:
Once you have finished adjusting outputs MAX - MIN - INTER-
MEDIATE, check ignition once again: noise emission at this
stage must be identical to the following stage of operation. If you
notice any sign of pulsations, reduce the ignition stage delivery.
Fig. 28
D518
ATTENTION
Take care that the cam profile variation is progres-
sive.
ATTENTION
As far as is possible, try not to move those screws
at the ends of the cam that were previously adjust-
ed for the opening of the air damper to MAX and
MIN output.
Fig. 29
D793