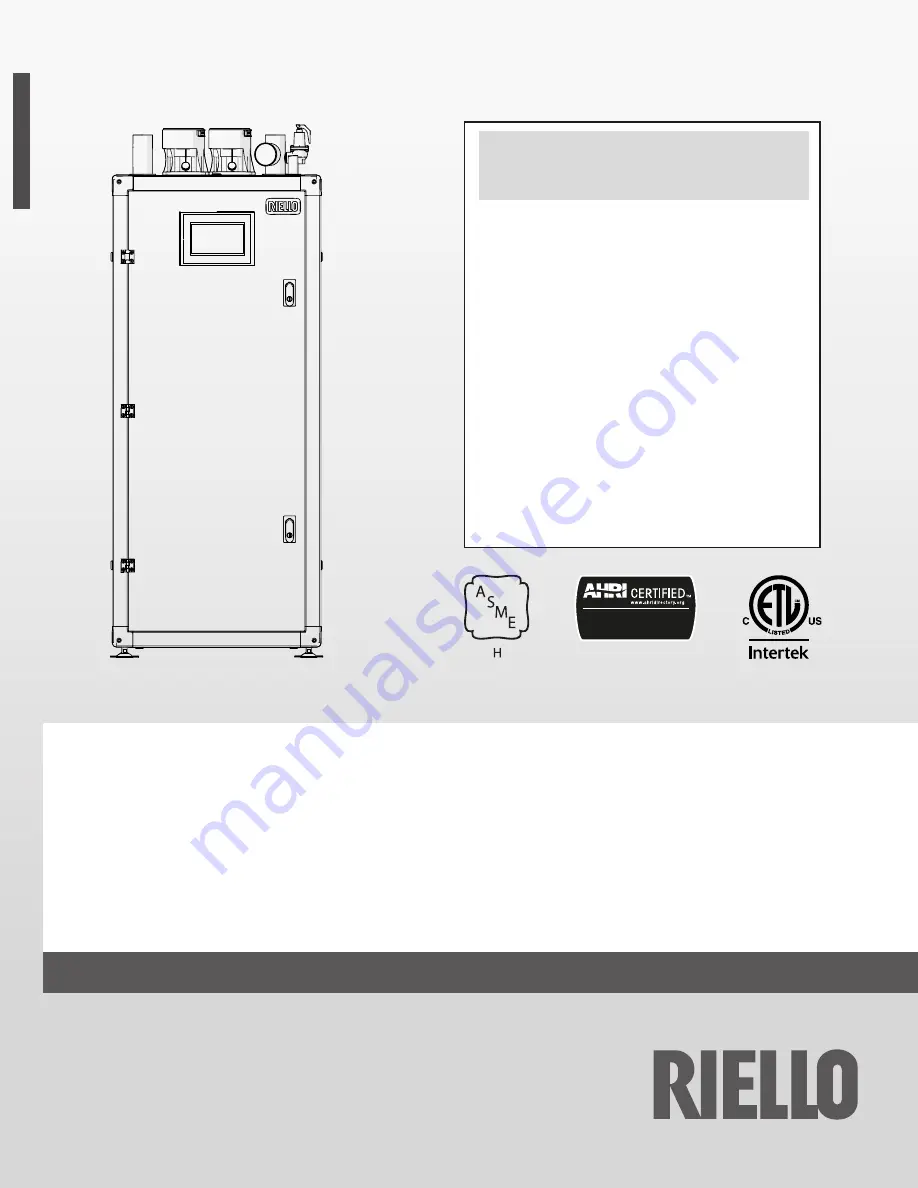
co
d
. 2
0
18
32
4
8 r
e
v.
2
0
4/
202
1
9
WARNING
: If the information in this manual is not
followed exactly, a fire or explosion may result causing
property damage, personal injury or loss of life.
Do not store or use gasoline or other flammable
vapors and liquids or other combustible materials in
the vicinity of this or any other appliance. To do so
may result in an explosion or fire.
What to do if you smell gas:
- Do not try to light any appliance;
- Do not touch any electrical switch; do not use any
phone in your building;
- Immediately call your gas supplier from a neighbor’s
phone. Follow the gas supplier’s instructions;
- If you cannot reach your gas supplier, call the fire
department.
Installation and service must be performed by a
qualified installer, service agency or the gas supplier.
This manual should be maintained in legible
condition and kept adjacent to the boiler or in a safe
place for future reference.
Commercial Boilers
AHRI Standard BTS-2000
Array AR 399 SE - 500 SE
INSTALLATION, OPERATION AND SERVICE MANUAL