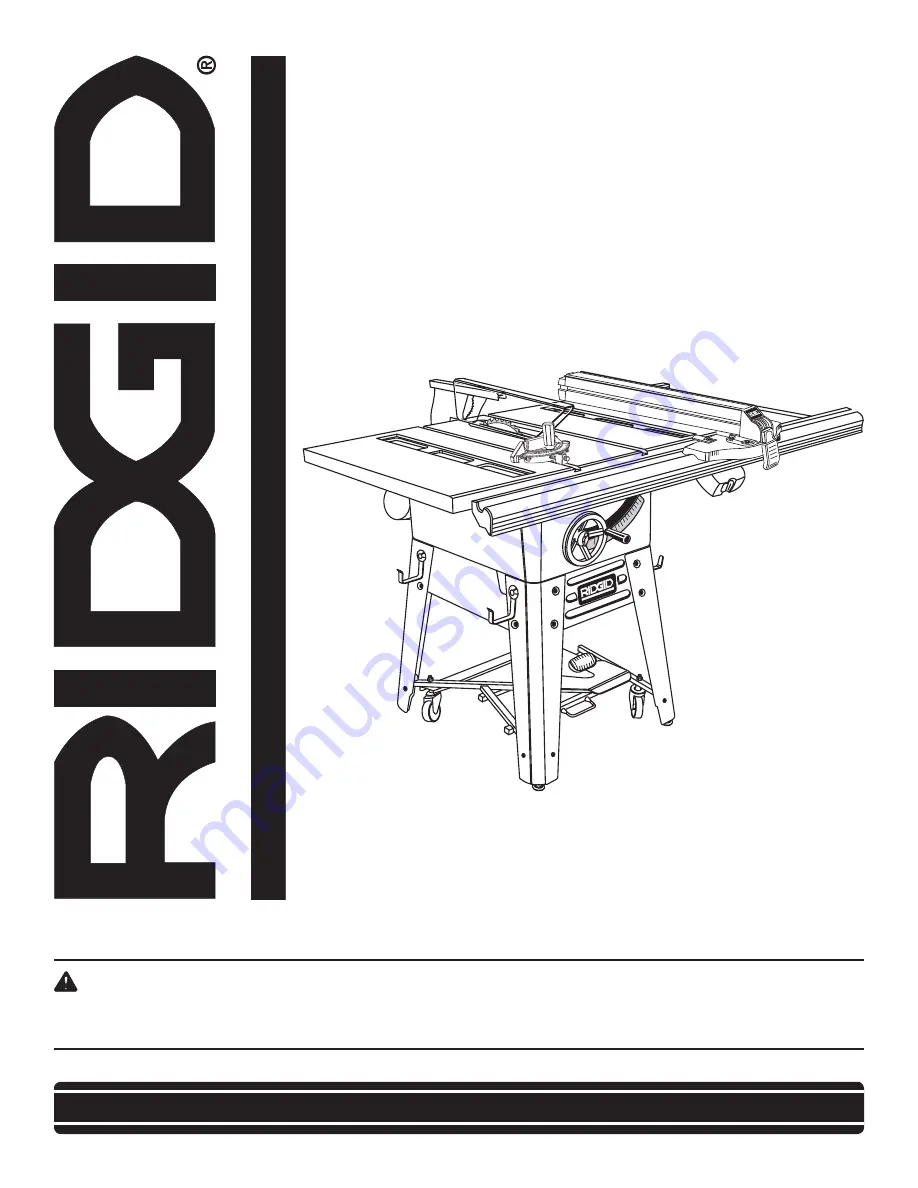
Your new table saw has been engineered and manufactured to our high standards for dependability, ease of operation, and
operator safety. When properly cared for, it will give you years of rugged, trouble-free performance.
WARNING:
To reduce the risk of injury, the user must read and understand the operator’s manual before using this
product.
Thank you for buying a RIDGID
®
product.
OPERATOR’S MANUAL
10 in. CAST IRON TABLE SAW
TS3660
SAVE THIS MANUAL FOR FUTURE REFERENCE