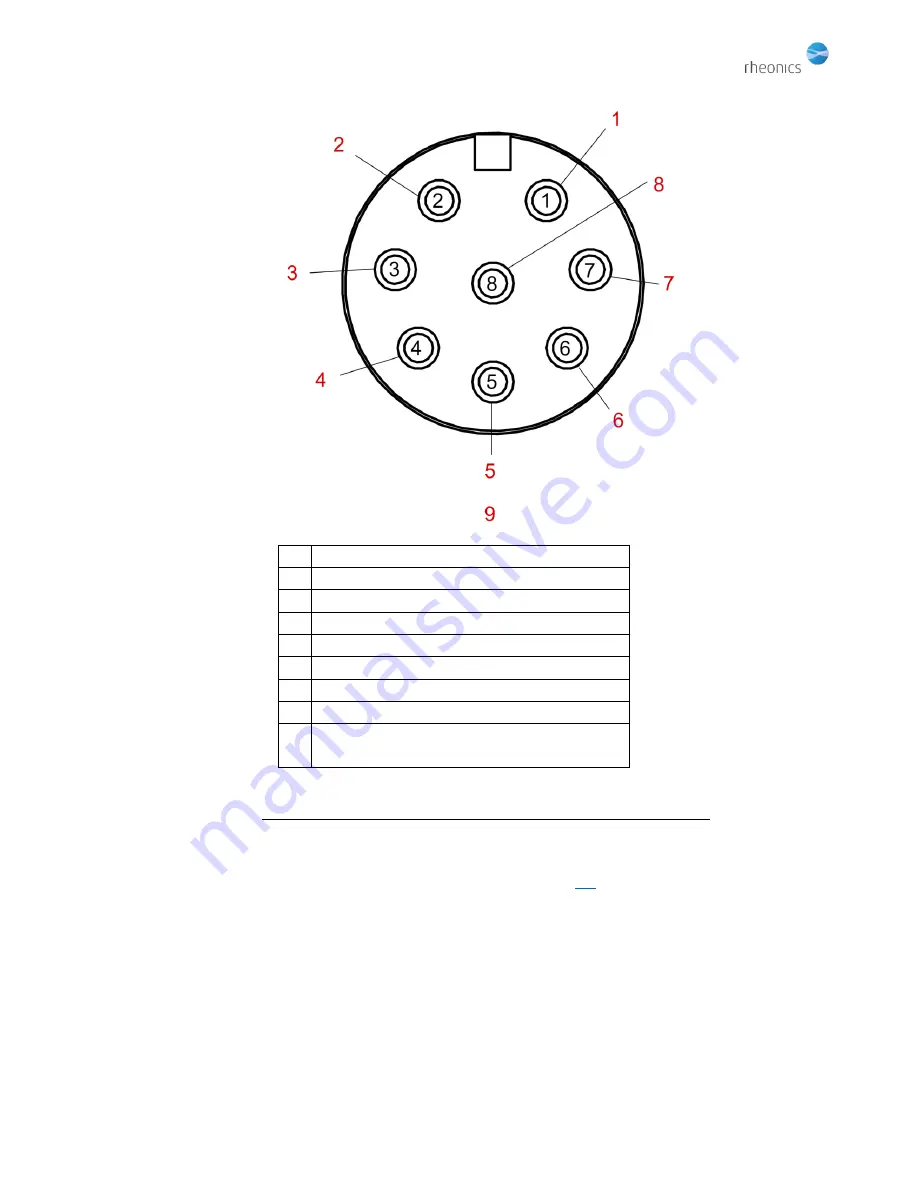
Rheonics | Switzerland | U.S.A.
SRV, SRD, SRV-FPC, SRD-FPC Installation and Intrinsic Safety Manual
P. 17
Version 2.0, Updated: October 29, 2020
Rheonics GmbH, Klosterstrasse 19, 8406 Winterthur, Switzerland
©Rheonics. Rheonics confidential and proprietary information.
1
1: Transducer coil +
2
2: Transducer coil -
3
3: No connect
4
4: No connect
5
5: Pt1000 Sens +
6
6: Pt1000 Gnd
7
7: Pt1000 I +
8
8: No connect
9
Signal assignment Pt1000 3-wire version
M12 connector front view
Figure 8: Pinout of M12 connector with 3-wire Pt1000 connection
In addition, the M12 connector must be rated at IP54 or higher.
Detailed pinout and connection diagrams are given in section
The cable and connector selected must be rated for at least the highest ambient temperature at
which the sensor will be used. They must meet the following specifications: