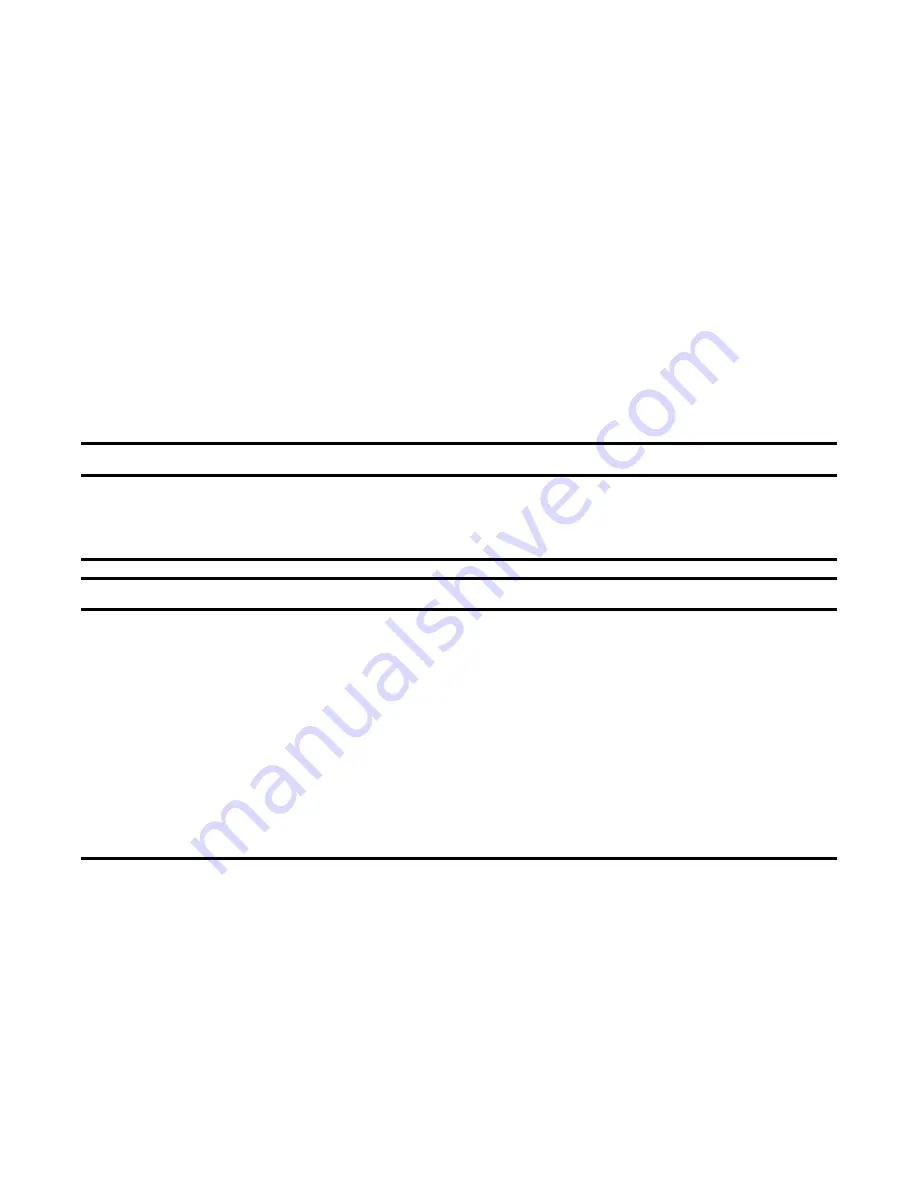
10
I-RIH (05-21) 131793-A
INSTALLATION
Pre-Installation Checklist
Check for any damage that may have been incurred during shipment .
If damage is found, document the damage with the transporting agency and immediately contact your distributor .
If you are an authorized Distributor, follow the FOB freight policy procedures .
Ensure that gas specifications and electrical characteristics of the unit are compatible with the gas and electric
supplies at the installation site .
Read this booklet and become familiar with the installation requirements of the unit .
If you do not have knowledge of local requirements, check with the local gas company or any other local agencies
who might have requirements concerning this installation .
Before beginning, make preparations for necessary supplies, tools, and manpower .
Before installing the unit, check the supporting structure to ensure that it has sufficient load-carrying capacity in
accordance with
section .
Mounting angle must be within the tolerance allowed .
Suspension Mounting
⚠ DANGER ⚠
The installer is responsible for suspension of the heater. Under no circumstances should either the
gas supply line or electrical supply line to the unit be used to provide assistance in suspension.
Do not run any gas or electric service lines above or below the heater or near the path of the flue
products.
⚠ CAUTION ⚠
• If a heater is located in an aircraft hangar or near overhead doors, it should be rigidly mounted
to prevent swinging.
• DO NOT ANGLE HEATERS MORE THAN 30 DEGREES OR LESS THAN 5 DEGREES. For proper
operation, the heater must be level, whether angle-mounted at 5 or 30 degrees. The heater is NOT
design-certified for use above 30 degrees (and voids the manufacturer’s warranty as well). A
horizontal or zero-degree angle is not recommended because flue gases coming off the burner
surface could potentially create an overheating condition for the gas controls. At a 5-degree
angle, a natural upflow of flue gases safely exits the heater.
• All models must be installed with the gas manifold located on the low end.
• Check local codes for mounting requirements and for permission to use flexible gas connectors.
Local codes may require rigid mounting. It is recommended that either the piping or the mounting
be flexible to prevent fatigue failure from vibration and/or thermal expansion.
•
Suspend the heater with the gas manifold located on the low end using either 3/8-inch (10-mm) threaded rod for
rigid mount or chain and S-hooks for chain mount (see
, DETAIL A) . Chain with a 200-pound (91-kg)
working load (1/0 Tenso) is recommended . S-hooks must be a minimum 1/4-inch (6 .3-mm) diameter wire and
must be closed after installation .
•
As an exception, it is permissible to suspend the following single-burner models with the gas valve on the high end:
RIHL unit size 050 and RIHN unit sizes 030 and 060 (see
, DETAIL B) . Mount these units with the gas
manifold (A) angled upward, the gas valve (B) toward the high side, and the mounting angle at 5- to 30-degrees .
•
, DETAIL C) . Suspend the heater as follows using either the chain and S-hooks provided in option UE1 or UE2
or field-supplied chain and S-hooks:
a . Securely connect one end of long chain to overhead building structure using S-hook A . Connect other end of
long chain to back of heater using S-hook B .