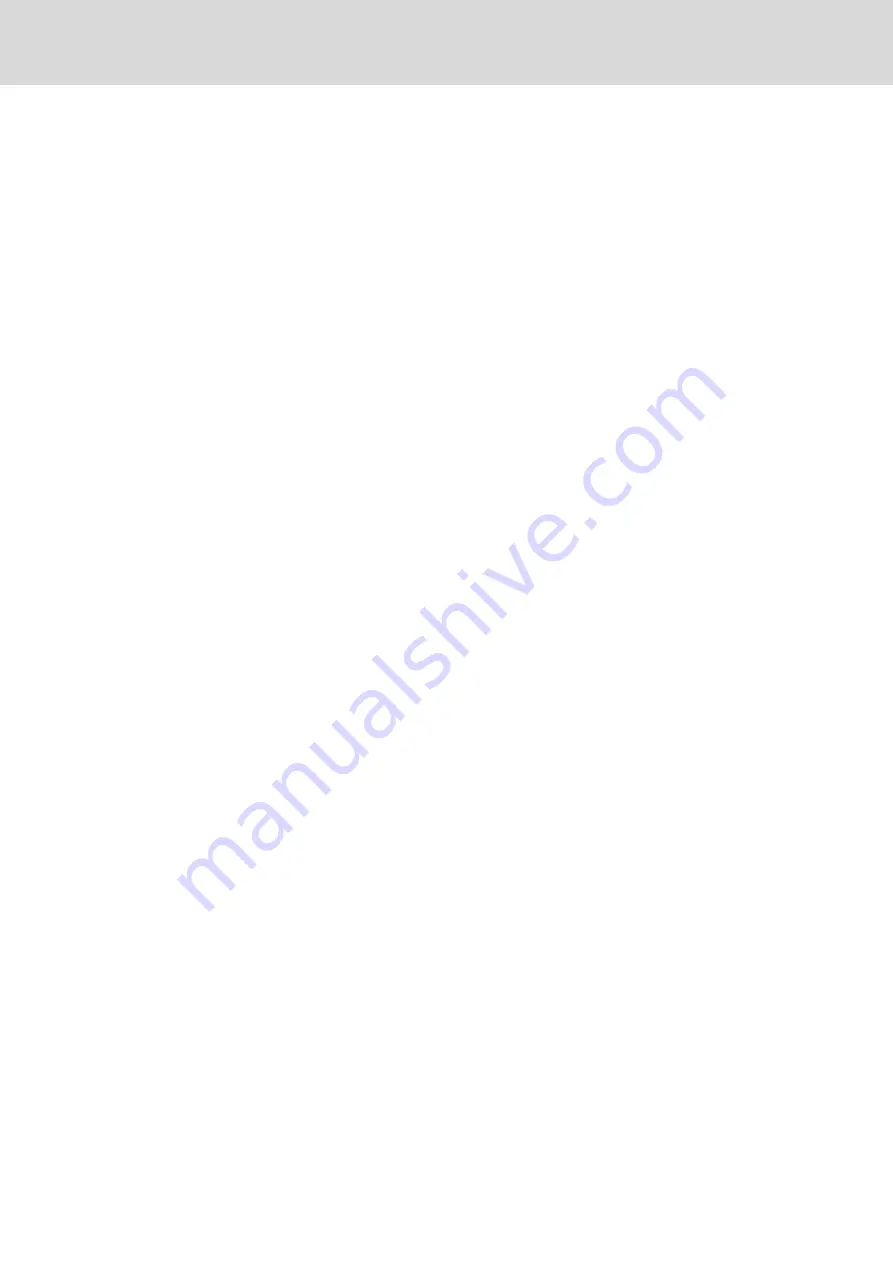
8.3.5
Grounding
An optimum grounding is required to keep away possible interferences from the
IndraControl L25 and the Rexroth Inline modules and to discharge them to the
ground.
Functional earth ground
The top-hat rail, which is used for mounting the IndraControl L25, must be
mounted to a grounded metal carrier, e. g. the rear panel of the control cabinet.
A functional earth ground is required to ensure optimum noise immunity. The
functional earth ground has to be connected via a cable, which is as short as
possible or preferably via a ground strap.
Recommended value:
Length: 1 m max.
Cross-section: 6 mm
2
The IndraControl L25 as well as the power and segment terminals are provided
with FE springs (metal clips) at their bottom side, which establish an electric
connection to the top-hat rail. To ensure a reliable ground connection even in
case of dirt or a damaged metal clip, the IndraControl L25 must be additionally
grounded via the FE terminal point, using a conductor with a cross-section of
at least 1.5 mm
2
.
The FE functional earth ground is used to discharge disturbances. It is not pro‐
vided as a protection against electric shock for persons.
Voltage jumper
Starting at the IndraControl L25, the FE (functional earth ground) voltage jump‐
er is routed through all connected Rexroth Inline modules. This ensures that
these modules are grounded once the ground connection of the IndraCon‐
trol L25, the supply terminals and the top-hat rail has been properly established.
Potential equalization
Potential equalization according to DIN VDE 0100 Part 540 must be provided
between the system parts and the voltage supply.
All components of the system have to be connected to the PE protective con‐
ductor system at the connectors that are marked accordingly.
8.3.6
Shield System
General Information
The shielding is intended to reduce any effects of interferences on the system.
The PROFIBUS line and the connection lines to modules for analog signals
must be shielded.
Observe the following when shielding:
●
Fit the shield over an area as large as possible under the clip in the shield
connector.
●
Ensure proper contact between the connector and the module.
●
Avoid damaging or squeezing cores. Avoid stripping the lines too much.
●
Connect the cores properly.
Shielding the PROFIBUS Cable
For noise immune transmission, Bosch Rexroth recommends a two-core twis‐
ted and shielded line pair, as specified as cable type A in EN 50 170, part 8-2.
Cable type B, which is also described in the above mentioned specification, is
obsolete and must not be used any longer.
The cable parameters are described in section
(only for Device Variant CML...PN...)" on page 38
.
DOK-CONTRL-IC*L25*****-PR03-EN-P
Rexroth IndraControl L25
Bosch Rexroth AG
53/69
Installation and Maintenance
Summary of Contents for IndraControl L25 CML...3N Series
Page 6: ...Bosch Rexroth AG DOK CONTRL IC L25 PR03 EN P Rexroth IndraControl L25 IV 69...
Page 22: ...Bosch Rexroth AG DOK CONTRL IC L25 PR03 EN P Rexroth IndraControl L25 20 69...
Page 30: ...Bosch Rexroth AG DOK CONTRL IC L25 PR03 EN P Rexroth IndraControl L25 28 69...
Page 44: ...Bosch Rexroth AG DOK CONTRL IC L25 PR03 EN P Rexroth IndraControl L25 42 69...
Page 58: ...Bosch Rexroth AG DOK CONTRL IC L25 PR03 EN P Rexroth IndraControl L25 56 69...
Page 66: ...Bosch Rexroth AG DOK CONTRL IC L25 PR03 EN P Rexroth IndraControl L25 64 69...
Page 68: ...Bosch Rexroth AG DOK CONTRL IC L25 PR03 EN P Rexroth IndraControl L25 66 69...
Page 71: ...Notes DOK CONTRL IC L25 PR03 EN P Rexroth IndraControl L25 Bosch Rexroth AG 69 69...