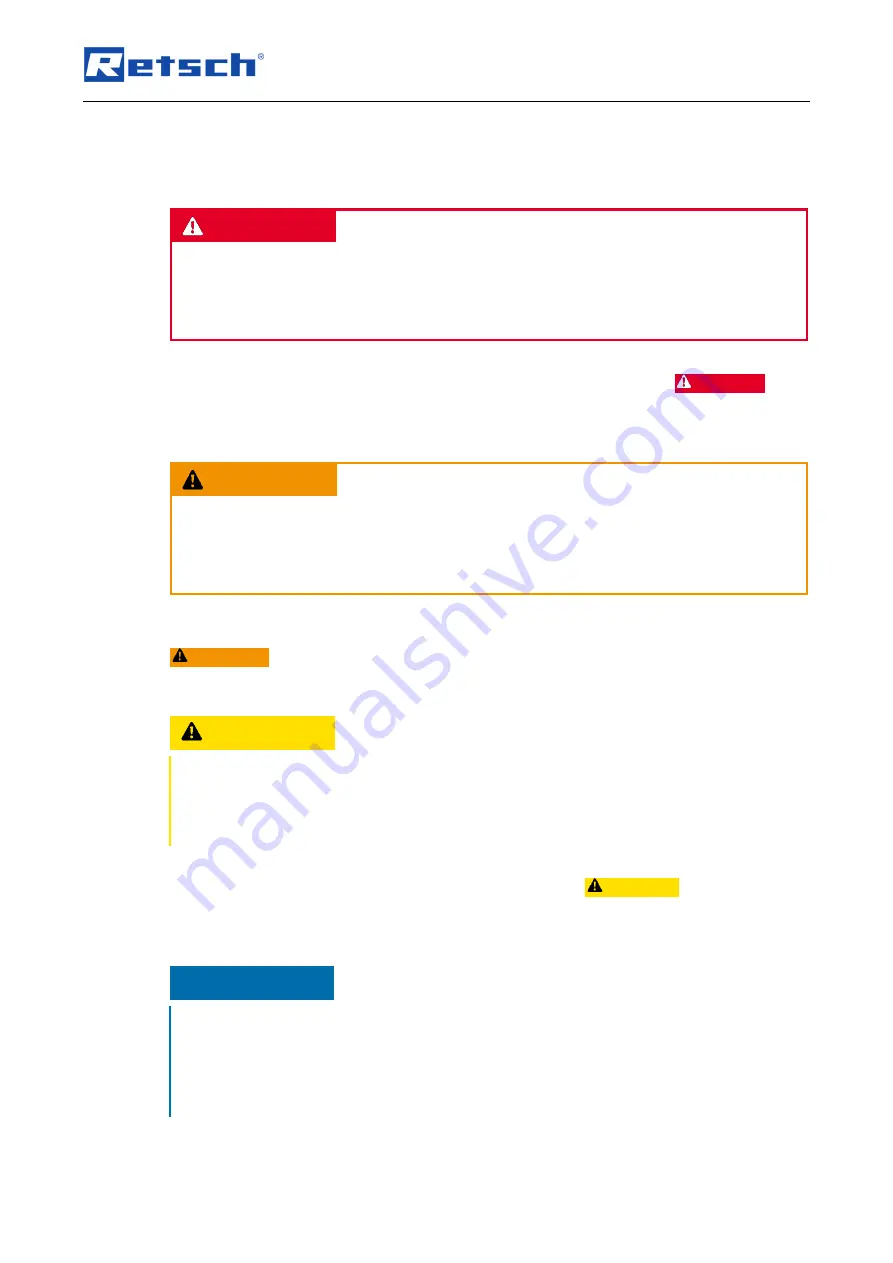
Notes on the manual
8
1.3 Explanations of the Safety Instructions
The following
warnings
in this manual warn of possible risks and damage:
DANGER
D1.0000
Risk of fatal injuries
Source of danger
−
Possible consequences if the danger is ignored.
•
Instructions and information on how to avoid the risk.
Fatal or serious injuries
may result if the “Danger” sign is disregarded. There is a
very high
risk
of a life-threatening accident or lasting personal injury. The signal word
DANGER
is
additionally used in the running text or in instructions.
WARNING
W1.0000
Risk of life-threatening or serious injuries
Source of danger
−
Possible consequences if the danger is ignored.
•
Instructions and information on how to avoid the risk.
Life-threatening or serious injuries
may result if the
“Warning” sign is disregarded. There is
an
increased risk
of a serious accident or of a possibly fatal personal injury. The signal word
WARNING
is additionally used in the running text or in instructions.
CAUTION
C1.0000
Risk of injuries
Source of danger
−
Possible consequences if the danger is ignored.
•
Instructions and information on how to avoid the risk.
Average to slight injuries
may result if the “Caution” sign is disregarded. There is an average
or slight risk of an accident or personal injury. The signal word
CAUTION
is additionally
used in the running text or in instructions.
NOTICE
N1.0000
Type of damage to property
Source of the damage to property
−
Possible consequences if the information is ignored.
•
Instructions and information on how to avoid the damage to
property.
Summary of Contents for RS 300
Page 2: ...2 Copyright Copyright by Retsch GmbH Retsch Allee 1 5 42781 Haan Germany ...
Page 5: ...Notes on the manual 5 ...
Page 7: ...Notes on the manual 7 ...
Page 22: ...Installation drawing 22 5 Installation drawing RS 300 construction size ...
Page 38: ...Operating the Device 38 Fig 31 Check safety ...
Page 48: ......
Page 49: ...Copyright Copyright by Retsch GmbH Retsch Allee 1 5 42781 Haan Germany ...