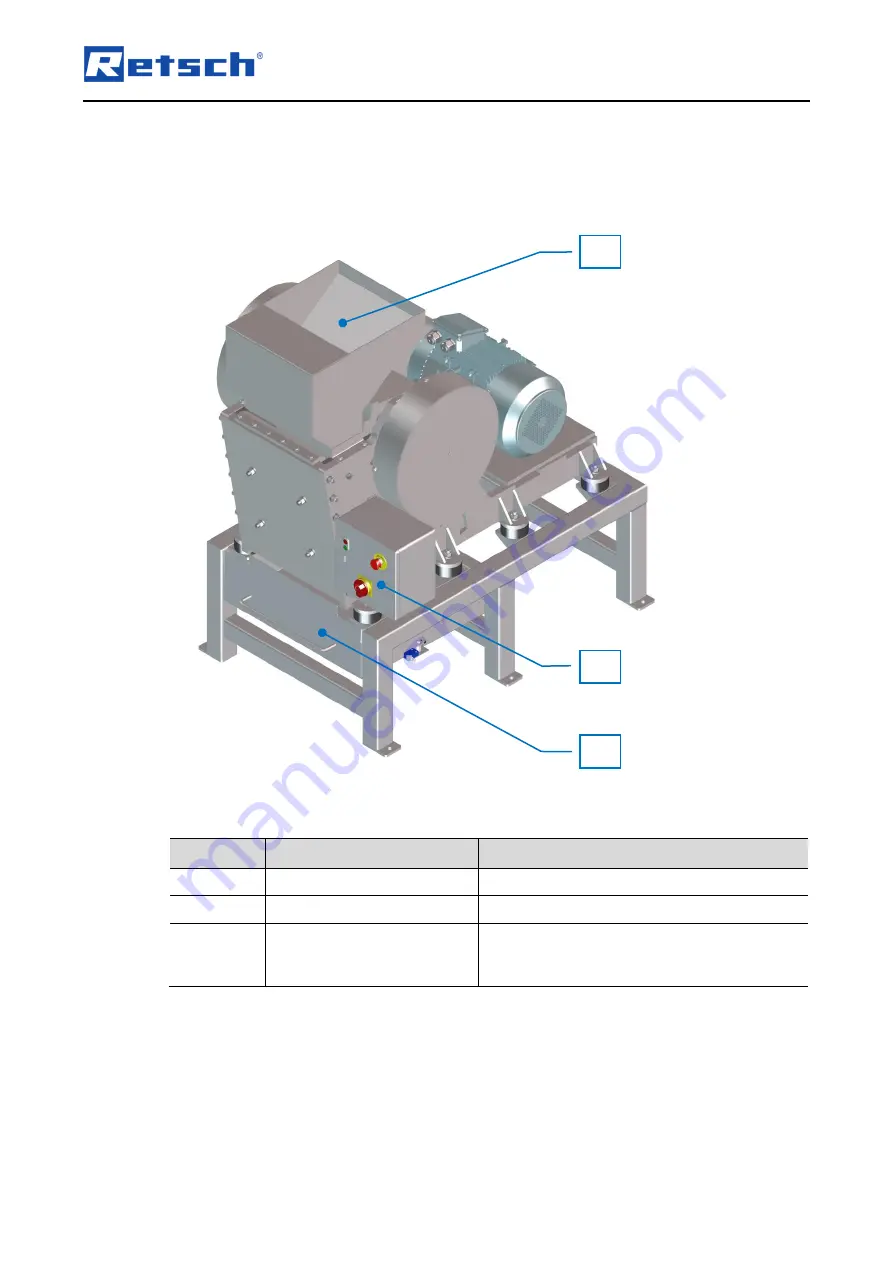
Views of the device
22
5
Views of the device
5.1 Front
Fig. 4:
Front view
Element
Description
Function
A
Feed hopper
For adding material.
B
Control element
For operating and controlling the machine.
C
Collecting receptacle
Collects the sample material.
The limit switch in the base frame actuates if the
collecting receptacle is removed during operation.
A
B
C