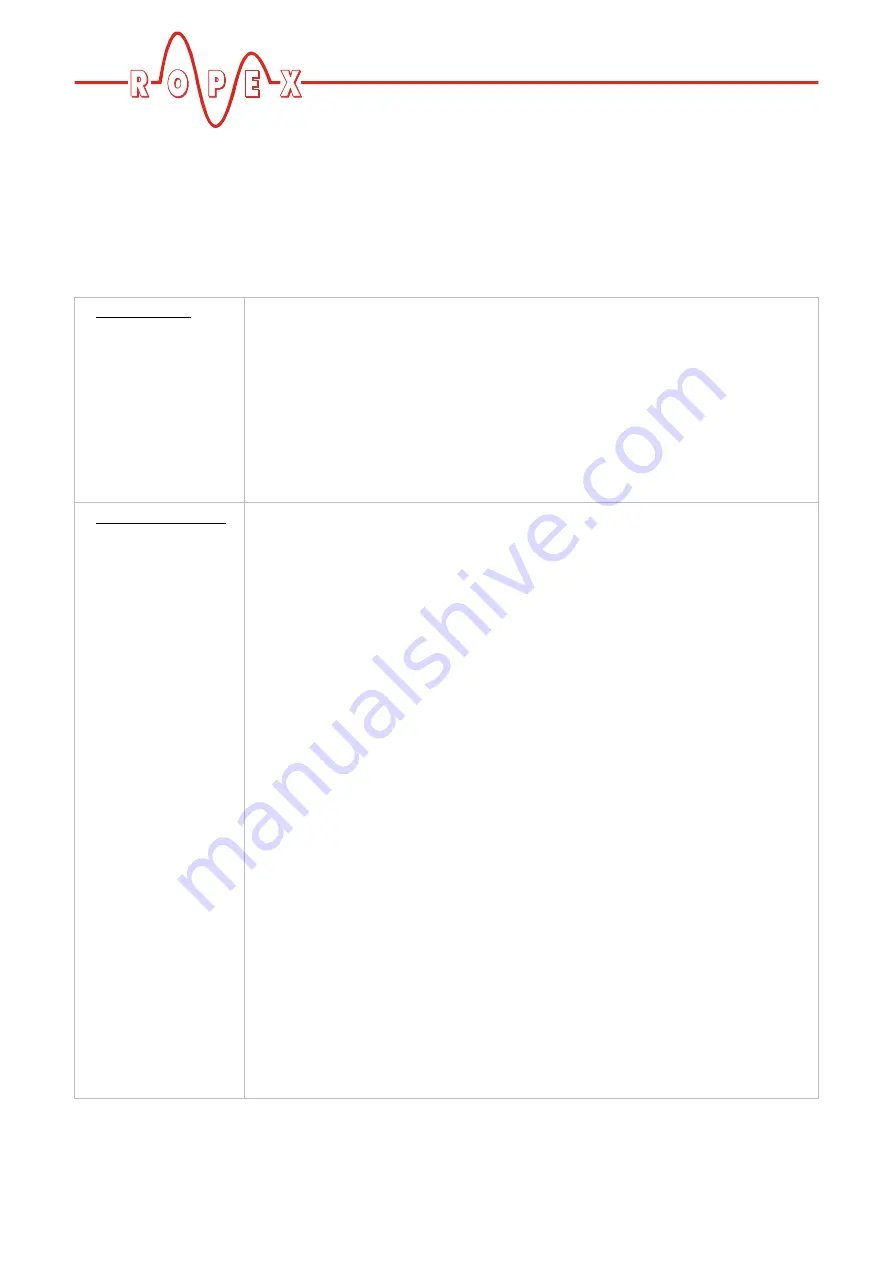
Factory settings
48
RES-430
11
Factory settings
11.1
Ropex settings
The RES-430 RESISTRON temperature controller is
configured in the factory as follows (Ropex settings):
Settings menu
Step 101 Heatsealing temperature:
0°C
Step 103 Starting delay:
0s
Step 104 Heatsealing time:
1s
Step 105 Cooling value:
Cooling time:
10 s
Absolute cooling temp.:
50°C
Relative cooling temp.:
40 % of
heatsealing
temperature
Step 106 Hold mode:
OFF
Step 107 AUTOCAL temperature:
20°C
Configuration menu
Step 201 Language
German
This selection is NOT changed if the factory settings are restored
with step 202 in the Configuration menu
Step 203 Alloy/TCR:
1100ppm, Alloy-20
Step 204 Variable temp. coeff.:
1100ppm
Step 205 Temperature range:
300°C
Step 206 Maximum temperature:
300°C
Step 207 Set point reached:
-10K
Step 208 Set point exceeded:
+10K
Step 210 Cooling mode:
Absolute
Step 211 Start of heatsealing time:
When temperature reached
Step 212 Relay K1 function:
Active when "START" signal present
Step 213 Lock "HAND" key
OFF
Step 214 Cycle counter:
0
Step 217 Temperature diagnosis:
OFF
Step 218 Temp. diagnosis delay:
0s
Step 219 Heatup timeout:
OFF
Step 221 Autocomp:
OFF
Step 225 Temperature unit:
Celsius
Step 240 Single/double sealing:
Double
Step 241 Sensor mode:
OFF
Step 242 Load cell minimum force:
0N
Step 243 Load cell maximum force:
1500N
Step 244 Load cell tare:
0N
Step 245 Load cell reference force:
680N
Step 246 Max. sensor temperature:
50°C
Step 247 Force diagnosis:
OFF
Step 248 Force diagnosis delay
0s
Step 249 Foot switch hold time:
0s