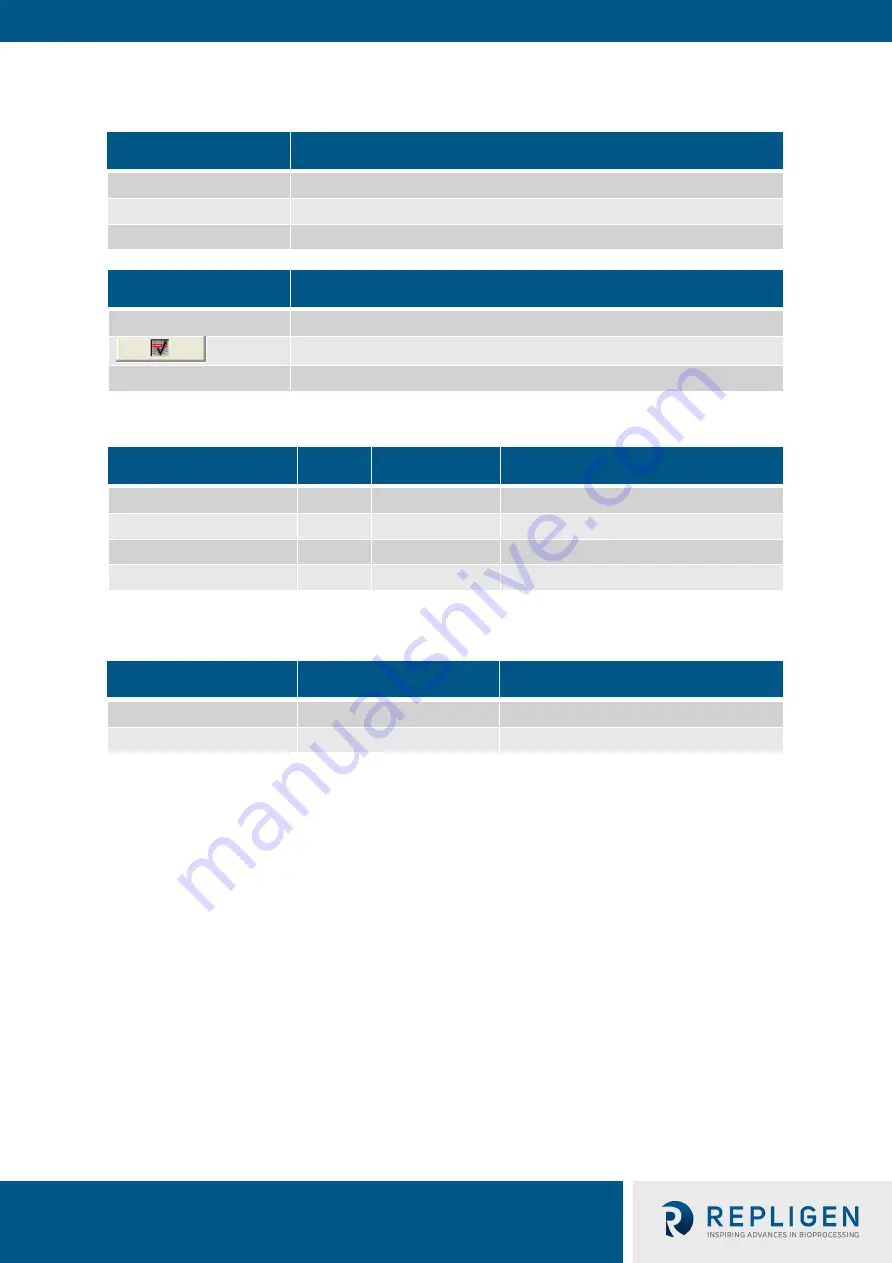
XCell™ C410:V3 Controller
User Guide
32 repligen.com UG-C410v3-06
Table 12. The Alarm screen display parameters
Field
Description
Time
Indicates time of alarm
Date
Indicates date of alarm
Text
Describes alarm
Button
Description
Horn acknowledge
Press to turn off horn
Select highlight Warning/Alarm message and press to remove
All Primary
All Primary screen buttons are displayed to navigate to those screens
Table 13. Two (2) Pump controller status relay states
XCell ATF® Device states State # Relay #1
Relay #2
Power Off/Alarm
A
Off
Off
Power On/Standby
B
Off
On
Power On/Running
C
On
On
Power On/Warning
D
On
Off
Table 14. Two (2) Pump interlock relay states
Harvest pump state
Relay #3
Relay #4
Active
On
On
Not Active
Off
Off
An isolated Form C contact for each relay is provided for the end user to connect to any remote
monitoring system. The Harvest pump is activated to Run mode, only and only if Relay #1 is ON, i.e.
in Power On/Running state #C or Power On/Warning state #D.
The following is a list of XCell™ C410:V3 Controller warnings that can occur during normal operation:
•
Flow Set Point cannot be reached. P-Flow Regulator (PV1) above maximum operating
setting.
•
Flow Set Point cannot be reached. P-Flow Regulator (PV1) below minimum operating
setting.
•
Exhaust Set Point cannot be reached. E-Flow Regulator (PV2) above maximum operating
setting.
•
Exhaust Set Point cannot be reached. E-Regulator (PV2) below minimum operating setting.