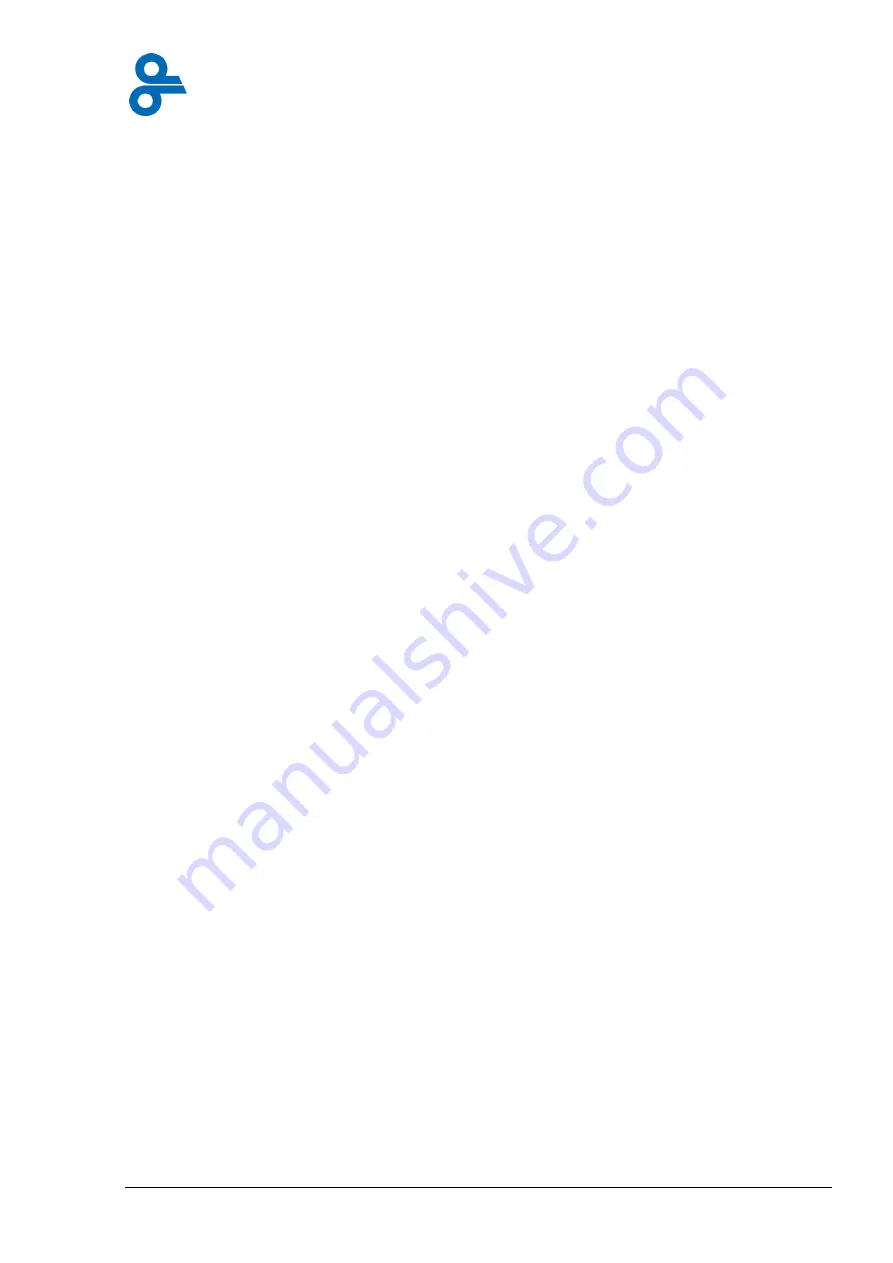
126
6.3
Maintenance instructions
Before working on the machine, first ensure that the machine is switched off (disconnect the power cable
and remove the safety cover). Take care with the pneumatic installation! Read the manual for the safety
instructions. Work can be started as soon as all necessary precautions have been taken. Only qualified
mechanics may work on the machine!
After the activities, ensure that the machine is in proper condition. All safety facilities must also be present
(replaced) and must function properly before the machine is restarted.
6.3.1 Conveyor chain
Chain
After assembling the chain, it is always pre-loaded by the chain manufacturer. Pre-loading approximates
the maximum allowable load and is applied to ensure that all chain components such as pins, bushes and
plates are properly in place. By pre-loading a chain, initial stretch is minimized. As this increases the
service life of the chain, this is an important part of the production process.
Chain extension is not caused by deformation of the plates, but by wear of the pin and the bush. For a
chain to still function without any problems with chain wheels having less than 60 teeth, the maximum
permissible extension is 1.5%. A roller chain will extend somewhat after installation of the chain. This is
normal, the initial extension amounting to about 0.05%. This initial extension must be compensated with
the chain tensioner.
Preliminary activities
Before carrying out maintenance work to the conveyor chain, check the entire chain (both sides), for
damage, contamination and corrosion. Remove any film and / or product residue. In case of damage,
restore the chain (claws and/or springs) If corrosion has (started to) set in, reconsider the lubricating
intervals and make use of aggressive cleaning agents. If in doubt, consult the distributor.
Chain tension adjustment
The chain tends to stretch a certain amount immediately after installation of the chain. This is caused by
running-in of the components. After this initial extension (about 0.05%), the chain will (uniformly) extend
somewhat, as a result of normal wear. This must be compensated by, for instance, a chain tensioner. In
order to maintain correct chain tension, it is necessary to check it regularly and if necessary take
corrective action. The following inspection scheme is advised based on 8 working hours per day. The
application, or the environmental conditions, can necessitate a different (shorter) interval. If the scheme is
not adhered to, this will increase the chance of premature wear, damage and / or accidents.
For the first week after installation of the chain: 1 x per day.
From the second up to and including the fourth week after installation of the chain: 2 x per week.
After the first month: 1 x per week.
If the chain tensioners have insufficient span, then at least 2 links must be removed (always on both
sides). Because the 2 chains are tensioned in the machine in parallel by 2 individually operating
tensioners, extra attention must be paid to an identical tension for both chains. Unequal adjustment can
cause overload of the chain (damage / wear), or poor functioning of the machine.
Correct chain tension is very important. If it is not correct, it can cause various problems. For instance: too
little chain tensioning can cause poorly aligned cross-cutting or printed top film. Unequal chain tensioning
on both chains may cause creases in the film. If the chain tension is too high, this will lead to premature
extension (wear) of the chain and / or damage the machine.
An exact value for the chain tension cannot be given because this depends on various factors. Keep the
chain tension as low as possible, so that the machine still functions properly. As a rule of thumb, the chain
section between the drive chain wheel and the chain tensioner should be able to be depressed by hand
between 2 mm and 8 mm.