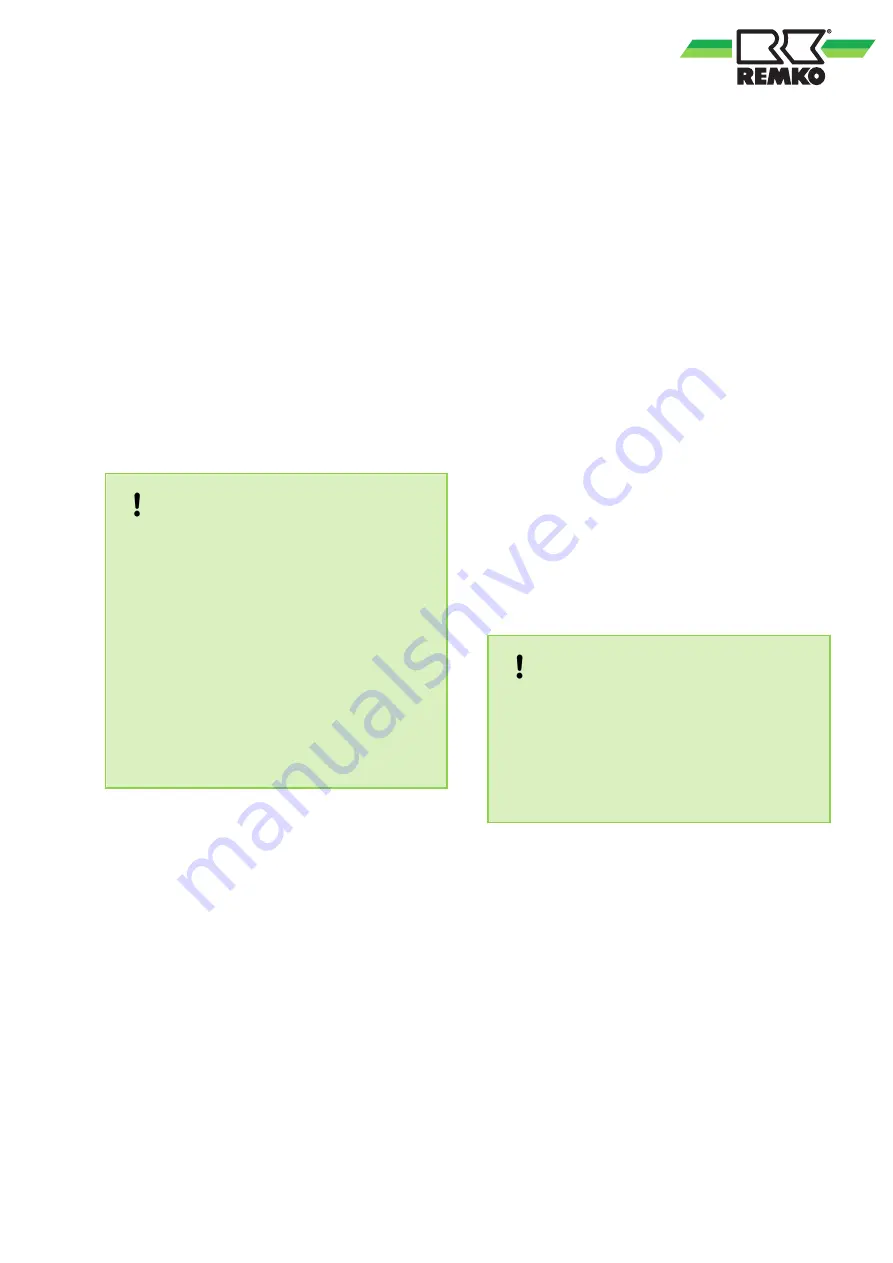
1.6 Safety instructions for the oper-
ator
The operational safety of the units and compo-
nents is only assured providing they are used as
intended and in a fully assembled state.
n
The units and components may only be set up,
installed and maintained by qualified per-
sonnel.
n
The existing regulations concerning accident
prevention must be adhered to.
n
Do not operate units or components with
obvious defects or signs of damage.
n
Contact with equipment parts or components
can lead to burns or injury.
n
Ensure that electrical energy does not pose a
risk.
n
Regulations of the VDE and the local energy
supply company must be adhered to.
NOTICE!
Material damage due to mineral oils!
Mineral oil products permanently damage
EPDM seal elements; the sealing properties
may therefore be lost. We do not take responsi-
bility or provide warranty replacements for
damage caused by seals that are damaged in
this way.
–
It is essential that you prevent EPDM from
coming into contact with mineral oil sub-
stances.
–
Use a lubricant that is free of mineral oil and
has a silicone or polyalkylene basis, such
as Unisilkon L250L and Syntheso Glep 1
made by Klüber, or a silicon spray.
1.7 Safety notes for installation and
inspection tasks
n
The operator must ensure that all inspection
and installation work is carried out by author-
ised and qualified personnel who have thor-
oughly read the operating manual.
n
Works on the pump/system may only be car-
ried out whilst at a standstill as a matter of prin-
ciple.
n
Appropriate hazard prevention measures must
be taken to prevent risks to people when per-
forming installation, repair, maintenance or
cleaning work on the units.
n
The setup, connection and operation of the
units and its components must be undertaken
in accordance with the usage and operating
conditions stipulated in this manual and comply
with all applicable regional regulations.
n
Regional regulations and laws as well as the
Water Ecology Act must be observed.
n
The power supply should be adapted to the
requirements of the units.
n
The units and components must be kept at an
adequate distance from flammable, explosive,
combustible, abrasive and dirty areas or
atmospheres.
n
Safety devices may not be modified or
bypassed.
NOTICE!
Malfunction!
The fresh water module must be integrated into
the equipotential bonding system of the elec-
trical installation. If this is not ensured by the
pipe network, set up an approved potential
equalisation connection to the main potential
connection.
1.8 Unauthorised modification and
changes
The operational safety of the fresh water module
that was delivered is guaranteed only with
intended use in accordance with section 1.8 of the
operating instructions. Under no circumstances
should the threshold values specified in the data-
sheet be exceeded.
Modifications or changes to units and components
are not permitted and may cause malfunctions.
Safety devices may not be modified or bypassed.
Original replacement parts and accessories
authorised by the manufacturer ensure safety. The
use of other parts may invalidate liability for
resulting consequences.
5