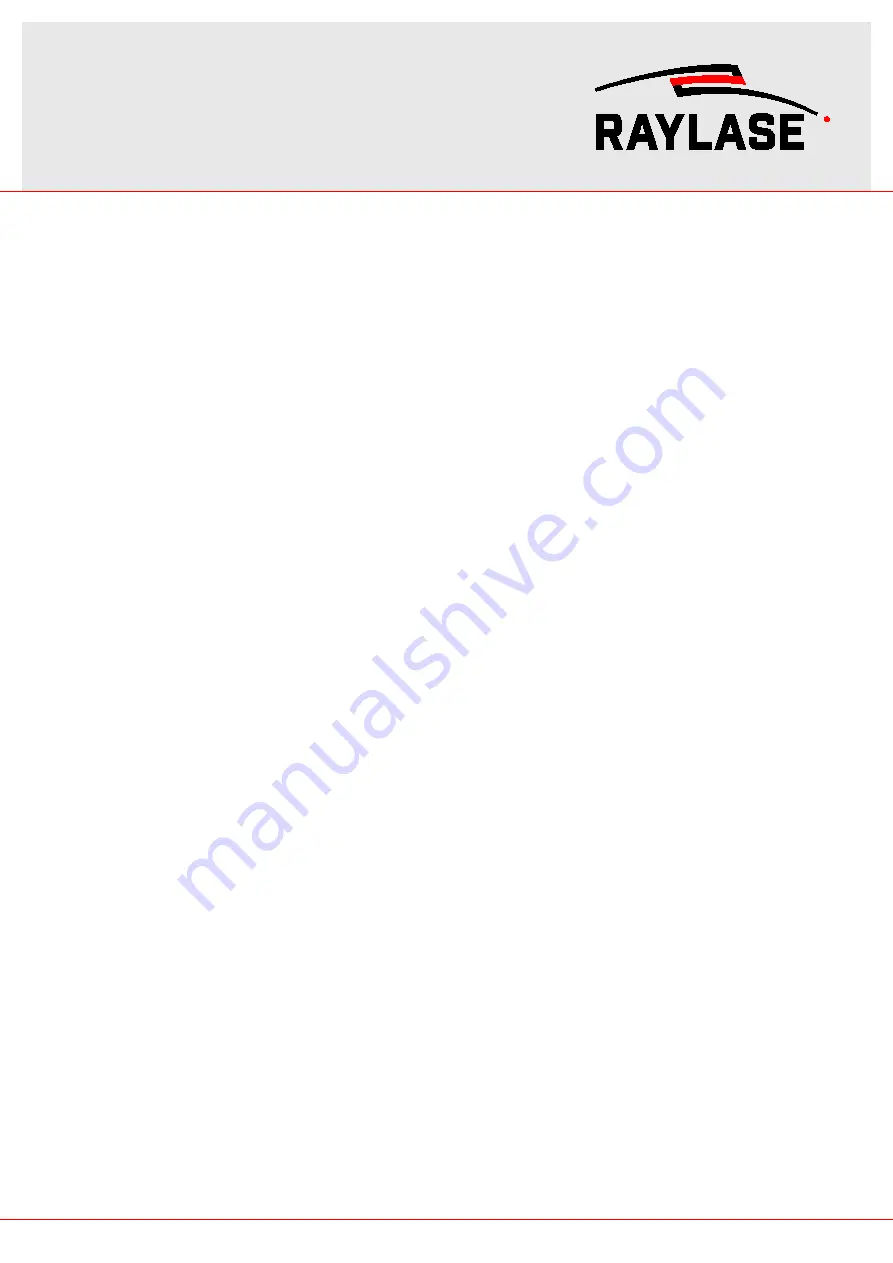
3 PRODUCT DESCRIPTION
© 2022 RAYLASE GmbH SUPERSCAN IV
MN105-en / v1.0.12
26
3.7.9
Interfaces
The deflection unit has a connection for SL2-100 data signals, for power supply and optionally for
XY2-100 data signals. The details are described in the subsequent chapters.
3.7.9.1
XY2-100 Interface
This interface can be used to connect the deflection unit to a RAYLASE control card. The detailed
information for the interface is set out below.
This interface is compatible to the XY2-100 enhanced protocol of RAYLASE.
The SUPERSCAN IV’s digital controller makes it possible to return data-signals to the control card. Data
are transferred every 10 µs to the controller card via the interface. There is one return channel for each
axis. This allows, for instance, monitoring the current axis positions during processing, or detailed
failure analysis following a malfunction.
Each axis also has a forward channel that can transfer a data packet to the scan head every 10 µs:
normally, these will be target positions for the axis.
Whenever it becomes necessary to transfer a command to the scan head during processing, e.g. to
change the type of information supplied on the return channel, the usual transmission of target
positions is suppressed for one 10 µs period. To avoid undesirable processing artefacts due to the
missing target position, a minimum interpolation period of 22 µs should be configured on the scan
head. The currently configured interpolation period can be retrieved via the command
SetMode
Interpolation Configuration 0x0590
, and set with the command
SetInterpolation 0x90
.
If the scan head’s interpolation period is re-configured, it will also be necessary to adjust the laser-
delay settings to suit. The interpolation period has no effect on the dynamic behaviour of the scan
head.
All commands and the extensive capabilities of the functionally enhanced XY2-100 interface are
described in detail in the manual
SS-IV and SS-V Enhanced
, which can be found on the supplied USB
stick.
Optional