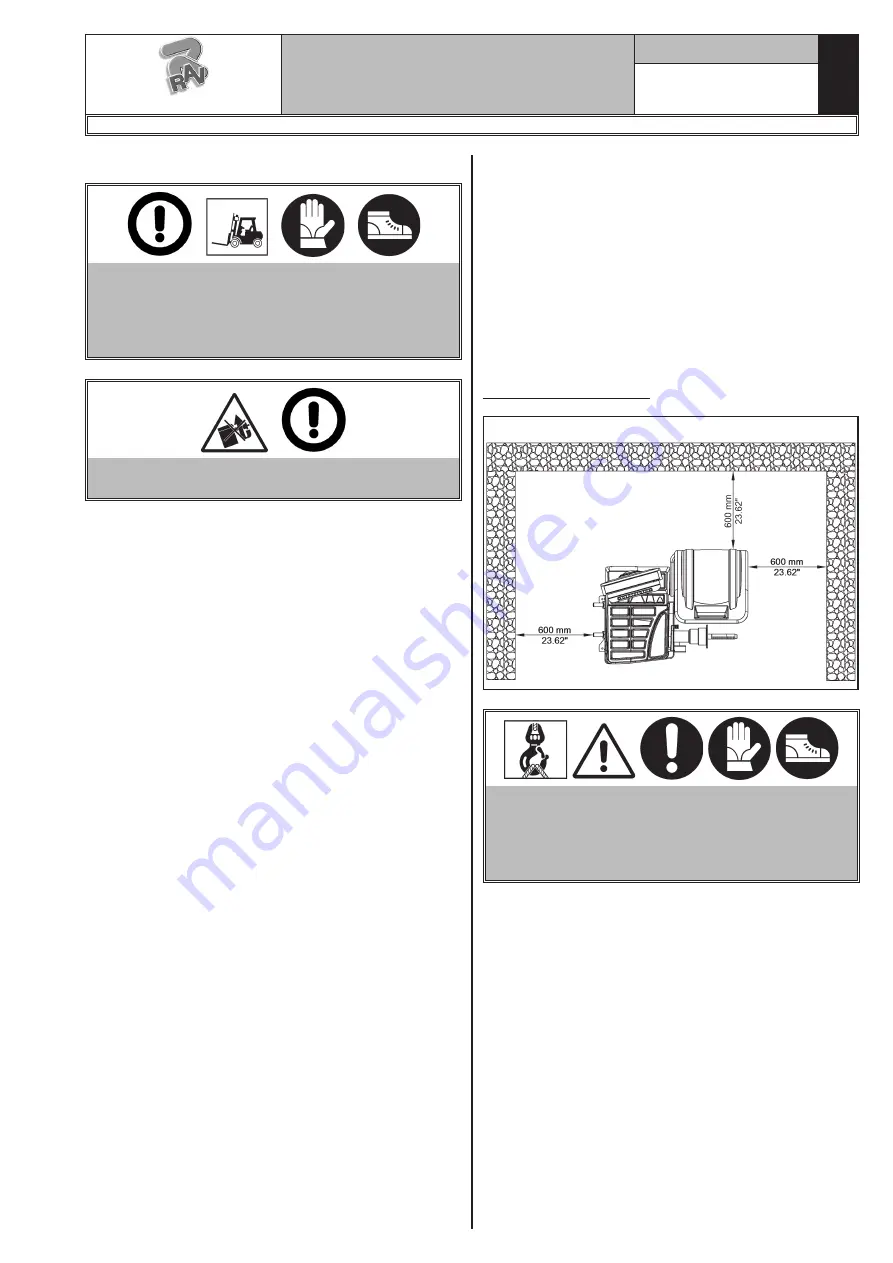
EN
Page 14 of 91
INSTRUCTION, USE AND
MAINTENANCE MANUAL
7.0 MOBILIZATION
THE LIFTING EQUIPMENT MUST WITHSTAND
A MINIMUM RATED LOAD EQUAL TO THE
WEIGHT OF THE MACHINE (SEE PARAGRAPH
TECHNICAL SPECIFICATIONS). DO NOT AL-
LOW THE LIFTED MACHINE TO SWING.
NEVER LIFT THE MACHINE BY MEANS OF THE
CHUCK.
If the machine has to be moved from its normal work
post, the movement must be conducted following the
instructions listed below.
• Protect the exposed corners with suitable material
(Pluribol/cardboard).
• Do not use metallic cables for lifting.
• Make sure the power and pneumatic supply (on
models with pneumatic chuck) of the machine are
not connected.
• Place again the machine onto the original pallet with
whom it was delivered.
• Use transpallet or fork-lift for handling.
8.0 WORKING ENVIRONMENT CONDI-
TIONS
The machine must be operated under proper condi-
tions as follows:
• temperature: 0° + 45° C
• relative humidity: 30 - 90% (dew-free)
• atmospheric pressure: 860 - 1060 hPa (mbar).
The use of the machine in ambient conditions other
than those specified above is only allowed after prior
agreement with and approval of the manufacturer.
8.1
Working area
Fig. 3
USE THE MACHINE IN A DRY AND AD-
EQUATELY LIT PLACE, POSSIBLY INDOORS
OR ANYWAY IN A ROOFED AREA, THIS PLACE
MUST BE IN COMPLIANCE WITH APPLICABLE
SAFETY REGULATIONS.
The location of the machine requires a usable space
as indicated in
Fig. 3
. The positioning of the machine
must be according to the distances shown. From the
control position the operator is able to observe all the
machine and surrounding area. He must prevent unau-
thorized personnel or objects that could be dangerous
from entering the area.
The machine must be fixed on a flat floor surface,
preferably of cement or tiled. Avoid yielding or irregu-
lar surfaces.
The base floor must be able to support the loads trans-
mitted during operation.
This surface must have a capacity load of at least 500
kg/m².
The depth of the solid floor must be sufficient to guar-
antee that the anchoring bolts hold.
G3.150 - GP3.150 - G3.150S - GP3.150S - G3.150WS - GP3.150WS - G3.150WSPLUS - GP3.150WSPLUS - G3.150SA - G3.150WSA
RAVAGLIOLI S.p.A.
1297-M058-00