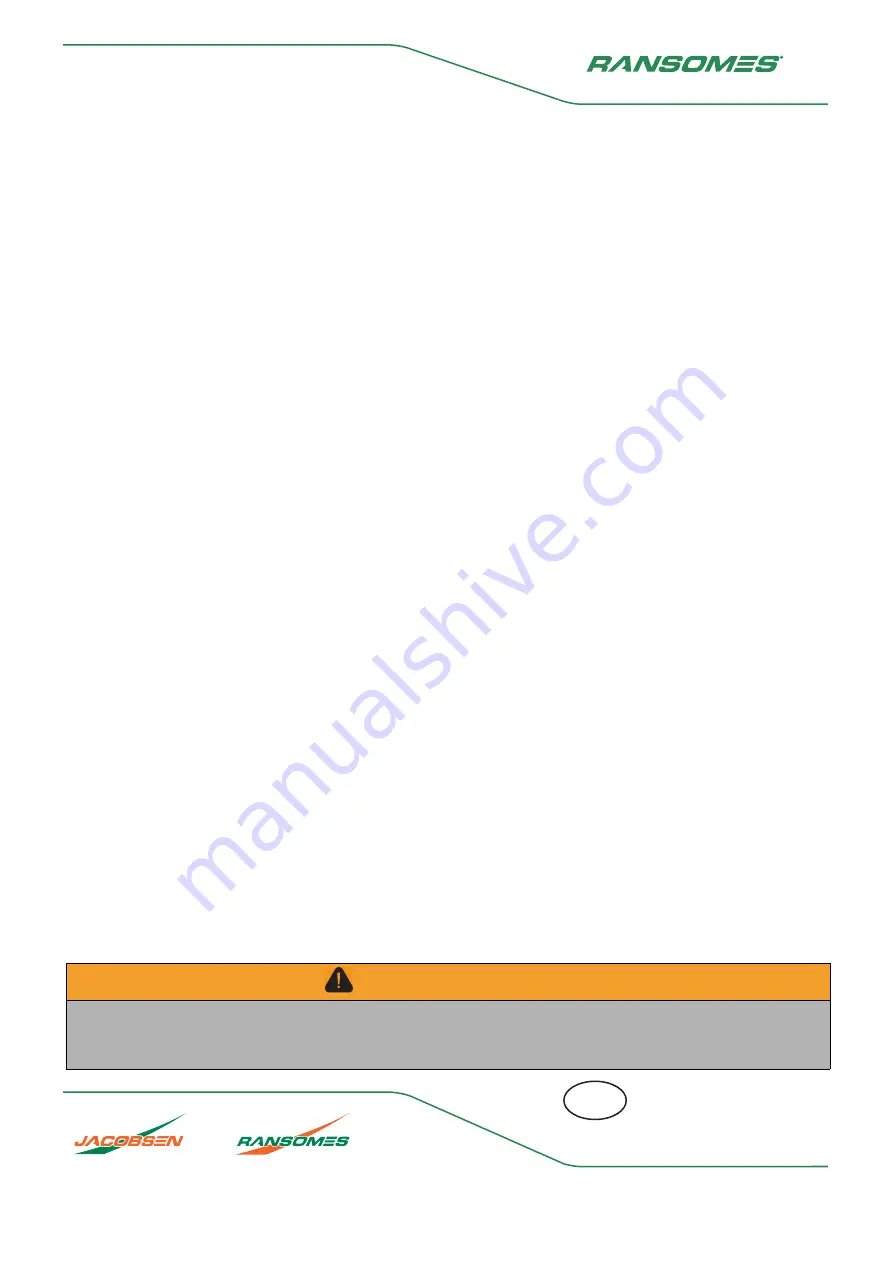
Safety, Operation & Maintenance Manual
Ransomes HM600, Kubota
®
V2403-CR-TE4, 4WD with ROPS
Ransomes HM600, Kubota
®
V2403-CR-TE4, 4WD with Cabin
Series: ZA / DB
Product code: RHM600 / RHM600C
WARNING
WARNING: If incorrectly used this machine can cause severe injury. Those who use and maintain this
machine must be trained in its proper use, warned of its dangers and must read the entire manual before
attempting to set up, operate, adjust or service the machine.
678141-GB (r.0)
RJL 100 July 2018
GB
United
Kingdom
Summary of Contents for HM600
Page 8: ...en 8 2 INTRODUCTION NOTES...
Page 50: ...en 50 5 CONTROLS NOTES...
Page 115: ...en 115 QUALITY OF CUT 10 NOTES...