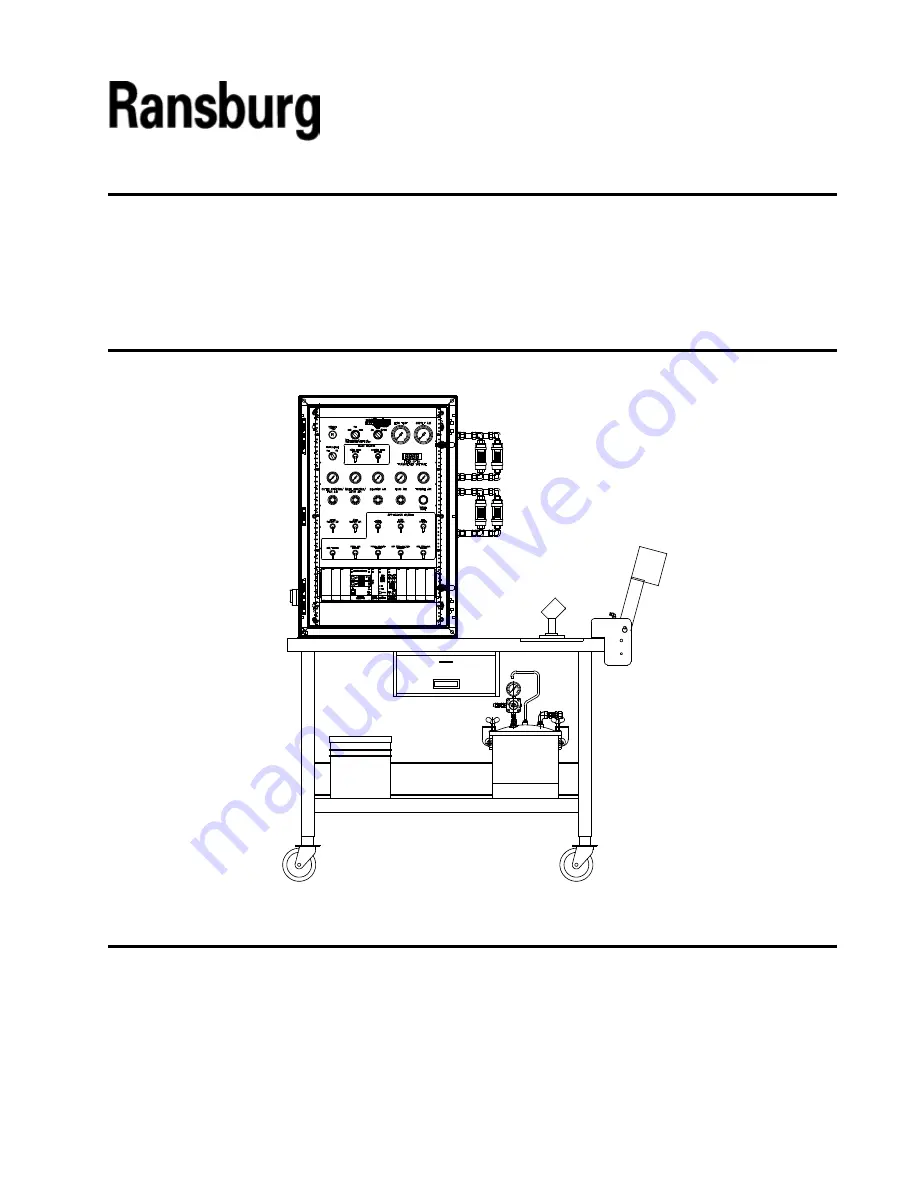
IMPORTANT: Before using this equipment, carefully read
SAFETY PRECAUTIONS, starting on page 1, and all
instructions in this manual. Keep this Service Manual for
future reference.
SERVICE MANUAL
LN-9259-07.1
Replaces LN-9259-07
April - 2013
RMA-303 INDIRECT / RMA-303 DIRECT
EVOLVER 303 / EVOLVER NE
TEST STATIONS
Service Manual Price:
$30.00 (U.S.)
TURBINE
S.A.O./FAN
S.A.I./ATOM
DESC
MANUFACTURER
CAT
MANUFACTURER
CAT DESC
160
160
DESC
MANUFACTURER
CAT
100
100
100
100
100
BEARING AIR