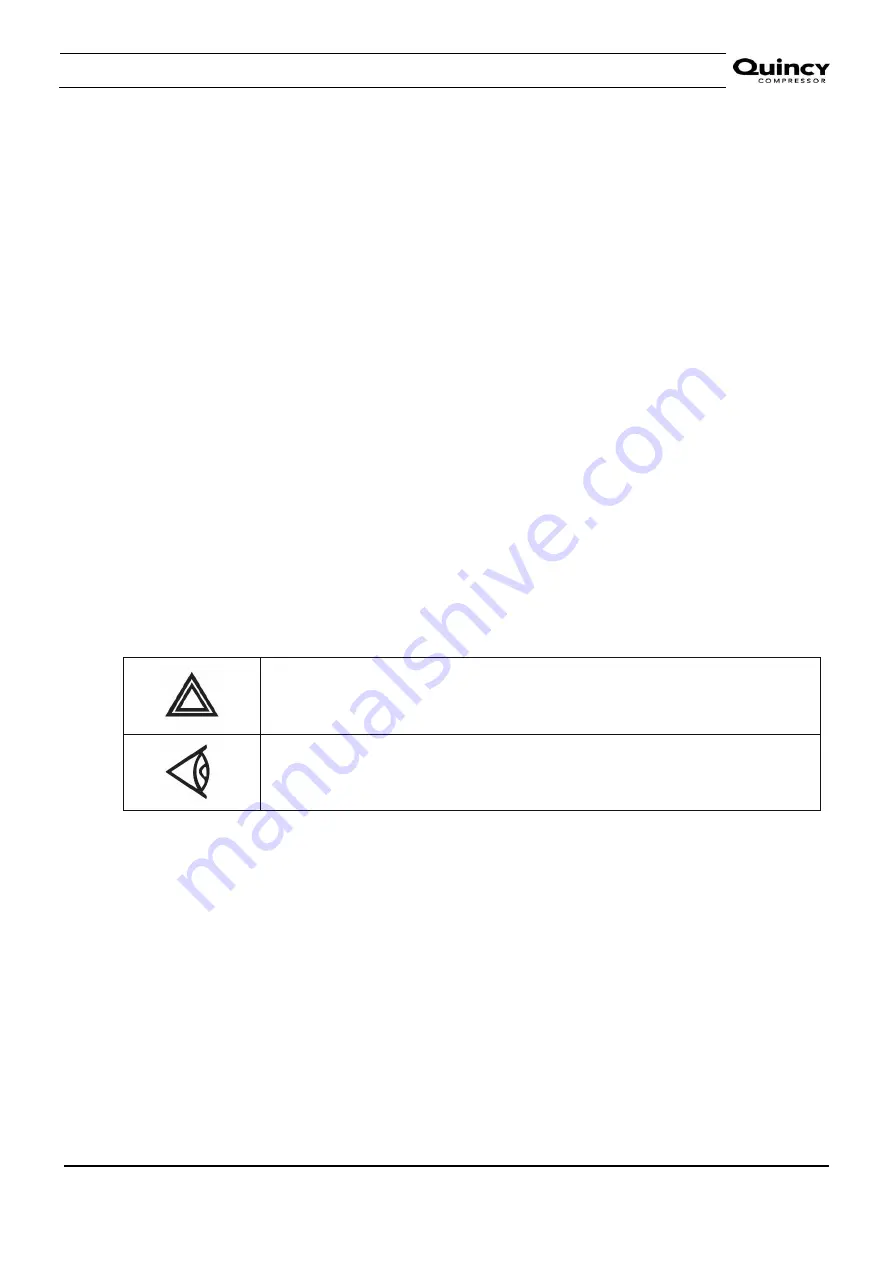
Instruction book
9829 2151 14
81
5
Operating instructions
5.1 Initial start-up
Description
To start up the dryer for the first time or after a long period of standstill, proceed as follows:
1. Open the dryer bypass valves, if installed.
2. Close the air supply towards the PDP-sensor and unplug the PDP-sensor.
3. Cut off the air supply from the compressor towards the dryer by closing the external inlet valve, if
installed.
4. Close the external outlet valve, if installed.
5. Start the compressor and wait for pressure.
6. Slowly open the external inlet valve, if installed.
7. Check the connections of the dryer for air leaks and repair if necessary.
8. Switch on the voltage to the dryer.
9. Switch on the dryer.
10. Let the dryer operate for several hours with the external outlet valve closed.
11. Gradually open the external outlet valve, keeping the pressure inside the dryer above 4.5 bar
(65.3 psi).
12. As required, close the bypass valves of the dryer.
13. Press the stop button 0 and switch off the voltage to the dryer.
14. Plug the PDP-sensor.
15. Open the air supply towards the PDP-sensor.
At initial start-up, dust can be released. It is recommended to replace the
cartridges of the silencers and the after filters, if installed, after approximately one
week of operation.
If the application allows air that is not dried optimally, the valve towards the air
consumer may be opened even when the PDP temperature is too high. In this
case, it will take more time for the desiccant to dry completely.
5.2 Start-up
If the dryer has not been used for more than 3 months, refer to the chapter "Initial start-up". In all other
cases proceed as follows:
1. Cut off the air supply from the compressor towards the dryer by closing the the external inlet valve.
2. Cut off the air supply towards the PDP-sensor.
3. If installed, close the external outlet valve between the dryer unit and the dry air consumer.
4. Slowly open the dryer skid inlet valve.
5. Switch the dryer on.
6. Gradually open the external outlet valve, keeping the pressure inside the dryer above 4.5 bar
(65.3 psi).
7. As required, close the bypass valves of the dryer.
8. Open the air supply towards the PDP-sensor.
Summary of Contents for QHD750
Page 2: ......
Page 4: ......
Page 11: ...Instruction book 9829 2151 14 11 Do not overfill the dryer when replacing desiccant...
Page 14: ...Instruction book 14 9829 2151 14 Back view of QHD750 Front view of QHD900...
Page 15: ...Instruction book 9829 2151 14 15 Back view of QHD900 Front view of QHD1100...
Page 16: ...Instruction book 16 9829 2151 14 Back view of QHD1100 Front view of QHD1370...
Page 17: ...Instruction book 9829 2151 14 17 Back view of QHD1370 Front view of QHD1800...
Page 18: ...Instruction book 18 9829 2151 14 Back view of QHD1800 Front view of QHD2300...
Page 19: ...Instruction book 9829 2151 14 19 Back view of QHD2300 Front view of QHD2800...
Page 20: ...Instruction book 20 9829 2151 14 Back view of QHD2800 Front view of QHD3600...
Page 98: ...Instruction book 98 9829 2151 14 Appendix 1 Service diagram...
Page 99: ......
Page 100: ......
Page 101: ......
Page 102: ......
Page 103: ......
Page 104: ......
Page 105: ......
Page 106: ......
Page 107: ......
Page 108: ......
Page 109: ......
Page 110: ......
Page 111: ......