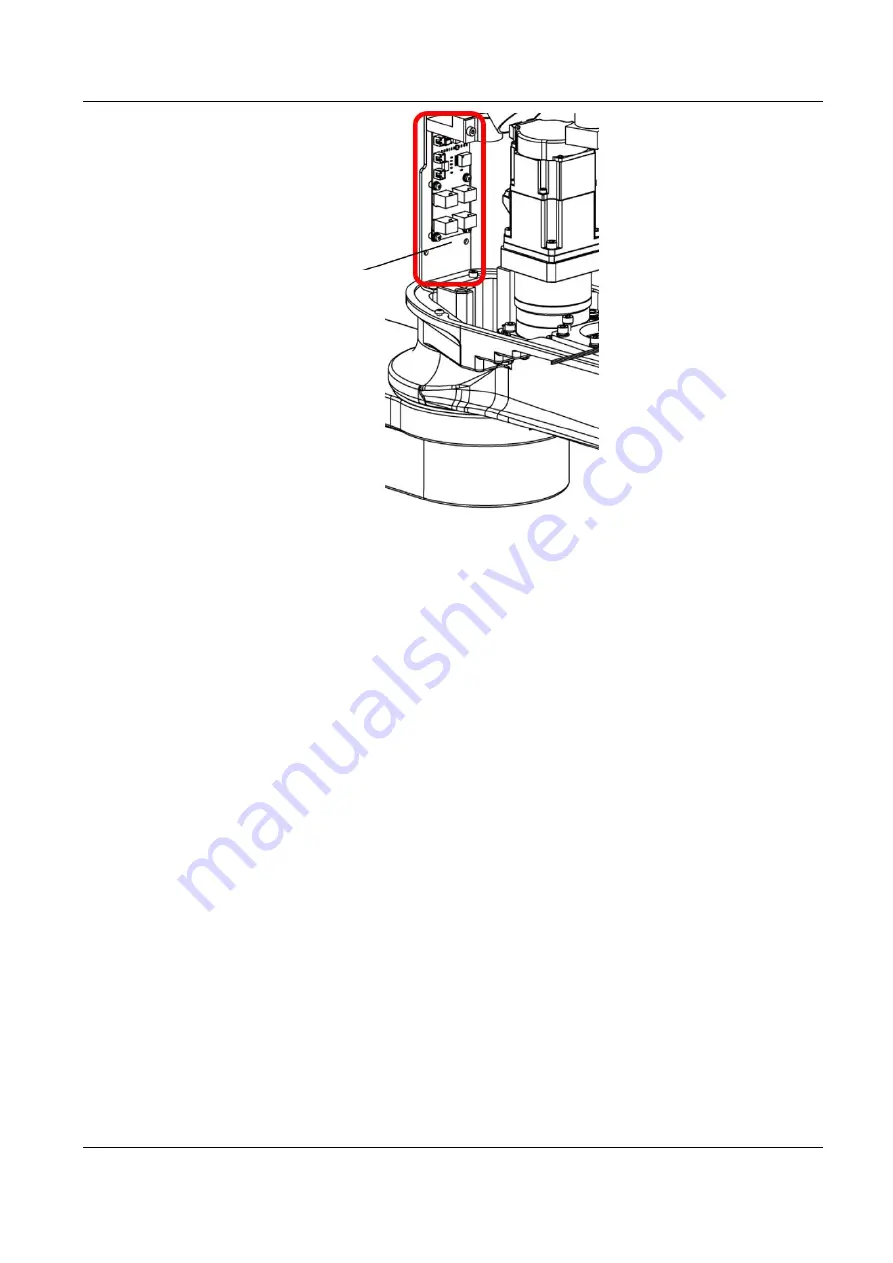
AH20 Robot Maintenance Manual
80
Document Version V1.0.1 (09-21-2022)
Figure 5-26 Brake PCBA of the mechanical arm 2
Step 1
Refer to Section 4.3.1 to remove the screws from the mechanical arm 2
shell of the robot and gently pull out the mechanical arm 2 shell.
Step 2
Unplug all cables connected to the brake PCBA.
Step 3
Use the cross screwdriver to unscrew the fastening screws from the
brake PCBA and remove them, as shown in Figure 5-25.
Brake PCBA