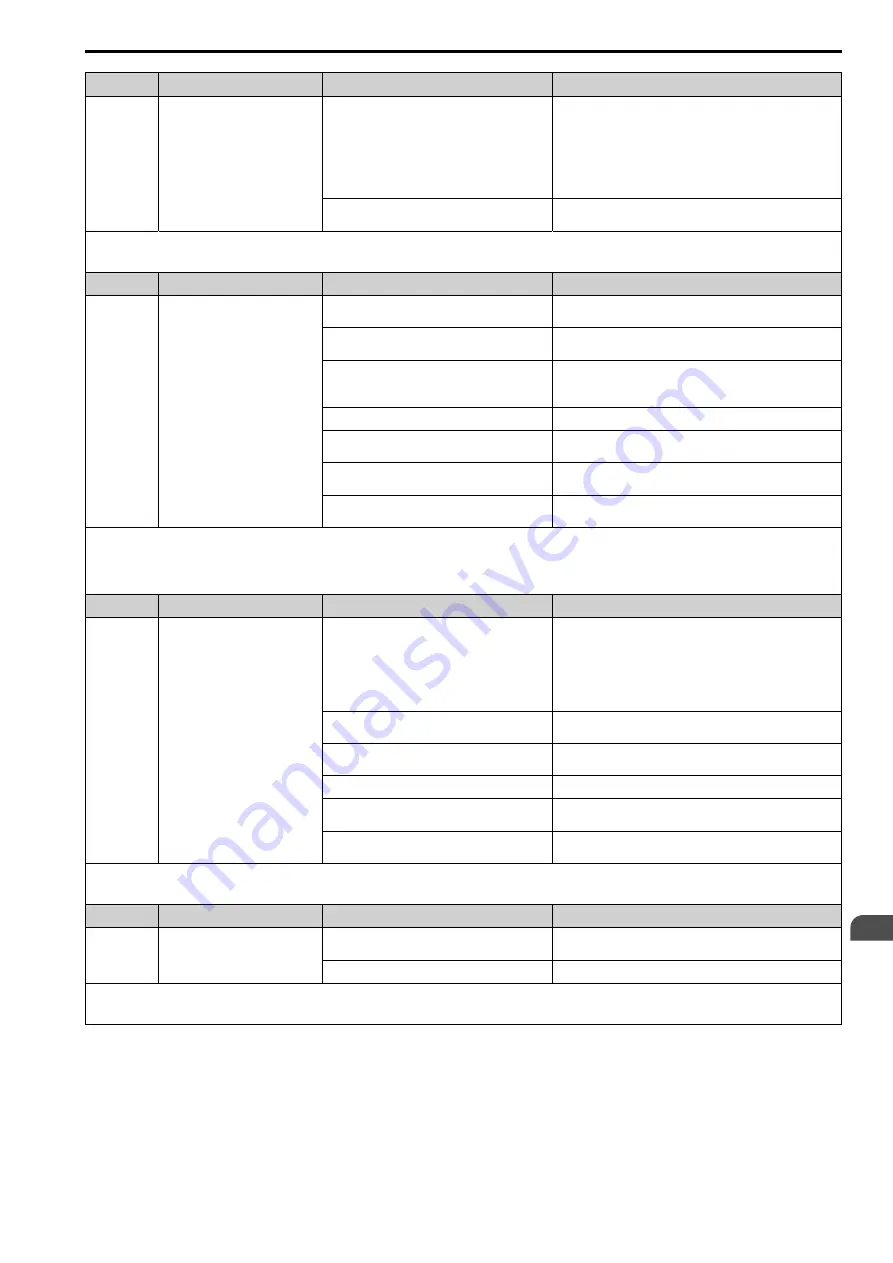
SIEPYEUOQ2A01G AC Drive Q2A Technical Manual
269
Code
Name
Causes
Possible Solutions
The drive is operating a motor with 24 or more
poles at zero speed.
•
Set
F1-46 = 1 [dv2 DetMethodSelection = MechanicalAngle
Detection Method]
.
•
Increase
F1-17 [Dev2 Mode Selection]
.
•
Increase
F1-47 [dv2 DetectionLvl]
.
Note:
If you change the setting of
F1-47
, the sensitivity of detection
for
dv2
can decrease.
The PG option card or the encoder on the motor
side is damaged.
Repair the wiring and re-energize the drive, then replace the PG
option card or the encoder if the problem continues.
Note:
•
The drive detects this error if it does not detect a Z pulse during one motor rotation.
•
Do a Fault Reset to clear the fault.
Code
Name
Causes
Possible Solutions
dv3
Inversion Detection
E5-11 [Enc ZPulse Offset]
is set incorrectly.
Correctly set the value for Δθ to
E5-11
as specified by the values
on the motor nameplate.
There is a new encoder or the motor rotation
direction changed.
Do Z Pulse Offset Tuning.
An external force on the load side rotated the motor.
•
Make sure that the motor is rotating in the correct direction.
•
Find and repair problems on the load side that cause the motor
to rotate from the load side.
Noise interference along the encoder cable.
Correctly ground the shielded wire of the encoder cable.
The encoder cable is disconnected or incorrectly
wired.
Examine for wiring errors or disconnected wires in the encoder
cable, and repair problems.
The setting for
F1-05 [Enc1 Rotat Selection]
is the
opposite of the direction of motor rotation.
Correctly connect the motor wiring for each phase (U, V, W).
The PG option card or the encoder on the motor
side is damaged.
Repair the wiring and re-energize the drive, then replace the PG
option card or the encoder if the problem continues.
Note:
•
The drive detects this error if:
–
the torque reference and acceleration are in opposite directions.
–
the speed reference and actual motor speed are more than 30% different for the number of times set to
F1-18 [Dev3 Mode Selection]
.
•
Do a Fault Reset to clear the fault.
Code
Name
Causes
Possible Solutions
dv4
Inversion Prevention Detection
An external force on the load side moved the motor.
•
Make sure that the motor is rotating in the correct direction.
•
Find and repair problems on the load side that cause the motor
to rotate from the load side.
•
Disable detection of this fault for applications that rotate the
motor from the load side in the opposite direction of the speed
reference. The drive will not detect this fault if
F1-19 = 0
[Dev4 Mode Selection = Disabled]
.
E5-11 [Enc ZPulse Offset]
is set incorrectly.
Correctly set the value for Δθ to
E5-11
as specified by the values
on the motor nameplate.
There is a new encoder or the motor rotation
direction changed.
Do Z Pulse Offset Tuning.
Noise interference along the encoder cable
Correctly ground the shielded wire of the encoder cable.
The encoder cable is disconnected or incorrectly
wired.
Examine for wiring errors or disconnected wires in the encoder
cable, and repair problems.
The PG option card or the encoder on the motor
side is damaged.
Repair the wiring and re-energize the drive, then replace the PG
option card or the encoder if the problem continues.
Note:
•
The drive detects this error if the pulses in the opposite direction of the speed reference are more than the value set in
F1-19
.
•
Do a Fault Reset to clear the fault.
Code
Name
Causes
Possible Solutions
dv7
Polarity Judge Timeout
There is a disconnection in the motor coil winding.
Measure the motor line-to-line resistance and replace the motor if
a coil is disconnected.
The screws on the drive output terminals are loose.
Tighten the terminal screws to the correct tightening torque.
Note:
•
The drive detects this error if it cannot detect polarity in a pre-set length of time.
•
Do a Fault Reset to clear the fault.
Summary of Contents for Q2A
Page 2: ...This Page Intentionally Blank 2 SIEPYEUOQ2A01G AC Drive Q2A Technical Manual...
Page 12: ...12 SIEPYEUOQ2A01G AC Drive Q2A Technical Manual...
Page 18: ...i 2 Legal Information 18 SIEPYEUOQ2A01G AC Drive Q2A Technical Manual...
Page 28: ...1 2 Features and Advantages of Control Methods 28 SIEPYEUOQ2A01G AC Drive Q2A Technical Manual...
Page 64: ...2 9 Installation Methods 64 SIEPYEUOQ2A01G AC Drive Q2A Technical Manual...
Page 166: ...4 9 Test Run Checklist 166 SIEPYEUOQ2A01G AC Drive Q2A Technical Manual...
Page 172: ...5 2 European Standards 172 SIEPYEUOQ2A01G AC Drive Q2A Technical Manual...
Page 173: ...Standards Compliance 5 5 2 European Standards SIEPYEUOQ2A01G AC Drive Q2A Technical Manual 173...
Page 174: ...5 2 European Standards 174 SIEPYEUOQ2A01G AC Drive Q2A Technical Manual...
Page 175: ...Standards Compliance 5 5 2 European Standards SIEPYEUOQ2A01G AC Drive Q2A Technical Manual 175...
Page 176: ...5 2 European Standards 176 SIEPYEUOQ2A01G AC Drive Q2A Technical Manual...
Page 258: ...6 2 Modbus Communications 258 SIEPYEUOQ2A01G AC Drive Q2A Technical Manual...
Page 356: ...8 7 Storage Guidelines 356 SIEPYEUOQ2A01G AC Drive Q2A Technical Manual...
Page 360: ...9 2 Disposal Instructions 360 SIEPYEUOQ2A01G AC Drive Q2A Technical Manual...