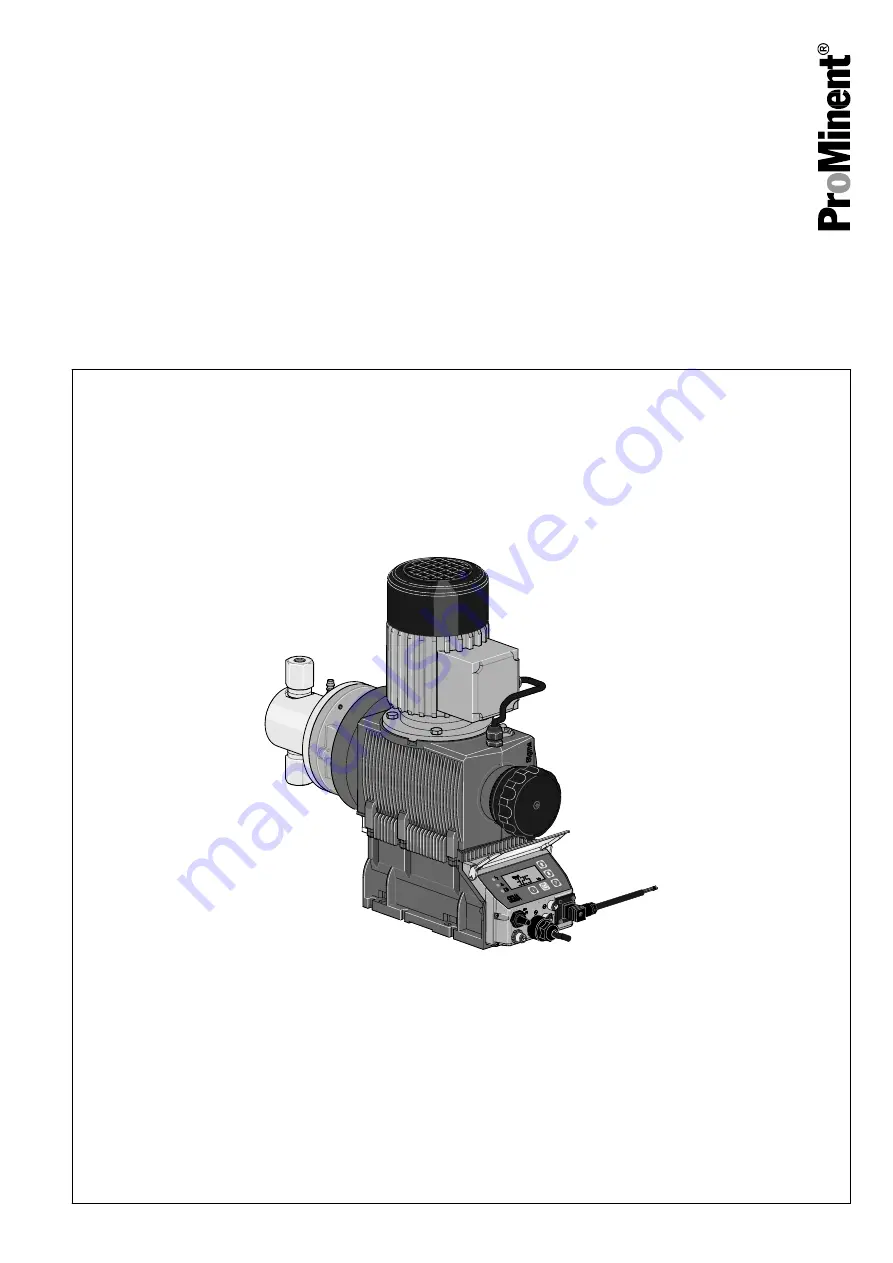
Piston Metering Pump
Sigma/ 2 Control type SCKa
Operating instructions
P_SI_0136_SW
Original operating instructions (2006/42/EC)
Part no. 984860
BA SI 060 11/13 EN
Please carefully read these operating instructions before use! · Do not discard!
The operator shall be liable for any damage caused by installation or operating errors!
Technical changes reserved.