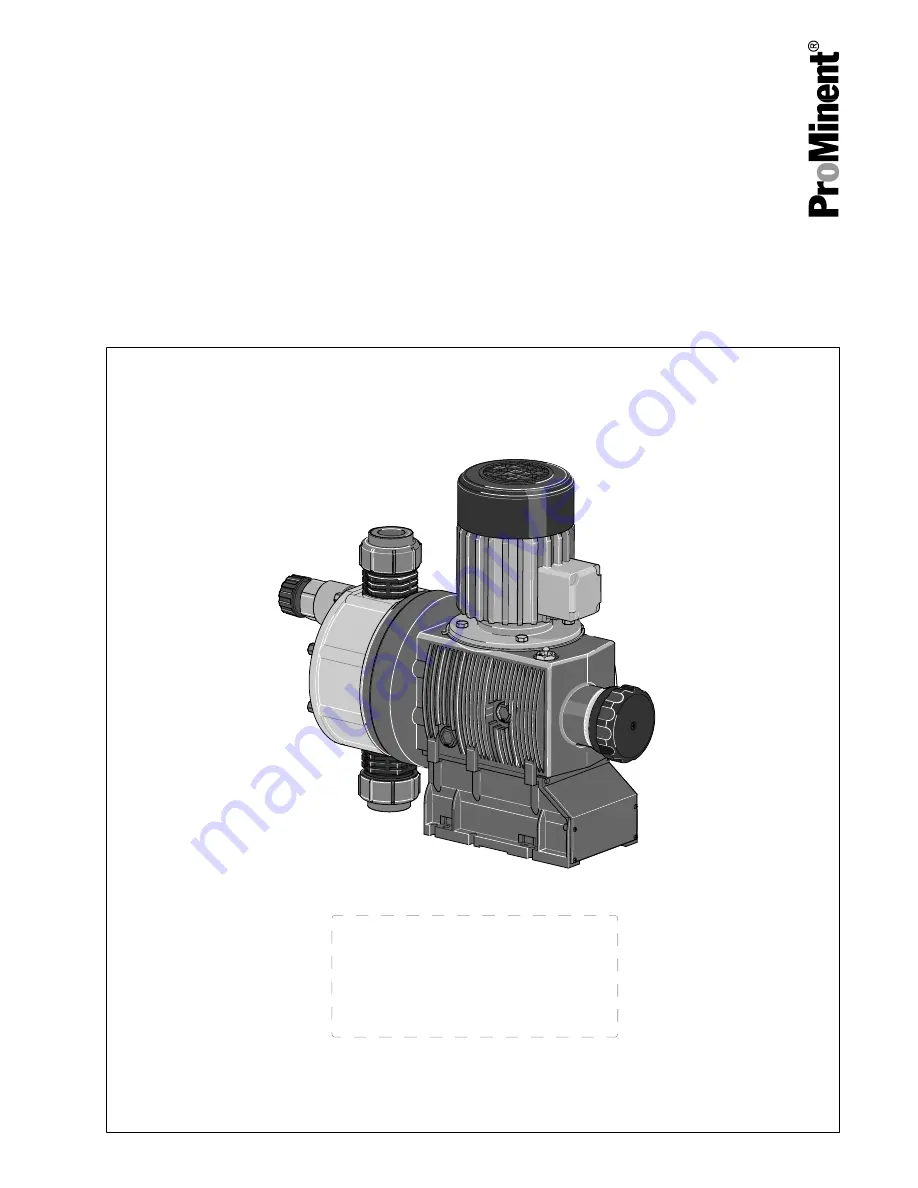
Diaphragm motor-driven metering pump
Sigma/ 3 Basic type S3Ba
Operating instructions
P_SI_0075_SW
EN
Original operating instructions (2006/42/EC)
Part no. 985905
BA SI 089 01/19 EN
Please carefully read these operating instructions before use. · Do not discard.
The operator shall be liable for any damage caused by installation or operating errors.
The latest version of the operating instructions are available on our homepage.