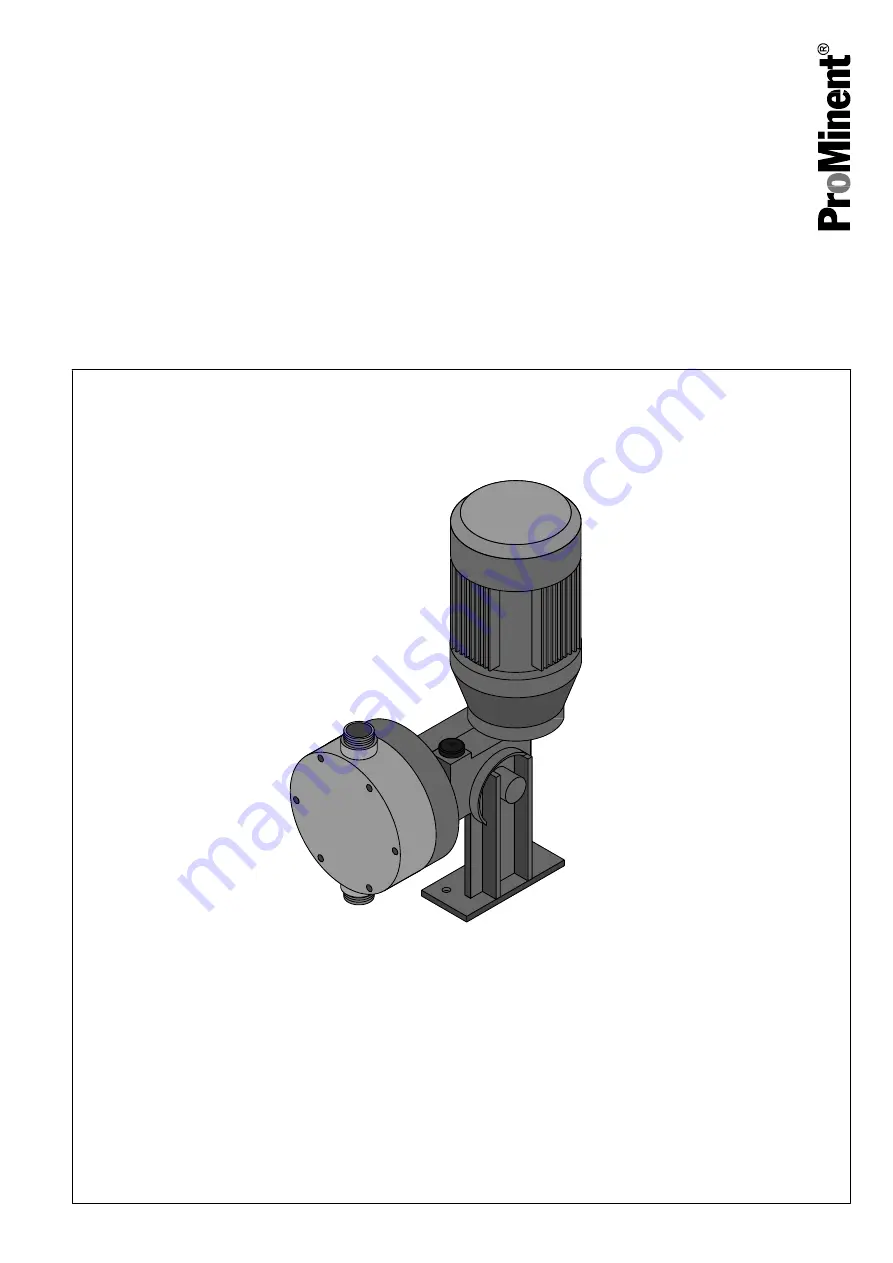
Plasma PSMa
Motorised Diaphragm Metering Pump
Operating Manual
P_PL_0001_SW
Two sets of operating instructions are required for the safe, correct and proper operation of the metering pumps: The
product-specific operating instructions and the "General Operating Instructions ProMinent
®
Motor-Driven Metering Pumps
and Hydraulic Accessories".
Both sets of operating instructions are only valid when read together.
Translation of Original operating instructions (2006/42/EC)
Vers. 10/2009
Please carefully read these operating instructions before use! · Do not discard!
The operator shall be liable for any damage caused by installation or operating errors!
Technical changes reserved.