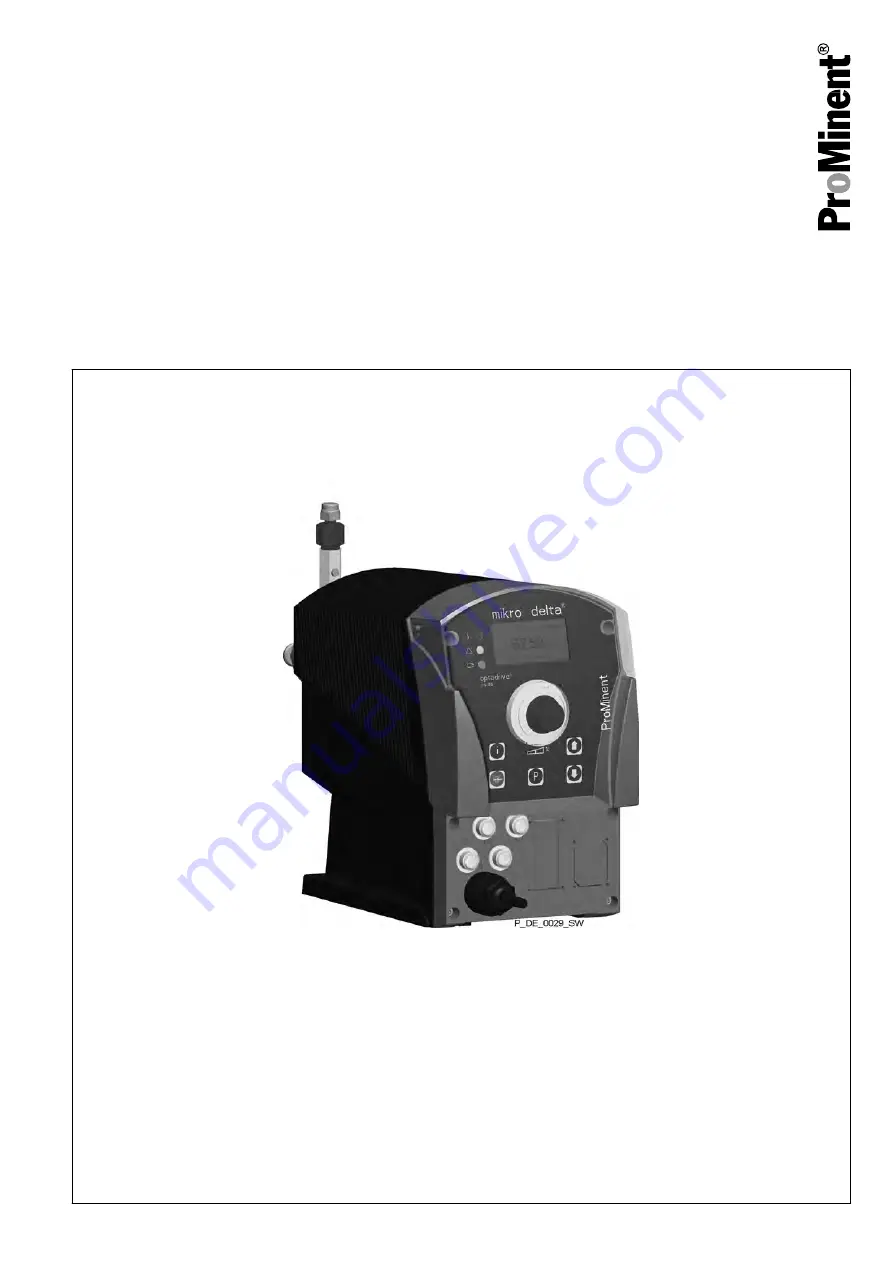
Precision Piston Metering Pump
mikro delta
®
MDLa
Operating instructions
with controlled optoDrive
®
solenoid drive
Original Operating Instructions (2006/42/EC)
Part no. 986160
BA DE 024 08/12 EN
Please carefully read these operating instructions before use! · Do not discard!
The operator shall be liable for any damage caused by installation or operating errors!
Technical changes reserved.
Summary of Contents for mikro delta
Page 59: ...Fig 27 Leakage hole Maintenance 59...
Page 86: ...22 Decontamination declaration Decontamination declaration 86...
Page 88: ...Menu Security Menu Clear Menu Language Operating adjustment overview 88...
Page 93: ...93...
Page 94: ...94...
Page 95: ...95...