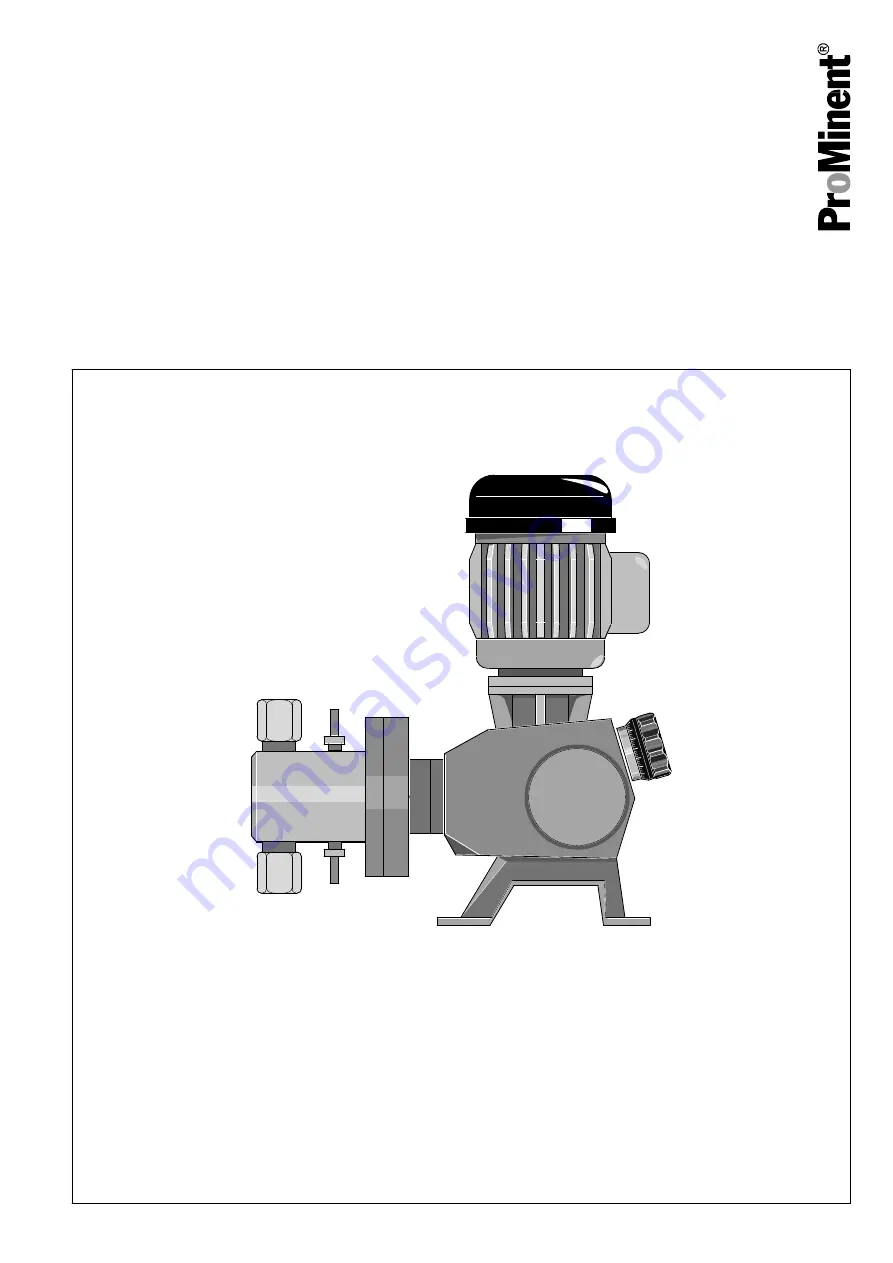
Piston Metering Pump
Meta MTKa
Operating instructions
P_ME_0005_SW
Original operating instructions (2006/42/EC)
Part no. 985036
BA ME 010 02/14 EN
Please carefully read these operating instructions before use. · Do not discard.
The operator shall be liable for any damage caused by installation or operating errors.
The latest version of the operating instructions are available on our homepage.