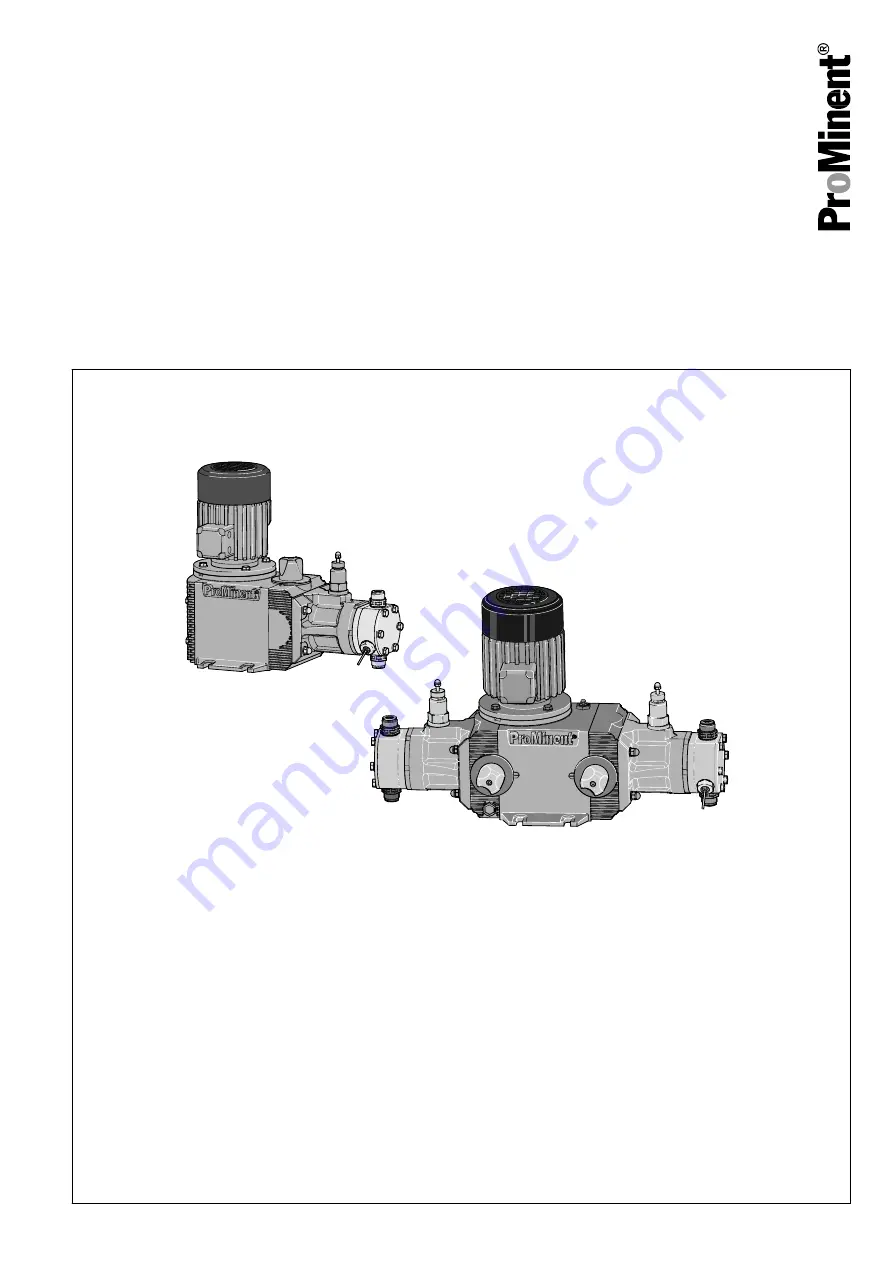
Metering pumps
Hydro/ 2 and Hydro/ 3
Operating instructions
P_HY_0004_SW
EN
Original operating instructions (2006/42/EC)
984721
BA HY 018 05/19 EN
Please carefully read these operating instructions before use. · Do not discard.
The operator shall be liable for any damage caused by installation or operating errors.
The latest version of the operating instructions are available on our homepage.