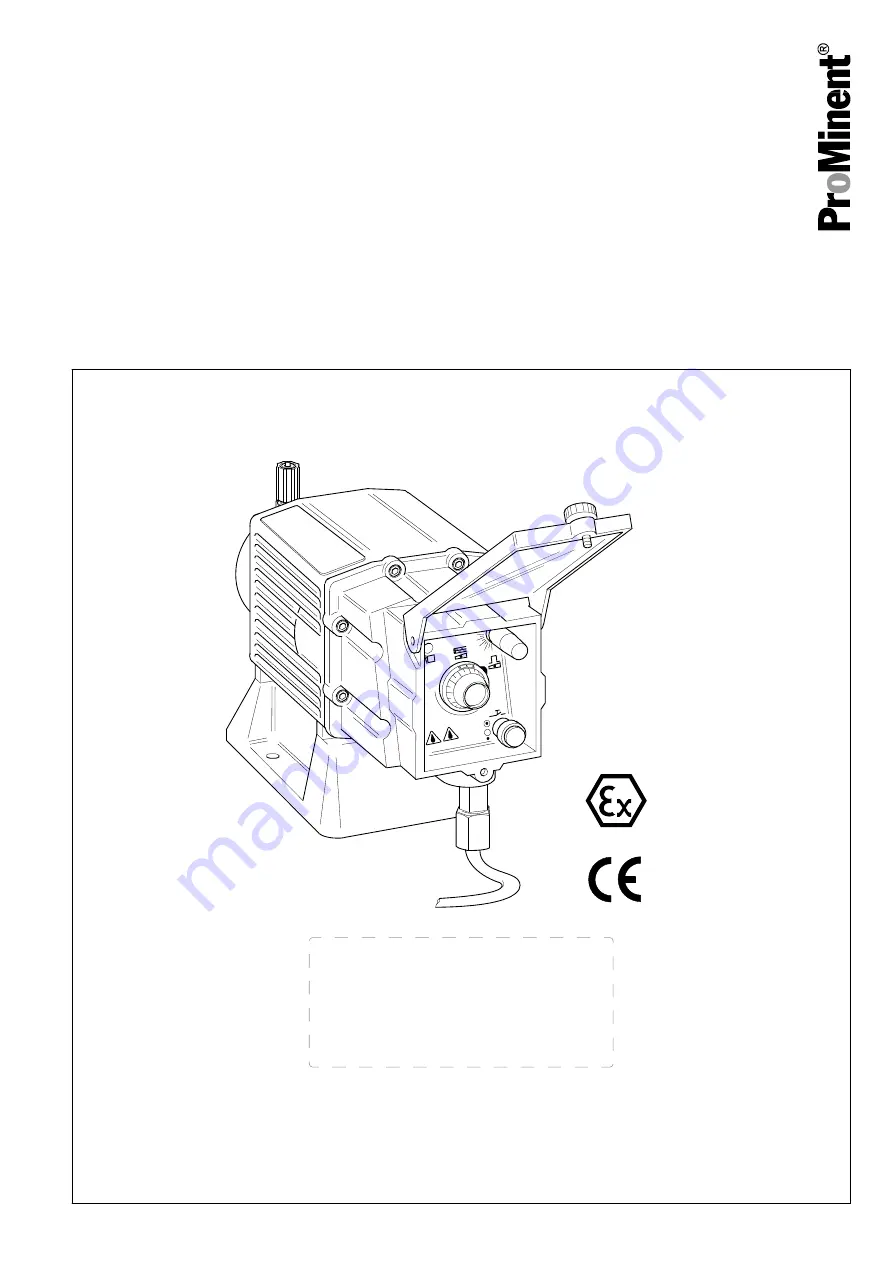
Metering pump
ProMinent EXtronic
®
EXBb
Operating instructions
0158
EN
Original operating instructions (2006/42/EC)
Part No. 987094
BA EX 0 16 09/19 EN
Please carefully read these operating instructions before use. · Do not discard.
The operator shall be liable for any damage caused by installation or operating errors.
The latest version of the operating instructions are available on our homepage.