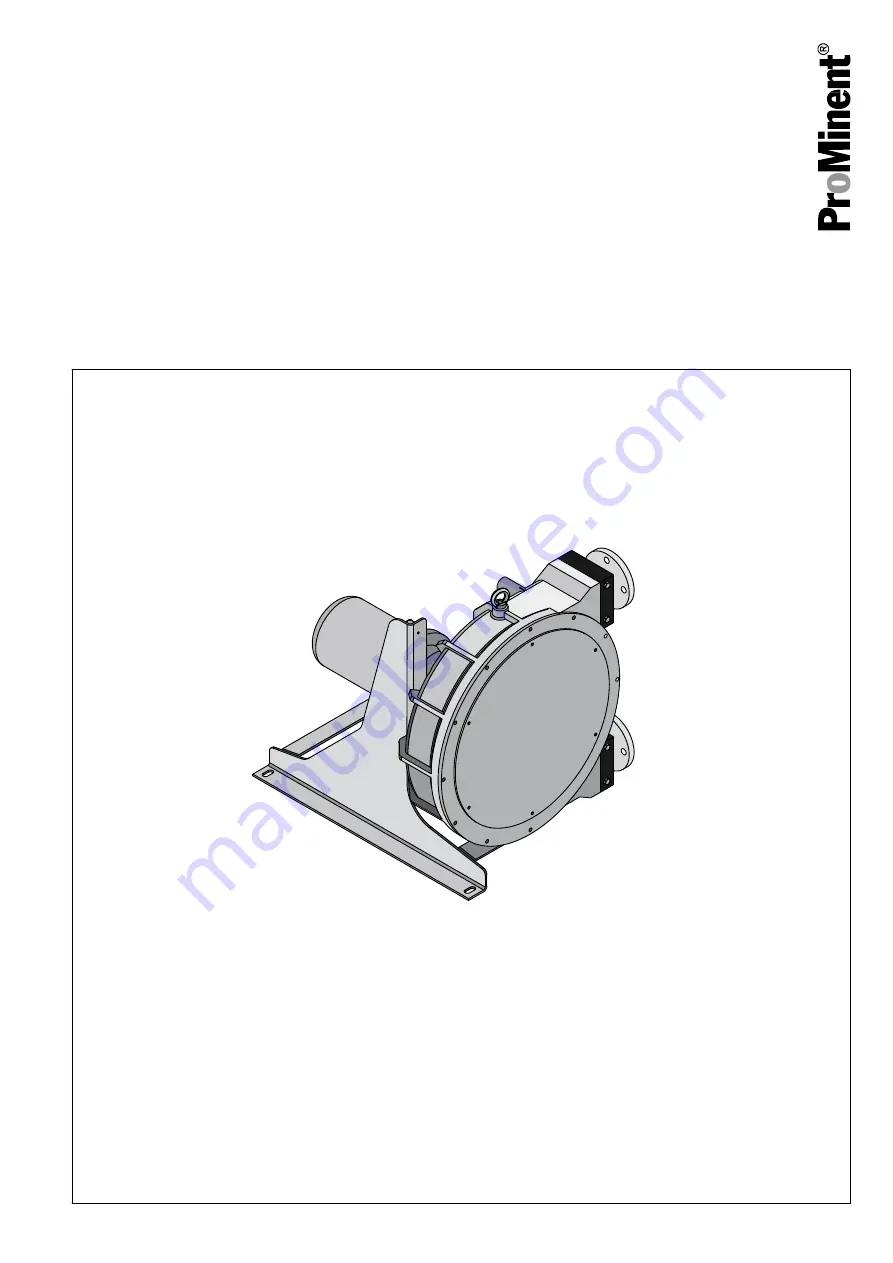
DULCO
®
flex DFCa
Peristaltic Pump
Operating instructions
A0374
EN
Original Operating Instructions (2006/42/EC)
Part no. 986227
BA DX 021 12/15 EN
Please carefully read these operating instructions before use. · Do not discard.
The operator shall be liable for any damage caused by installation or operating errors.
The latest version of the operating instructions are available on our homepage.