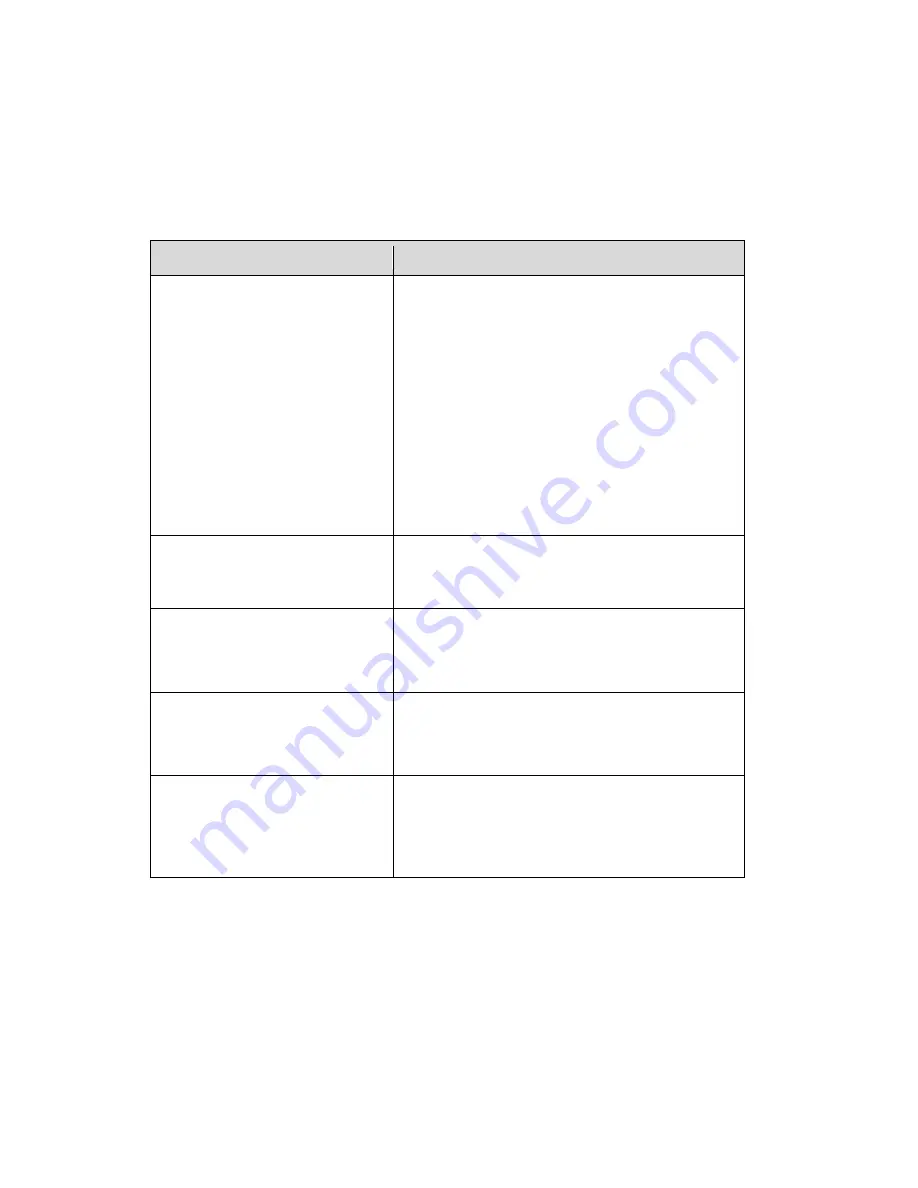
40
14.
Troubleshooting
If you are having problems with the validator, consult Table 5 for a list of symptoms and possible
solutions.
Table 5. Troubleshooting the Validator
Symptom
Solution
The ODV2D-V2 beam does not
come on.
1. Make sure the power/data cable is plugged
into the ODV2D-V2 and the controller board
on the printer.
2. Make sure the validator has not been disabled
in the
ODV2D-V2 > Control > Validator Active
menu. See
“Enab
le
Validator” on page
15.
3. Print a bar code 2D Validation Demo page on
page 33.
4. Call your service representative if the problem
persists.
The ODV2D-V2 beam does not
cover the entire width of the
labels being printed.
There is something wrong with the LED array.
Call your service representative if the problem
persists.
The printer pauses after scanning
each label.
For complex labels with 2-D or several 1-D
barcodes, the printer might be waiting for the
ODV2D-V2 to complete analysis. Try reducing the
print speed to minimize pausing.
Printing less than 10 mil (0.010
inch) x-dimension width bar
codes constantly causes error
messages.
The validator does not recognize x-dimensions
smaller than10 mil. If you must print bar codes
this size, disable the validator to prevent error
reports. See
“Enabl
e
Validator” on page
15.
The printed labels look clean, but
the validator is still reporting an
error message.
The validator glass may be dirty, distorting the
report results. Power down the printer and clean
the glass using Microfiber Glass and Mirror Cloth
and Sight Savers Lens Cleaner Spray or
equivalent.