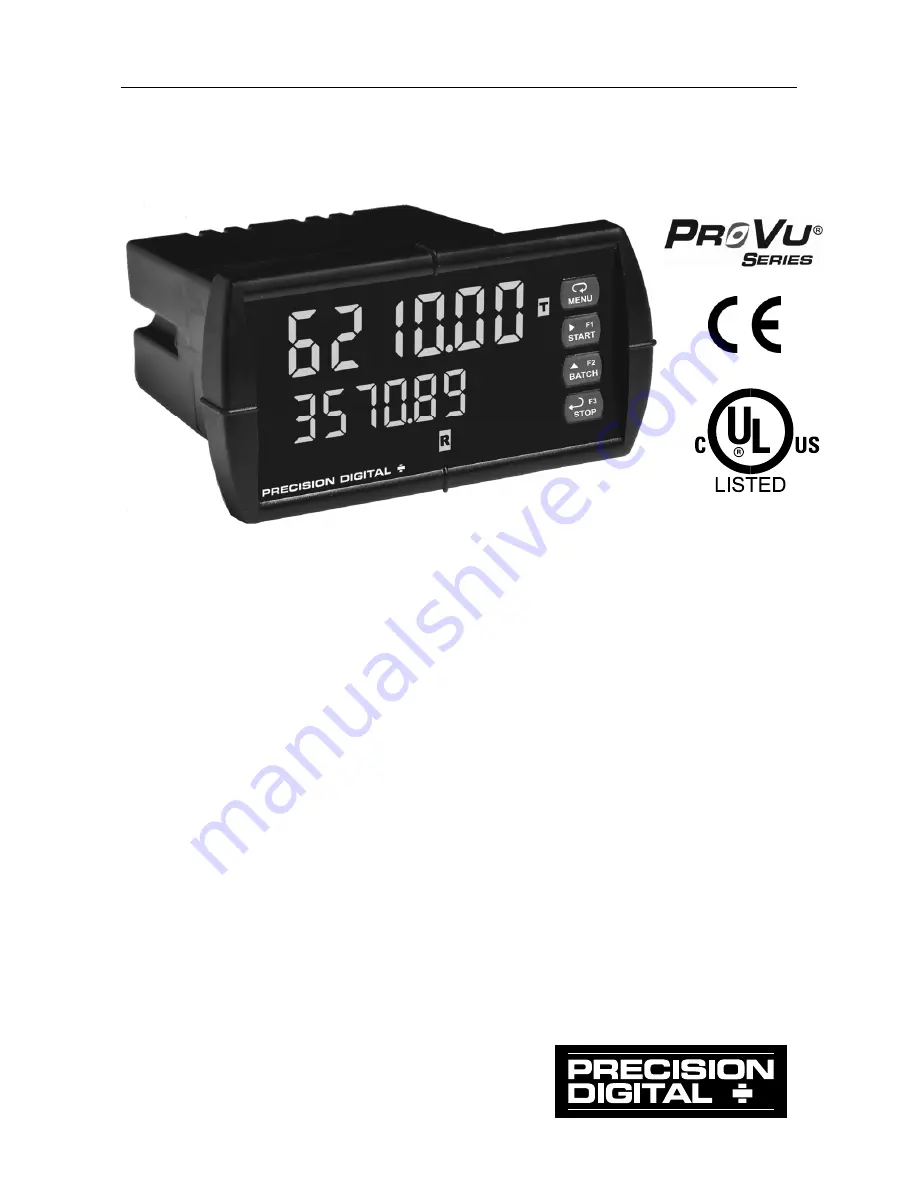
PRECISION DIGITAL CORPORATION
89 October Hill Road • Holliston MA 01746 USA
Tel (800) 343-1001 • Fax (508) 655-8990
www.predig.com
P
RO
V
U
Batch Controllers
PD6210 Analog Input &
PD6310 Pulse Input
PD6210: 0-20 mA, 4-20 mA, 0-5 V, 1-5 V,
10 V Inputs
PD6310: Pulse, Open Collector, NPN, PNP, TTL, Switch
Contact, Sine Wave (Coil), Square Wave Inputs
NEMA 4X, IP65 Front
Start/Pause/Stop, Change Batch with Front Panel Buttons
Single or Multi-Stage Batch Control (Up to 8 Relays)
Automatic
Overrun
Correction
Rate in Units per Second, Minute, Hour, or Day
Automatic or Manual Batch Control
Low or High Flow Alarms
9 Digit Grand Total with Overflow Feature
Count Up or Down with Each Batch
Free
MeterView
®
Pro Software for Operation, Monitoring,
and Programming
Summary of Contents for PROVU PD6210
Page 36: ...Model PD6210 PD6310 Batch Controllers Instruction Manual 36 36 36...
Page 100: ...Model PD6210 PD6310 Batch Controllers Instruction Manual 100 NOTES...
Page 102: ...Model PD6210 PD6310 Batch Controllers Instruction Manual 102...
Page 103: ...Model PD6210 PD6310 Batch Controllers Instruction Manual 103 NOTES...