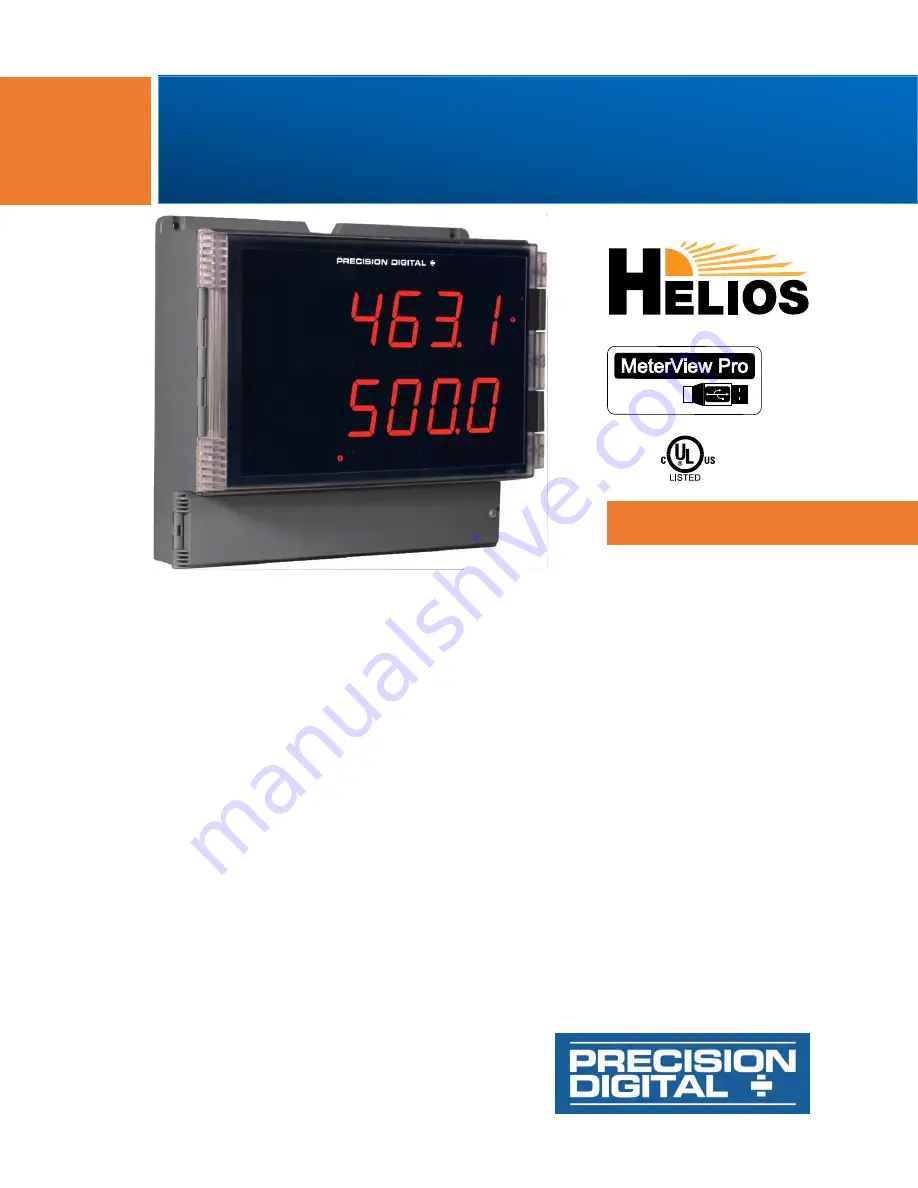
Helios Large Display Pulse Input Batch Controller
Instruction Manual
PD2-6310
Precision Digital Corporation
Batch Controller
•
Large 1.80" Digits
•
Dual-Line 6-Digit Display
•
Readable from up to 100 Feet (30 Meters) Away
•
Superluminous Sunlight Readable Display
•
NEMA 4X, IP65 Rated Field Mountable Enclosure
•
Operating Temperature Range of -40 to 65°C (-40 to 150°F)
•
Single or Multi-Stage Batch Control (up to 4 Relays)
•
Pulse, Open Collector, NPN, PNP, TTL, Switch Contact,
Sine Wave (Coil), Square Wave Inputs
•
Start/Pause/Stop, Change Batch with Front Panel Buttons
•
Automatic Overrun Correction
•
Input Power Options Include 85-265 VAC or 12-24 VDC
•
Isolated 24 VDC Transmitter Power Supply
•
Count Up or Down with Each Batch
•
2 or 4 Isolated 4-20 mA Output Options
•
Onboard USB & RS-485 Serial Communications
•
Modbus
®
RTU Communication Protocol Standard
•
Program the Meter from a PC with onboard USB and MeterView Pro
USB Install
www.
GlobalTestSupply
.com
Find Quality Products Online at: