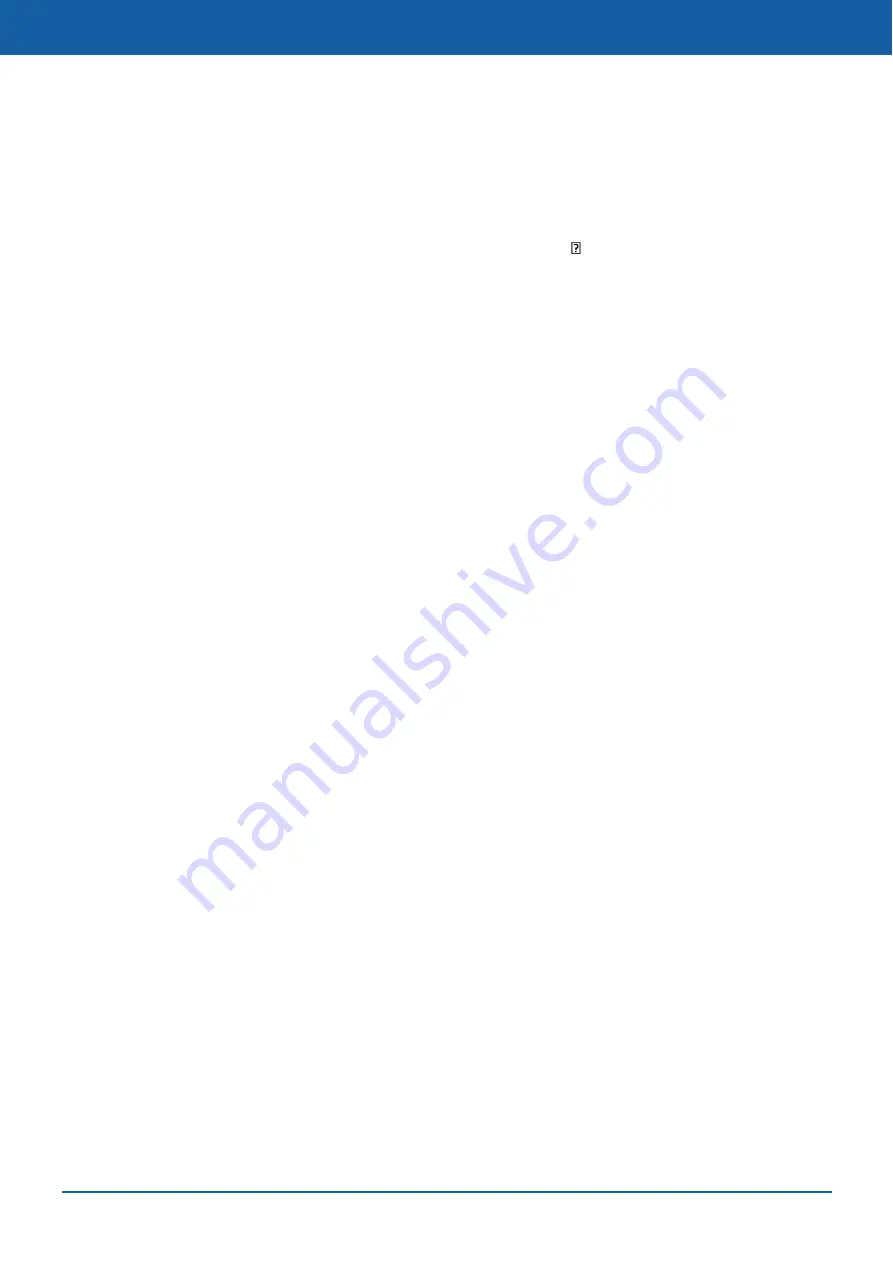
UMSUMS - USER GUIDE
4 of 8
Motion Control Actuators and Frame
Description
This component is principally concerned with the movement of the hydrophone within the measurement
tank. There are four linear motion stages (3 powered, 1 slave). Each linear actuator is based upon a 2mm
pitch ball screw that is driven by a stepping motor. Closed-loop control is provided by a load mounted
linear magnetic encoder giving a read out positional resolution of 1 m. With all stepper motor driven
systems there exists the possibility that the number of steps completed by the actuator will not be the
same as the number steps requested by the drive controller. This generally results in the actuator not
moving as far as expected. When the encoders are activated their output is fed back to the drive
controller. If there is a difference between the distance moved by the actuator, and that initially
requested, the drive controller calculates the necessary correction and automatically moves the drive as
appropriate. The encoder deadband is set by default to 6 µm giving positional accuracy of ±6 µm. As a
safety precaution all drives have two limit switches that can be used to prevent the actuator from moving
beyond particular user-definable positions. These can be used to prevent collision between the
hydrophone and static objects, such as the walls of the tank, or into obstacles placed within the tank.
Axis labelling convention
To prevent confusion when identifying axes, the following conventions are adopted:
•
The Z-axis (in keeping with standard acoustics nomenclature) is the acoustic axis of the
transducer. For vertically mounted systems (transducer firing top down or bottom up) the
Z-axis will be the vertical axis. For horizontally mounted systems, the Z-axis is the longest
horizontal axis of the tanks
•
The X-axis is always defined as the axis which crosses the tank
•
The Y-axis is thus defined as the longitudinal axis of the tank (for vertically mounted
systems) or the vertical axis (for horizontally mounted systems).
All axes adopt the convention that the positive direction is away from the actuator motor.
Two-Rotational Axes Gimbal Mount
Optional rotational mounts are available. See the documentation supplied with your mounts for more
information.
Axis Labelling Convention
Once X and Y axis have been identified the two rotational axes on the gimbal are simply identified as
rotation about the X-axis (Abt_X) and about the Y-axis (Abt_Y).
Stepper Motor Drive Control Unit
This unit contains the stepper motor drive controllers and their associated power supplies. It also contains
the temperature monitoring system. Each motion actuator has its own dedicated drive controller within
the cabinet. These controllers deal with all aspects of motion control. In addition to supplying power to
the stepper motors, they also implement the actions required by the limit or emergency stop switches, as
well as administering position maintenance instructions when the system is used with drive encoders. The
drive control unit is mains powered, and is fitted with a door cut-out switch that interrupts the mains