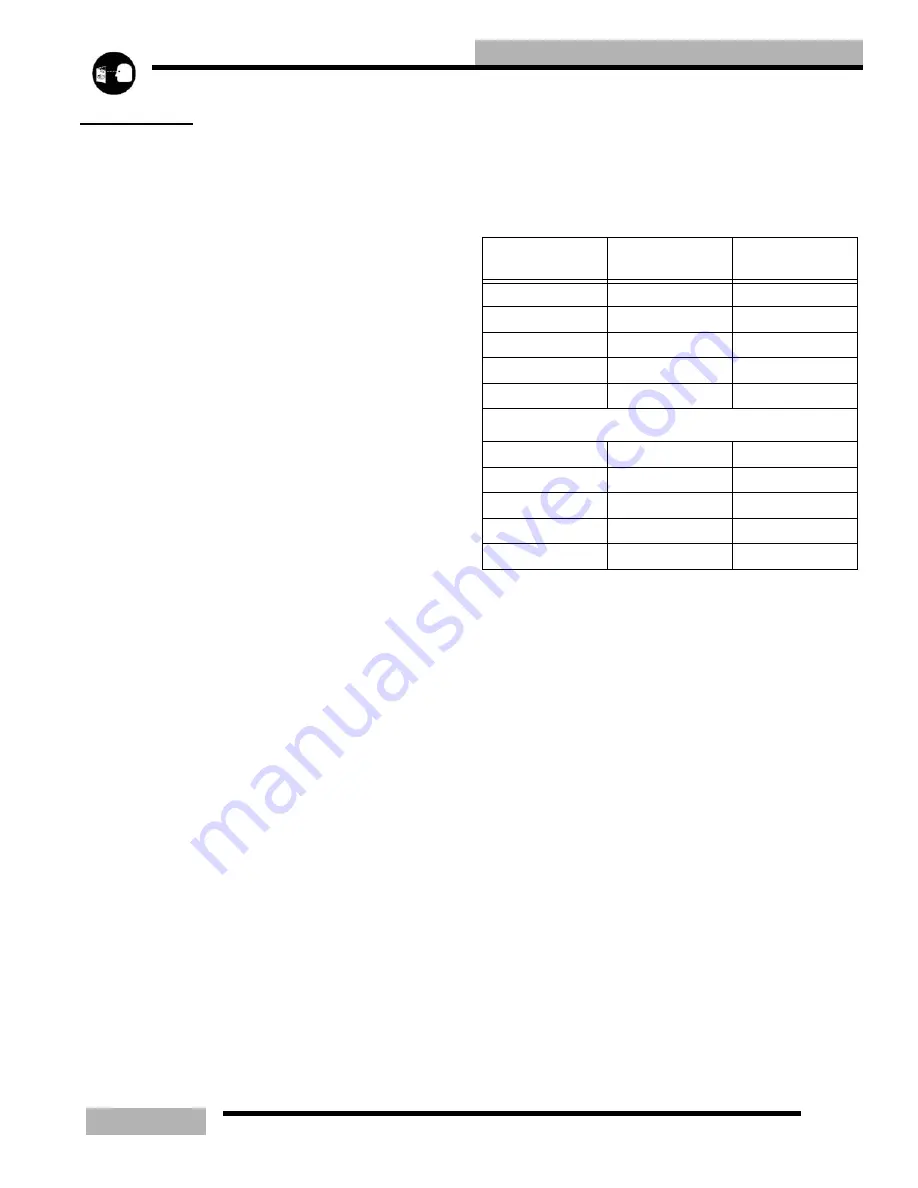
13.5
ELECTRICAL
BATTERY
PREPARING A NEW BATTERY FOR
SERVICE
To ensure maximum service life and performance from a
battery, it must have proper initial servicing. To service a new
battery, the following steps must be taken.
NOTE: Do not service the battery unless it will be
put into regular service within 30 days.
1.
Remove vent plug from vent fitting.
2.
Fill battery with electrolyte to the upper level marks on the
case.
3.
Set battery aside and allow it to cool and stabilize for 30
minutes.
4.
Add electrolyte to bring the level back to the upper level
mark on the case.
NOTE: This is the last time that electrolyte should
be added. If the level becomes low after this point,
add only distilled water.
5.
Charge battery at 1/10 of its amp/hour rating. Example:1/
10 of 9 amp battery =.9 amps, 1/10 of 14 amp battery = 1.4
amps, 1/10 of 18 amp battery = 1.8 amps (recommended
charging rates).
6.
Check specific gravity of each cell with a hydrometer to
ensure each has a reading of 1.270 or higher.
BATTERY TESTING
There are three easy tests which can determine battery
condition. Whenever the complaint is related to either the
starting or charging systems, the battery should be checked
first. Lead-acid batteries should be kept at or as near full
charge as possible. If the battery is stored or used in a partially
charged condition, hard crystal sulfation will form on the
plates, reducing their efficiency and possibly ruining the
battery.
OPEN CIRCUIT VOLTAGE TESTING (OCV)
Battery voltage should be checked with a digital multitester.
Readings of 12.6v or less require further battery testing and
charging.
SPECIFIC GRAVITY TEST
A tool such as the battery hydrometer (PN 2870836) can be
used to measure electrolyte strength or specific gravity. As the
battery goes through the charge/discharge cycle, the
electrolyte goes from a heavy, more acidic state at full charge
to a light, more water state when discharged. The hydrometer
can measure state of charge and differences between cells in a
multi-cell battery. Readings of 1.270 or greater should be
observed in a fully charged battery. Differences of more
than.025 between the lowest and highest cell readings indicate
a need to replace the battery.
LOAD TEST
NOTE: This test can only be performed on machines
equipped with electric start. This test cannot be
performed if the engine or starting system is not
working properly.
A battery may indicate a fully charge condition on the OCV
test and the specific gravity test, but still not have the storage
capacity necessary to properly function in the electrical
system. For this reason, a battery capacity or load test should
be conducted whenever poor battery performance is
encountered.
To perform the test, hook a multitester to the battery in the
same manner as in the OCV test. The reading should be 12.6
volts or greater. Engage the electric starter and view the
registered battery voltage while cranking the engine. Continue
the test for 15 seconds. During this cranking period, the
observed voltage should not drop below 9.5 volts. If the
beginning voltage is 12.6 or higher and the cranking voltage
drops below 9.5 volts during the test, replace the battery.
REFILLING A LOW BATTERY
The normal charge/discharge cycle of a battery causes the cells
to give off gases. These gases, hydrogen and oxygen, are the
Table 13-2: Battery Voltage
STATE OF CHARGE
CONVENTIONAL
LEAD-ACID
YUMACRON TYPE
100% CHARGED
12.60v
12.70v
75% CHARGED
12.40v
12.50v
50% CHARGED
12.10v
12.20v
25% CHARGED
11.90v
12.00v
0% CHARGED
< 11.80v
< 11.90v
Battery voltage per cell
100% CHARGED
1.265v
1.275v
75% CHARGED
1.210v
1.225v
50% CHARGED
1.160v
1.175v
25% CHARGED
1.120v
1.135v
0% CHARGED
< 1.100v
< 1.115v
Summary of Contents for SUPERSPORT 2006
Page 48: ...NOTES SPECIFICATIONS 1 48...
Page 55: ...2 7 GENERAL SAE TAP DRILL SIZES METRIC TAP DRILL SIZES DECMIAL EQUIVALENTS...
Page 60: ...2 12 GENERAL SPECIAL TOOLS...
Page 61: ...2 13 GENERAL...
Page 62: ...2 14 GENERAL...
Page 106: ...4 18 CARBURETION...
Page 139: ...6 27 ENGINE 340 550 ENGINE REBUILDING 10 11 3 4 12 13 5 2 14 1 16 15 16 9 17 6 7 8...
Page 156: ...7 12 CLUTCHING 1 1 2 3 4 5 6 7 18 17 10 8 9 13 12 11 15 16 14...
Page 192: ...8 20 FINAL DRIVE...
Page 200: ...10 2 FRONT SUSPENSION STEERING FUSION IQ RMK 600 RMK Fusion 14 78...
Page 201: ...10 3 FRONT SUSPENSION STEERING EDGE RMK Apply Polaris All Season Grease to all zerks...
Page 202: ...10 4 FRONT SUSPENSION STEERING 42 5 EDGE Apply Polaris All Season Grease to all zerks...
Page 203: ...10 5 FRONT SUSPENSION STEERING WIDETRAK Apply Polaris All Season Grease to all zerks...
Page 244: ...11 28 REAR SUSPENSION...
Page 256: ...12 12 CHASSIS HOOD...
Page 282: ...13 26 ELECTRICAL...
Page 288: ...13 32 ELECTRICAL...
Page 289: ...14 1 WIRE DIAGRAM 2006 600 FUSION HO HOOD...
Page 290: ...14 2 WIRE DIAGRAM 2006 HO RMK HOOD...
Page 291: ...14 3 WIRE DIAGRAM 600 HO FUSION RMK CHASSIS...
Page 292: ...14 4 WIRE DIAGRAM 600 HO FUSION RMK CHASSIS CALL OUTS...
Page 293: ...14 5 WIRE DIAGRAM 700 900 ENGINE...
Page 294: ...14 6 WIRE DIAGRAM 700 900 ENGINE AND ENGINE CALL OUTS...
Page 295: ...14 7 WIRE DIAGRAM 700 900 CHASSIS...
Page 297: ...14 9 WIRE DIAGRAM 340 550 FUJI FAN ENGINE CHASSIS...
Page 298: ...14 10 WIRE DIAGRAM 500 FUJI ENGINE CHASSIS...
Page 299: ...14 11 WIRE DIAGRAM 500 600 IBERTY ENGINE CHASSIS...