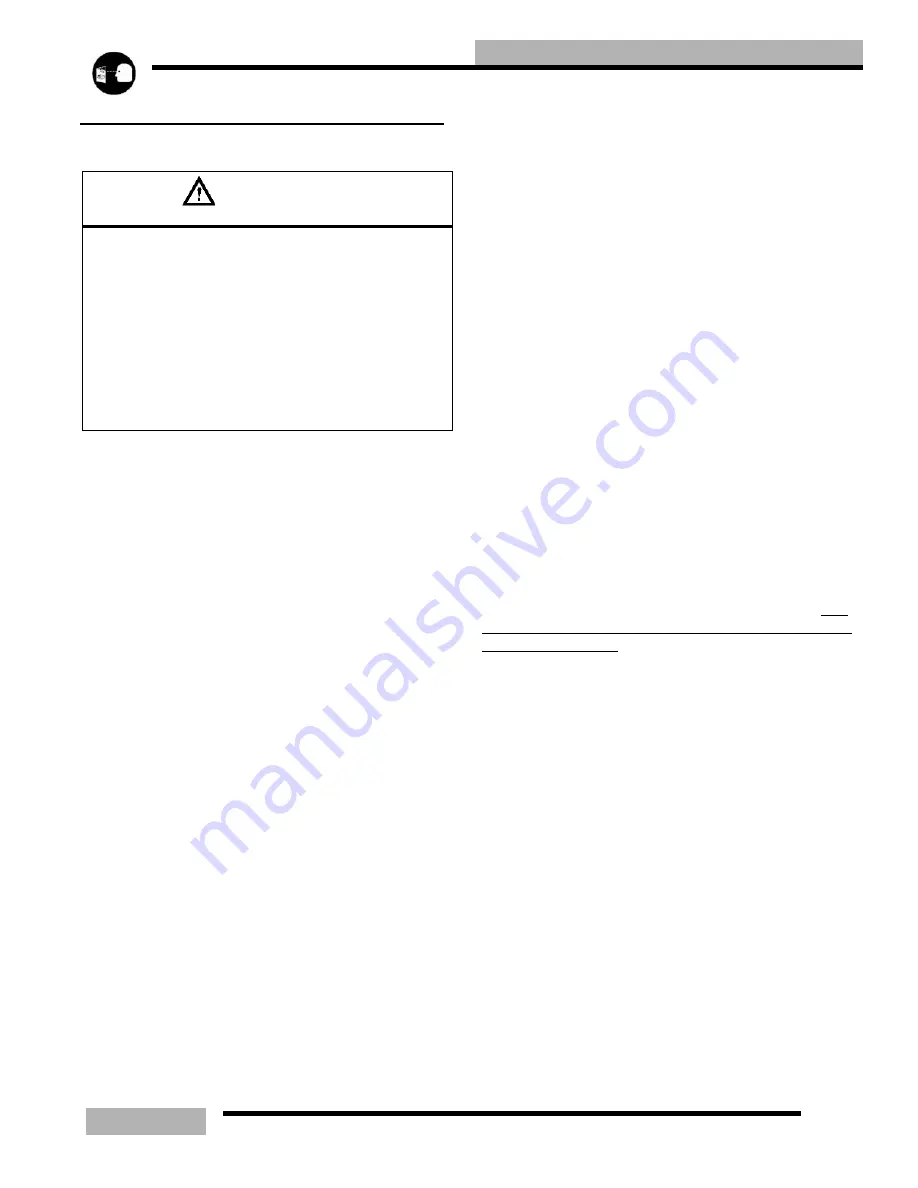
7.7
CLUTCHING
DRIVE SYSTEM TERMINOLOGY
SYSTEM OVERVIEW
The Polaris drive system is a centrifugally actuated variable
speed belt drive unit. The drive clutch, driven clutch, and belt
make up the torque converter system. Each clutch comes from
the factory with the proper internal components installed for
its specific engine model. Therefore, modifications or
variations of components at random are never recommended.
Proper clutch setup and adjustments of existing components
must be the primary objective in clutch operation diagnosis.
DRIVE SPRING
The drive spring opposes the shift force generated by the
clutch weights, and determines the neutral RPM, engagement
RPM, and wether the engine RPM remains flat, rises, or falls
during shift out. When changing only the drive spring,
installing a spring with a lower pre-load rate will result in a
lower engagement RPM speed, while installing a spring with a
higher pre-load rate will result in a higher engagement RPM.
CLUTCH WEIGHT
The clutch weights generate centrifugal force as the drive
clutch rotates. The force generated changes in relation to the
engine RPM and with specified weight of each clutch weight.
When changing only the clutch weights, a lighter weight will
result in a higher engagement RPM, lower shifting force, and
higher shift out RPM. Installing heavier weights has the
opposite effect
NEUTRAL SPEED
Engine RPM when the force generated by the clutch weights is
less than the pre-load force generated by the drive spring. In
this mode, the drive clutch is disengaged.
ENGAGEMENT RPM
Engine RPM when the force generated by the clutch weights
overcomes the drive spring pre-load force and the moveable
sheave begins to close or “pinch" the drive belt. The
engagement mode continues until no more belt slippage occurs
in the drive clutch. Once 100% belt engagement is achieved,
the sled will accelerate along the low ratio line until the drive
clutch up shift force overcomes the opposing shift force
generated by the driven clutch.
SHIFT OUT OVERREV
Engine RPM that spikes above the desired operating RPM
speed. The shift out RPM should come down to the desired
operating RPM, but never below, after the driven clutch begins
to open.
SHIFT OUT RPM
Engine RPM at which the up shift force generated by the drive
clutch overcomes the shift force within the driven clutch. In
this mode, the drive clutch will move the belt outwards, and
the driven clutch will allow the drive belt to be pulled down
into the sheaves.
During WOT operation, the shift out RPM can be seen as the
maximum, sustained RPM displayed on the tachometer. The
shift out RPM should be the same RPM as the recommended
engine operating RPM. If the shift out RPM is above the
recommended engine operating RPM, install heavier drive
clutch weights. If the shift out RPM is below the
recommended engine operating RPM, install lighter drive
clutch weights.
The shift out RPM should remain constant during both the
upshift and back shift modes.
DRIVEN SPRING
A compression spring (Team driven clutch) or torsional spring
(Polaris P-85 driven clutch) works in conjunction with the
helix, and controls the shift rate of the driven clutch. The
spring must provide enough side pressure to grip the belt and
prevent slippage during initial acceleration. A higher spring
rate will provide more side pressure and quicker back shifting
but decreases drive system efficiency. If too much spring
tension exists, the driven clutch will exert too much force on
the belt and can cause premature belt failure.
CAUTION
All clutch maintenance repairs must be performed only
by an authorized Polaris service technician who has at-
tended a Polaris sponsored service training seminar
and understands the proper procedures as outlined in
this manual. Because of the critical nature and preci-
sion balance incorporated into the drive clutch, it is ab-
solutely essential that no attempt at clutch disassembly
and/or repair be made without factory authorized spe-
cial tools and service procedures. Any unauthorized
modifications to clutches, such as adding or removing
weights, will void the warranty
.
Summary of Contents for SUPERSPORT 2006
Page 48: ...NOTES SPECIFICATIONS 1 48...
Page 55: ...2 7 GENERAL SAE TAP DRILL SIZES METRIC TAP DRILL SIZES DECMIAL EQUIVALENTS...
Page 60: ...2 12 GENERAL SPECIAL TOOLS...
Page 61: ...2 13 GENERAL...
Page 62: ...2 14 GENERAL...
Page 106: ...4 18 CARBURETION...
Page 139: ...6 27 ENGINE 340 550 ENGINE REBUILDING 10 11 3 4 12 13 5 2 14 1 16 15 16 9 17 6 7 8...
Page 156: ...7 12 CLUTCHING 1 1 2 3 4 5 6 7 18 17 10 8 9 13 12 11 15 16 14...
Page 192: ...8 20 FINAL DRIVE...
Page 200: ...10 2 FRONT SUSPENSION STEERING FUSION IQ RMK 600 RMK Fusion 14 78...
Page 201: ...10 3 FRONT SUSPENSION STEERING EDGE RMK Apply Polaris All Season Grease to all zerks...
Page 202: ...10 4 FRONT SUSPENSION STEERING 42 5 EDGE Apply Polaris All Season Grease to all zerks...
Page 203: ...10 5 FRONT SUSPENSION STEERING WIDETRAK Apply Polaris All Season Grease to all zerks...
Page 244: ...11 28 REAR SUSPENSION...
Page 256: ...12 12 CHASSIS HOOD...
Page 282: ...13 26 ELECTRICAL...
Page 288: ...13 32 ELECTRICAL...
Page 289: ...14 1 WIRE DIAGRAM 2006 600 FUSION HO HOOD...
Page 290: ...14 2 WIRE DIAGRAM 2006 HO RMK HOOD...
Page 291: ...14 3 WIRE DIAGRAM 600 HO FUSION RMK CHASSIS...
Page 292: ...14 4 WIRE DIAGRAM 600 HO FUSION RMK CHASSIS CALL OUTS...
Page 293: ...14 5 WIRE DIAGRAM 700 900 ENGINE...
Page 294: ...14 6 WIRE DIAGRAM 700 900 ENGINE AND ENGINE CALL OUTS...
Page 295: ...14 7 WIRE DIAGRAM 700 900 CHASSIS...
Page 297: ...14 9 WIRE DIAGRAM 340 550 FUJI FAN ENGINE CHASSIS...
Page 298: ...14 10 WIRE DIAGRAM 500 FUJI ENGINE CHASSIS...
Page 299: ...14 11 WIRE DIAGRAM 500 600 IBERTY ENGINE CHASSIS...