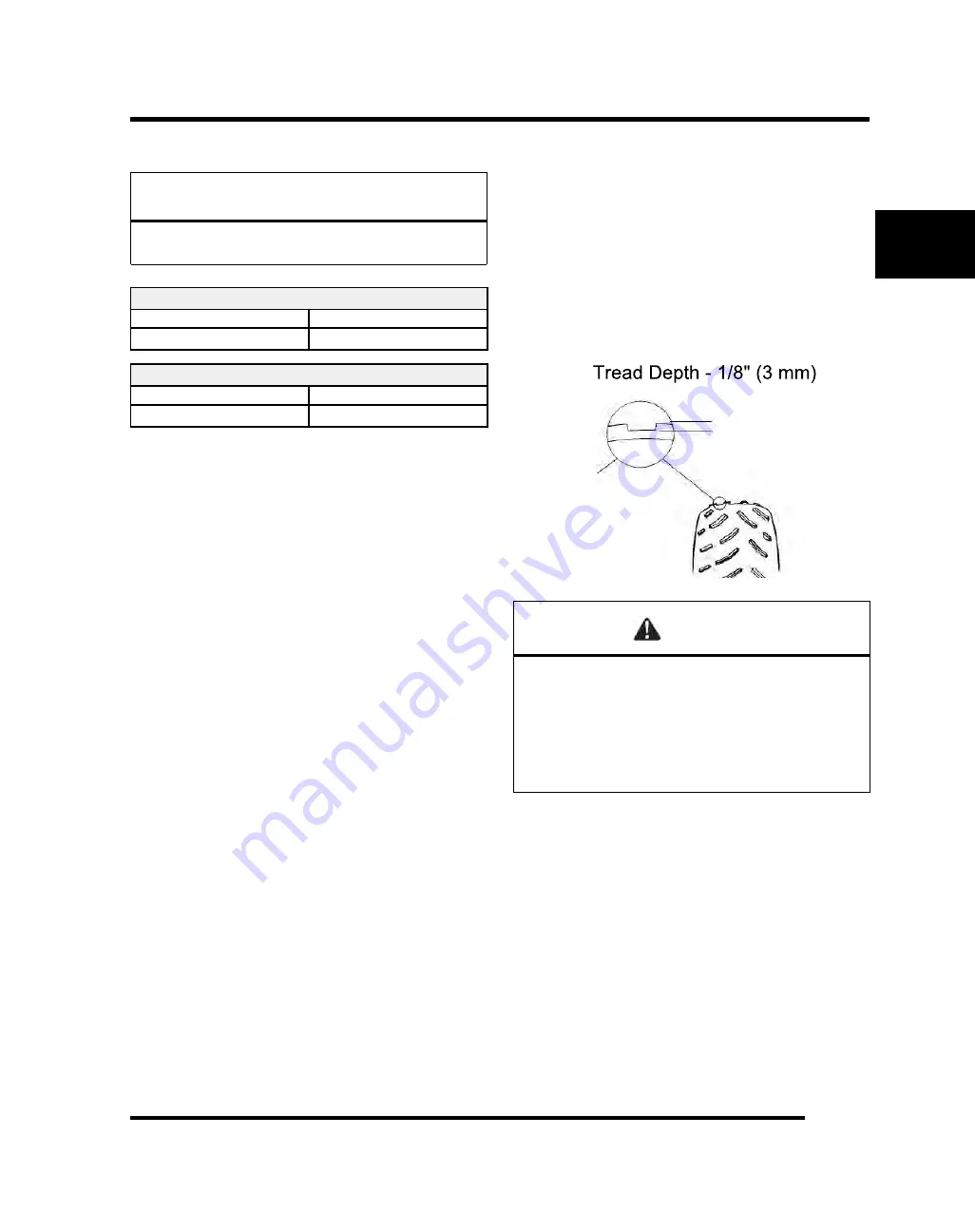
2
2.39
9924864 - 2012-2014 SPORTSMAN 800 / 6X6
© Copyright 2013 Polaris Sales Inc.
Tire Pressure
CAUTION
Maintain proper tire pressure. Refer to the warning tire
pressure decal applied to the vehicle.
TIRE PRESSURE INSPECTION (PSI - COLD) 4X4
Front
Rear
5 (34.5 Kpa)
5 (34.5 Kpa)
TIRE PRESSURE INSPECTION (PSI - COLD) 6X6
Front
Rear
7 (48.25 Kpa)
10 (69 Kpa)
Tire Inspection
• Improper
tire
inflation
may
affect
ATV
maneuverability.
• When
replacing
a
tire
always
use
original
equipment size and type.
• The use of non-standard size or type tires may
affect ATV handling.
Tire Tread Depth
Always replace tires when tread depth is worn to 1/8, (3
mm) or less.
WARNING
Operating an ATV with worn tires will increase the
possibility of the vehicle skidding and possible loss of
control.
Worn tires can cause an accident.
Always replace tires when the tread depth measures 1/
8inch (.3 cm) or less.
MAINTENANCE
Summary of Contents for Sportsman 800 EFI 4x4 2012
Page 4: ......
Page 6: ......
Page 60: ...2 40 9924864 2012 2014 SPORTSMAN 800 6X6 Copyright 2013 Polaris Sales Inc NOTES MAINTENANCE ...
Page 134: ...3 74 9924864 2012 2014 SPORTSMAN 800 6X6 Copyright 2013 Polaris Sales Inc NOTES ENGINE ...
Page 266: ...6 50 9924864 2012 2014 SPORTSMAN 800 6X6 Copyright 2013 Polaris Sales Inc NOTES CLUTCHING ...
Page 384: ...8 44 9924864 2012 2014 SPORTSMAN 800 6X6 Copyright 2013 Polaris Sales Inc NOTES TRANSMISSION ...
Page 482: ...Located By Battery 2012 2014 SPORTSMAN 800 EFI PAGE 1 OF 2 ...
Page 483: ...2012 2014 SPORTSMAN 800 EFI PAGE 2 OF 2 ...
Page 484: ...Located By Battery 2012 2014 SPORTSMAN 800 EFI 6X6 PAGE 1 OF 2 ...
Page 485: ...2012 2014 SPORTSMAN 800 EFI 6X6 PAGE 2 OF 2 ...