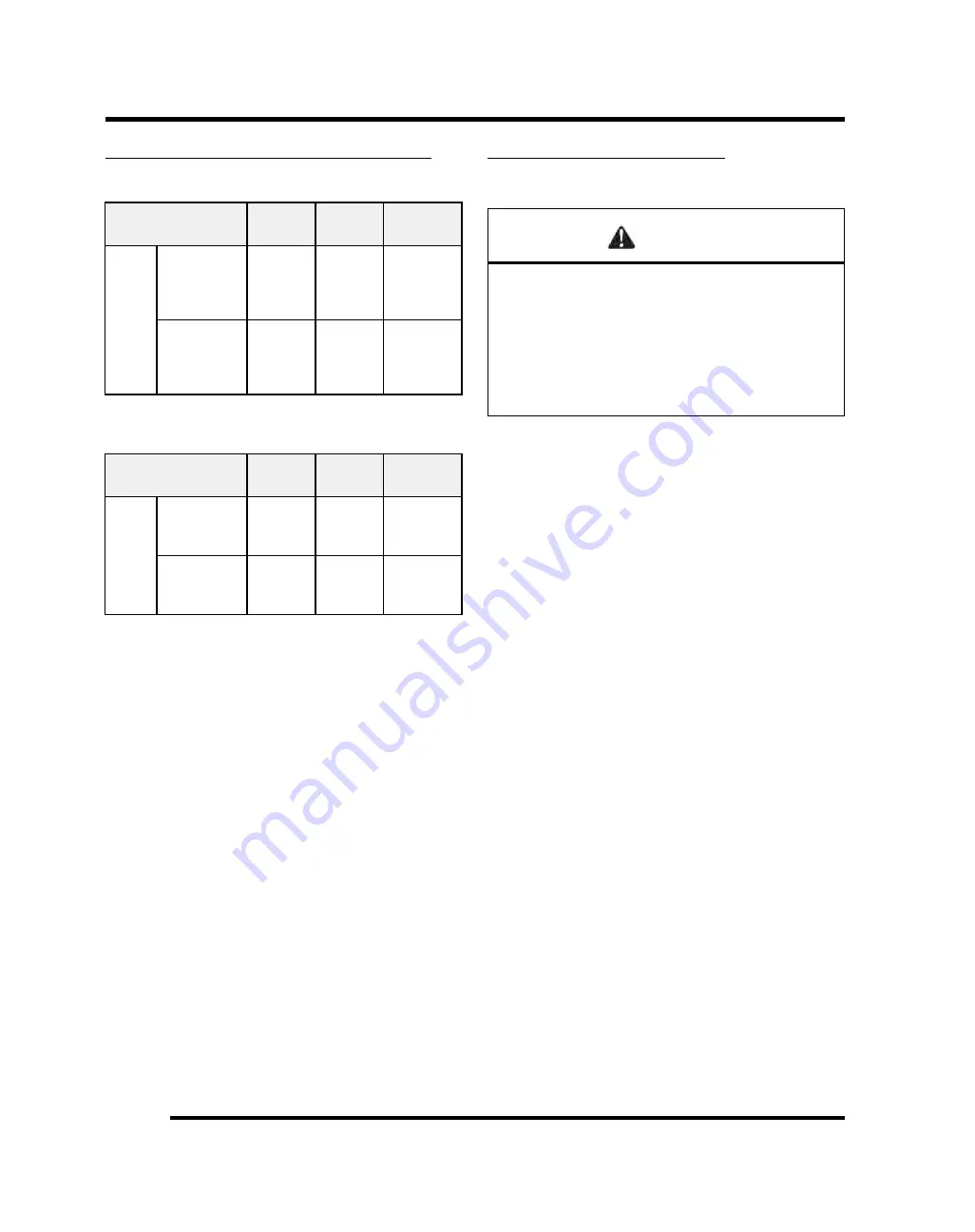
6.4
9924707 - 2013–2014
RZR
800 Service Manual
© Copyright 2013 Polaris Sales Inc.
HIGH ALTITUDE CLUTCH CHARTS
RZR / RZR S / RZR 4
Altitude
Shift
Weight
Drive
Spring
Driven
Spring
Me-
ters
(Fee-
t)
0-1500
(0-5000)
23-62
(56323-
37)
Green
(70437-
89)
Blk /
Almond
(704316-
7)
1500-3700
(5000 -
12000)
23-58
(B)
(13229-
11)
Green
(70437-
89)
Blk /
Almond
(704316-
7)
RZR EPS (EBS Model)
Altitude
Shift
Weight
Drive
Spring
Driven
Spring
Me-
ters
(Fee-
t)
0-1500
(0-5000)
23-66
(56327-
63)
Green
(70437-
89)
Red
(323445-
2)
1500-3700
(5000 -
12000)
23-62
(56323-
37)
Green
(70437-
89)
Red
(323445-
2)
PVT SYSTEM OVERVIEW
General Operation
WARNING
All PVT maintenance or repairs should be performed by
a certified Polaris Master Service Dealer (MSD)
technician who has received the proper training and
understands the procedures outlined in this manual.
Because of the critical nature and precision
balance incorporated into the PVT components, it is
absolutely essential that no disassembly or repair
be made without factory authorized special tools
and service procedures.
The Polaris Variable Transmission (PVT) consists of
three major assemblies:
1) The Drive Clutch
2) The Driven Clutch
3) The Drive Belt
The internal components of the drive clutch and driven
clutch control engagement (initial vehicle movement),
clutch upshift and backshift. During the development of
the Polaris vehicle, the PVT system is matched first to the
engine power curve; then to average riding conditions
and
the
vehicle’s
intended
usage.
Therefore,
modifications or variations of components at random are
never recommended. Proper clutch setup and careful
inspection of existing components must be the primary
objective when troubleshooting and tuning.
Drive Clutch Operation
Drive clutches primarily sense engine RPM. The two
major components which control its shifting function are
the shift weights and the coil spring. Whenever engine
RPM is increased, centrifugal force is created, causing
the shift weights to push against rollers on the moveable
sheave, which is held open by coil spring preload. When
this force becomes higher than the preload in the spring,
the outer sheave moves inward and contacts the drive
belt. This motion pinches the drive belt between the
spinning sheaves and causes it to rotate, which in turn
rotates the driven clutch.
At lower RPM, the drive belt rotates low in the drive
clutch sheaves. As engine RPM increases, centrifugal
force causes the drive belt to be forced upward on drive
clutch sheaves.
CLUTCHING
Summary of Contents for RZR 800 2013
Page 4: ......
Page 6: ......
Page 136: ...3 74 9924707 2013 2014 RZR 800 Service Manual Copyright 2013 Polaris Sales Inc NOTES ENGINE...
Page 486: ...IX 6 9924707 2013 2014 RZR 800 Service Manual Copyright 2013 Polaris Sales Inc...
Page 487: ...2013 2014 RANGER RZR 800...
Page 488: ...2013 2014 RANGER RZR 800...
Page 489: ...2013 2014 RANGER RZR 800 EPS...
Page 490: ...2013 2014 RANGER RZR 800 EPS...
Page 491: ...2013 2014 RANGER RZR S 800...
Page 492: ...2013 2014 RANGER RZR S 800...
Page 493: ...2013 2014 RANGER RZR S 800 INT L...
Page 494: ...2013 2014 RANGER RZR S 800 INT L...
Page 495: ...2013 2014 RANGER RZR 4 800...
Page 496: ...2013 2014 RANGER RZR 4 800...
Page 497: ...2013 2014 RANGER RZR 4 800 EPS...
Page 498: ...2013 2014 RANGER RZR 4 800 EPS...