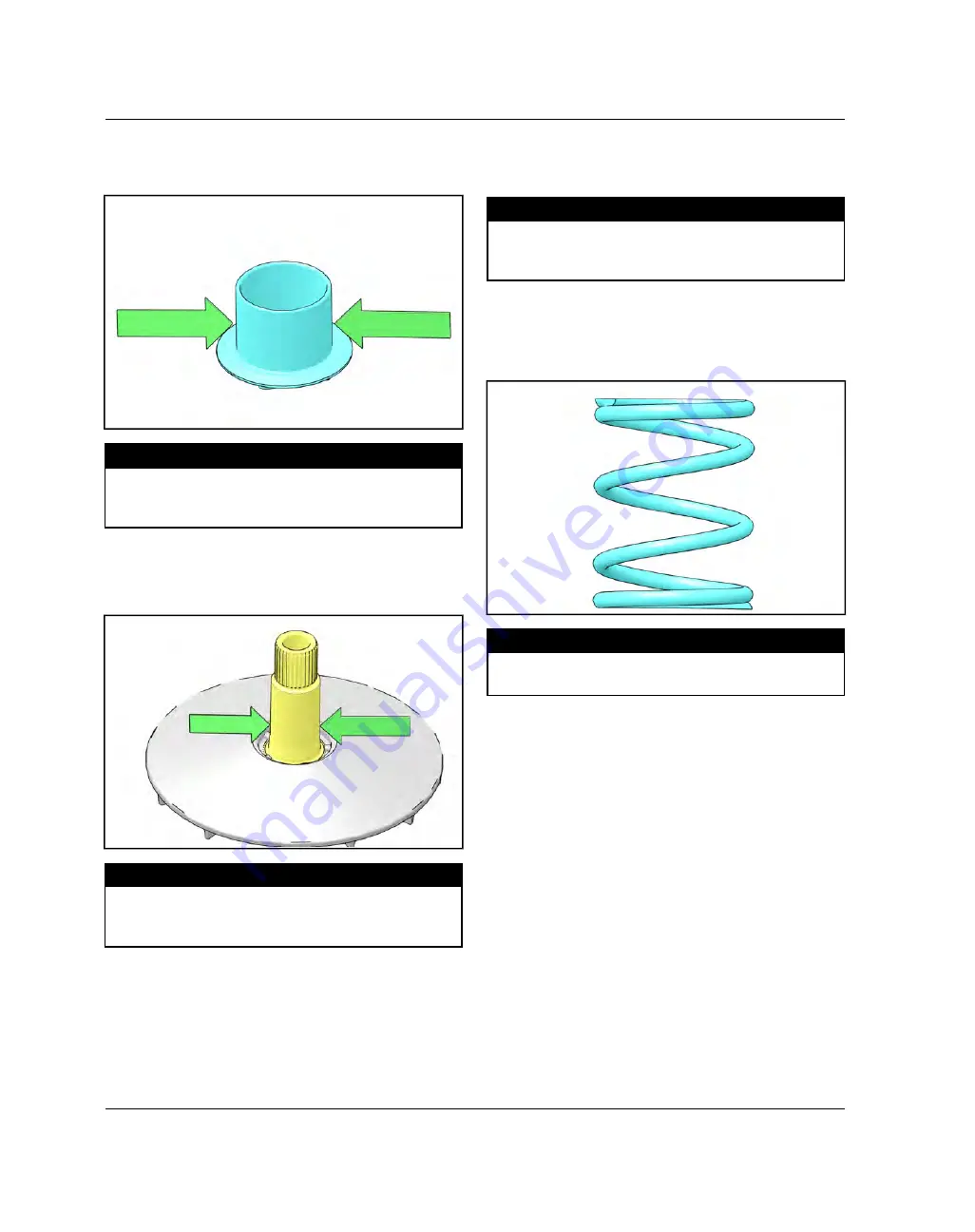
5.24
9928487 R01 - 2018 RANGER XP 1000 Service Manual
© Copyright Polaris Industries Inc.
7. Inspect the flange sleeve for pitting, grooving, or
damage. Measure the outside diameter and compare
to specifications. Replace if necessary.
TORQUE
Drive Clutch Flange Sleeve Diameter:
Service Specification:
1.693” (42.98 mm)
Service Limit:
1.692” (42.993 mm)
8. Inspect surface of shaft for pitting, grooves or
damage. Measure the outside diameter and compare
to specifications. Replace the drive clutch assembly if
shaft is worn or damaged.
MEASUREMENT
Shaft Diameter:
1.413” (35.913 mm)
Service Limit:
1.416” (35.975 mm)
9. Visually inspect Vespel® thrust washers for damage.
Measure the thickness and compare to specification.
Replace if worn or damaged.
MEASUREMENT
Thrust Washer Thickness:
Standard:
0.030 – 0.040” (0.76 - 0.96 mm)
Service Limit:
0.020” (0.50 mm)
DRIVE CLUTCH SPRING INSPECTION
• Measure the Drive Clutch Spring height. Compare to
specification and replace if necessary.
MEASUREMENT
Drive Clutch Spring Height:
3.76 in (95.43 mm)